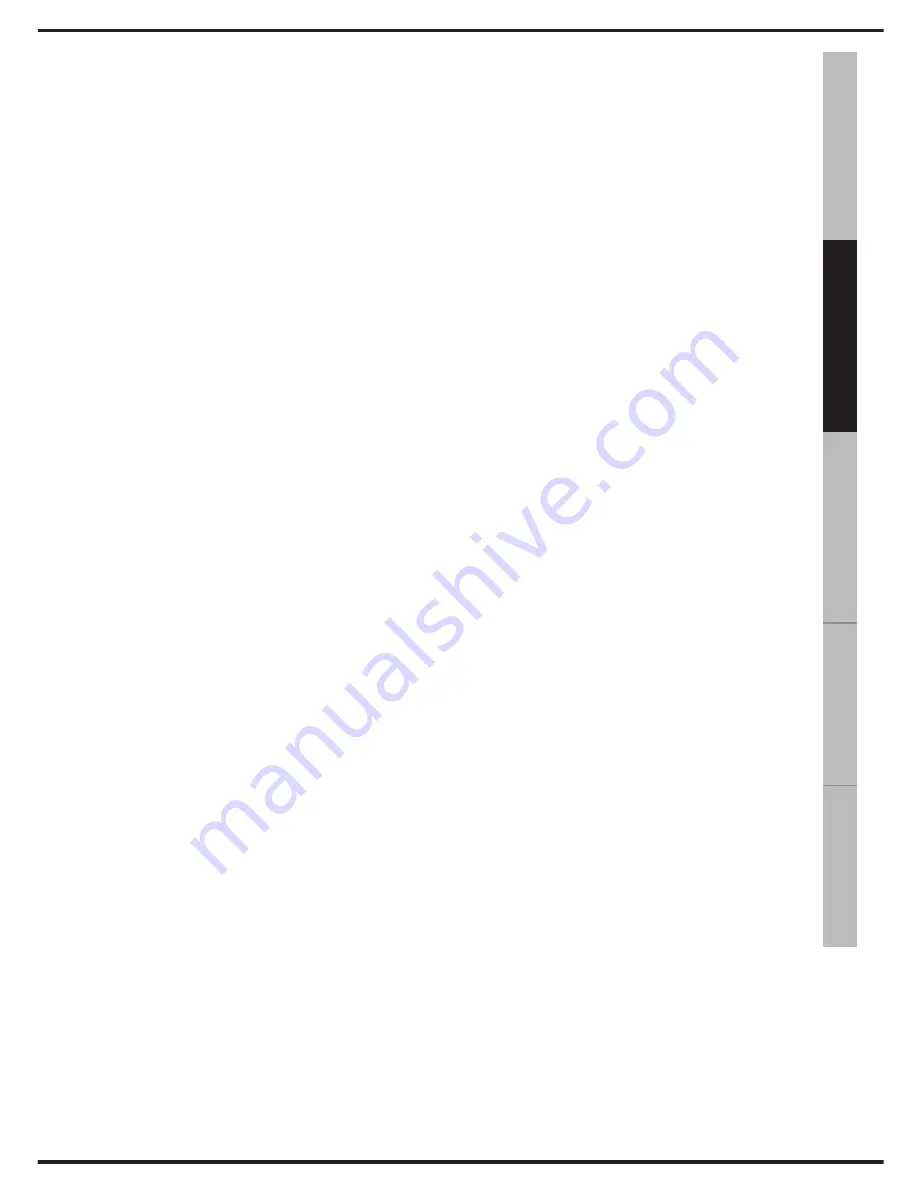
13
ESP
AÑOL
FRANÇAIS
DEUTSCH
ENGLISH
IT
ALIANO
3.
According to the kind of material,
regulate the electronic inductance (Fig.
1 –6). (Step 4, Fig8)
4.
Connect the earth clamp to the
workpiece.
5.
Start to weld maintaining
an arc length of between 5 to 10 mm.
6.
Regulate the wire speed (Knob Fig. 1
– 7).For best results regulate the speed
(Knob 9) until a loud, regular sizzling
sound is heard (similar to that of frying
bacon).
Always perform a trial run using a metal
sheet that is free of grease, rust or
paint.
For best results heed the following
advice:
1.
Keep the torch at a 45° angle to the
workpiece. Keep the gas nozzle
(Fig.4A) app. 6 mm away from the
workpiece.
2.
Move the torch smoothly.
3.
Weld using small zigzag movements
so as to be able to regulate the size of
the weld as desired.
4.
Do not weld in windy surroundings.
Draughts can disperse the gas from the
welding pool causing porous welding
results.
5.
Ensure the wire is clean:
never use rusty welding wire.
6.
Keep the torch cable straight.
7.
Clean the wire-feed guide with
compressed air when changing spools.
8.
Remove dust from the air intake grills
regularly,
using
low-pressure
compressed
air.
Always point the jet of air outwards to
avoid dirt being forced into the unit.
8.2 SYNERGIC MIG WELDING
In synergic MIG welding (with gas)
mode the welder tunes itself
automatically to suit the type of material
to be welded and the thickness of the
workpiece. Contrary to manual mode,
a series of predefined programmes to
suit all requirements are available.
It should be noted, however, that certain
parameters can be set manually. More
information in this respect will be
provided in later sections.
To select this mode, turn knob 5 (Fig.1)
to one of the SYNERGIC settings.
Proceed as follows for synergic MIG
welding: 1-
Select one of the following
programmes according to the type of
material to be welded (Selector knob 7,
Fig1)
• Al-Mg 0.8:
The permissible thickness
range is 0.8 to 4 mm.
• Al-Mg 5 1.0:
The permissible
thickness range is 0.9 mm to 5 mm.
• Al-Si 12 1.0:
The permissibile
thickness range is 0.8mm to 5 mm
(Spool Gun welding is recommended for
this type of wire).
•
SS 0.8:
ideal for welding stainless
steel (Ni-Cr) 0.8mm in diameter.
The permissible thickness range is 0.8
mm to 5 mm.
•
SG2 0.8:
ideal for welding SG2 or SG3
materials
0.8mm
in
diameter.
The permissible thickness range is 0.8
mm to 3.2 mm.
• Cu-Si 3 0.8:
Ideal for Cu-Si3 having a
diameter of 0.8 mm. Such materials can
be braze welded, particularly zinc-
plates iron sheets to be used by car
manufacturers
The permissible thickness range is 0.8
to 4 mm.
2-
Select the workpiece thickness using
Knob 2 of Figure 8. The display panel
(Fig. 1 – 1) will display the selected
thickness parameter (in mm) for a few
seconds.
3-
Turn knobs 6 and 7 to a mid-way
position.
4-
Connect the earth clamp to the
workpiece.
5-
Start to weld maintaining an arc
length of between 5 to 10 mm.
A high-quality result is usually achieved
Summary of Contents for QUEEN 210
Page 1: ...Instructionsmanual QUEEN 210 ...
Page 2: ... MB ...
Page 3: ... MB QUEEN 210 ...
Page 6: ......
Page 8: ...2 0 WARNING SYMBOLS WARNING SYMBOLS ...
Page 23: ...17 ...
Page 24: ...Cod 910 100 310GB REV01 ...