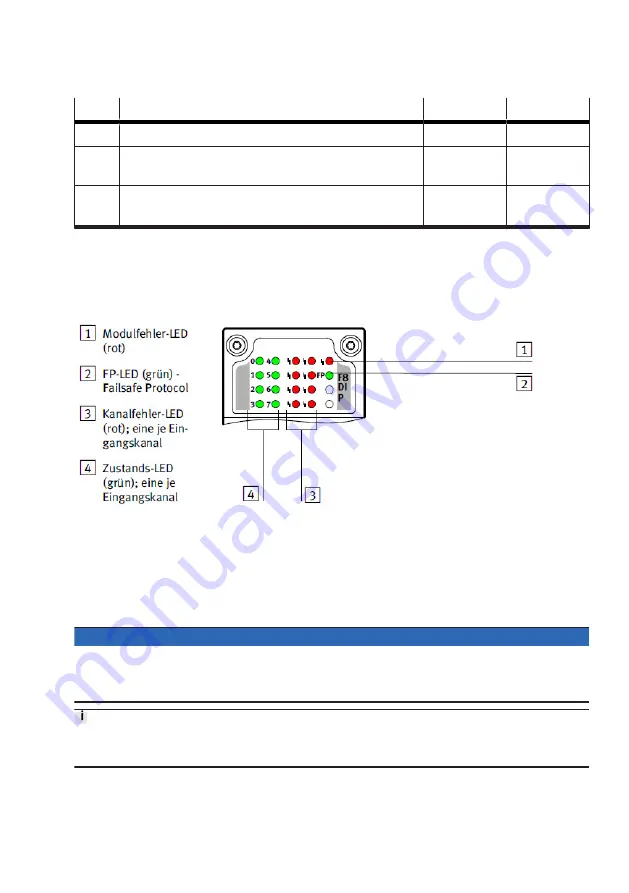
Festo — CPX-F8DE-P — 2022-10d
Operation
69
No.
Module
I address
O address
4
MPA: pneumatic interface
-
-
5
MPA: pneumatic module
VMPA1-FB-EMG-8 [8DO]
-
15
6
MPA: pneumatic module
VMPA2-FB-EMG-4 [4DO]
-
16
Tab. 30: Input and output addresses for the example
5
Operation
5.1
LED status indication
Fig. 34: LED display of the input module CPX-F8DE-P
The following LEDs are on in the normal operating status:
–
FP-LED
2
–
Status LEDs
4
of the active input channels
The status LEDs on inactive input channels and the module error LEDs
1
and channel error LEDs
3
do not light.
NOTICE
The designations of the LEDs correspond to the physical contacts E0 to E7.
• Note the special position of the input signals in the input image of the CPX-F8DE-P
pattern of the output and input data (F-user data).
Detailed information on error characteristics can be found in