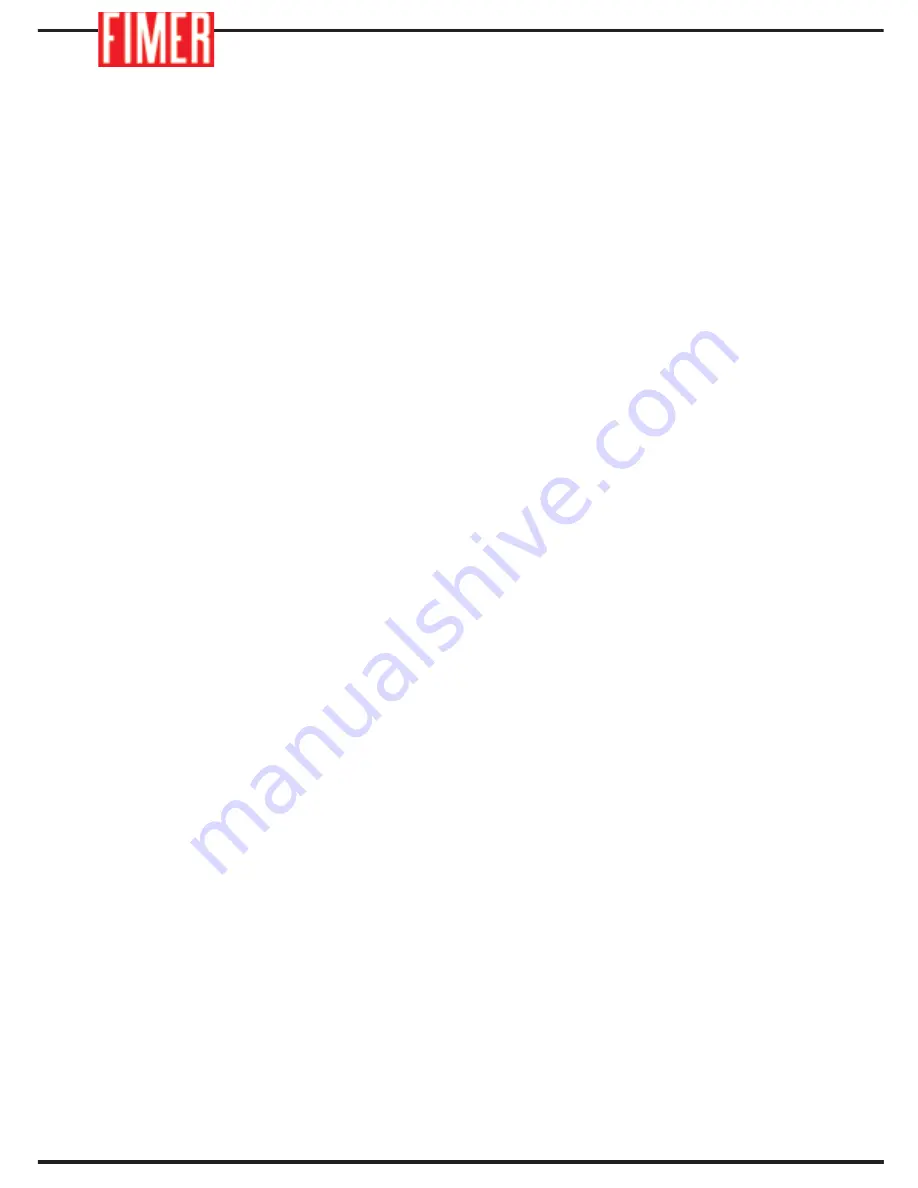
10
5. OUTPUT CONNECTIONS
The welding cables are connected using
fast-connector plugs.
5.1 MIG welding connections
1)
Connect the earth cable to the -
socket on the front panel of the unit (Fig
1 – 13). Lining up the peg and the
groove, insert the plug and screw it in
well clockwise. Do not over-tighten.
2)
Connect the torch to the appropriate
Euroconnector (Fig. 1 – 11) and screw in
clockwise up to stop. Do not over-tighten.
WARNING:
The life of the MIG torch will
be extended if the following items are
checked regularly: gas nozzle (Fig4A)
and wire feeder (Fig4B).
These items must be kept clean and
intact.
Replace the wire-feeder guide when the
wire does not flow through smoothly
5.2 MMA Welding connections
The welder is supplied in the correct
polarity configuration for MMA welding:
Check the polarity inversion settings
before making the output connections
(Fig.3 – 20) as per Line 1 of Fig 5.
1)
Connect the electrode clamp to the +
socket on the front panel of the unit (Fig
Fig1 – 14). Lining up the peg and the
groove, insert the plug and screw it in
well clockwise. Do not over-tighten.
2)
Connect the earth cable to the -
socket on the front panel of the unit (Fig
1 – 13). Lining up the peg and the
groove, insert the plug and screw it in
well clockwise. Do not over-tighten.
WARNING:
Some electrodes require
negative polarity on the electrode clamp
and positive polarity on the earth cable.
In that case, invert the connections!
Always check the electrode packaging
for instructions regarding the required
polarities!
The welding cables are connected using
fast-connector plugs.
6. WELDING WIRE INSTALLATION
(For MIG welding only) Skip this chapter
if you intend welding in MMA mode
Install the welding wire as follows,
referring also to Figure 3.
WARNING:
Before installing the
welding wire always remove the gas
nozzle (Fig. 4A) and the wire feeder
(Fig.4B) from the torch.
1.
Disconnect the mains power supply
(Fig. 2 -18)
2.
Unscrew the central knurled bobbin
of the spool (19) and remove the empty
spool if there is one.
3.
Remove the plastic protection from
the new spool and install the spool on
the holder (Fig – 19). Reinstall the
knurled bobbin. Beware: The smaller
knob at the centre of the bobbin is, in
fact, the wire brake. If it is too tight it
could provide too much braking power
and stop the wire-feed motor from
functioning properly. On the other
hand, if it is not tightened sufficiently it
may not provide sufficient braking
power to stop wire-feeding once the
welding operation has been completed.
4.
Unscrew and raise the knob (25),
then lower the lower roller of the wire
feeder (24). If necessary, remove any
wire remnants left by the previous
spool.
5.
Place the tip of the wire into the input
guide (22) and push it along until it
reaches the wire feeder roller.
6.
Lower the rollers (24) and replace the
plastic knob (25) of the wire tension
regulator. Tighten the knob with care. If
it is too tight the wire will not flow
smoothly and the feeder motor can be
damaged. If, on the other hand, it is too
loose the feeder motor will not be able
Summary of Contents for QUEEN 210
Page 1: ...Instructionsmanual QUEEN 210 ...
Page 2: ... MB ...
Page 3: ... MB QUEEN 210 ...
Page 6: ......
Page 8: ...2 0 WARNING SYMBOLS WARNING SYMBOLS ...
Page 23: ...17 ...
Page 24: ...Cod 910 100 310GB REV01 ...