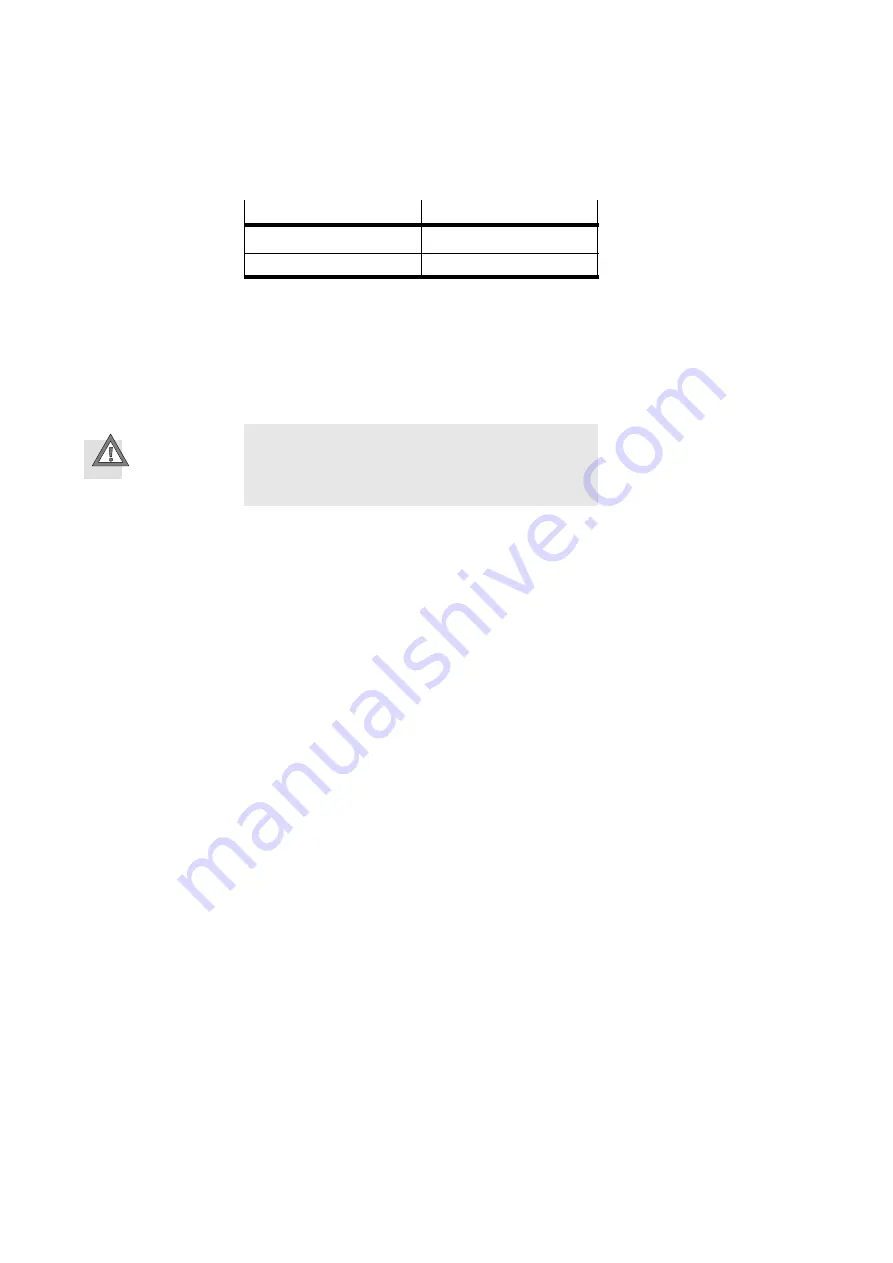
2. Fitting and commissioning
2-10
Festo P.BE-CB-COMP-EN en 0211a
Connection
Plugs/sockets
Power supply socket
PG9 or PG13.5
Sensors, actuators
PG7
In order that the completely fitted Checkbox complies with
the IP protection class:
S
Tighten the union nuts of the plugs by hand.
S
Seal the unused sockets with the protective caps sup-
plied.
Caution
Long I/O signal cables reduce the immunity to interfe-
rence. Do not, therefore, exceed the maximum permitted
I/O signal cable length of 30 m.
Summary of Contents for Checkbox Compact CHB-C-C
Page 2: ...Festo Checkbox is a registered trademark of Festo AG Co D 73726 Esslingen Deutschland...
Page 4: ...Contents and general instructions II Festo P BE CB COMP EN en 0211a...
Page 5: ...Contents and general instructions III Festo P BE CB COMP EN en 0211a...
Page 17: ...System summary 1 1 Festo P BE CB COMP EN en 0211a Chapter 1...
Page 28: ...1 System summary 1 12 Festo P BE CB COMP EN en 0211a...
Page 29: ...Fitting and commissioning 2 1 Festo P BE CB COMP EN en 0211a Chapter 2...
Page 49: ...The I O module 3 1 Festo P BE CB COMP EN en 0211a Chapter 3...
Page 60: ...3 The I O module 3 12 Festo P BE CB COMP EN en 0211a...
Page 61: ...I O module extensions of the Checkbox PLC 4 1 Festo P BE CB COMP EN en 0211a Chapter 4...
Page 79: ...Teaching parts 5 1 Festo P BE CB COMP EN en 0211a Chapter 5...
Page 89: ...Testing parts 6 1 Festo P BE CB COMP EN en 0211a Chapter 6...
Page 98: ...6 Testing parts 6 10 Festo P BE CB COMP EN en 0211a...
Page 99: ...Maintenance 7 1 Festo P BE CB COMP EN en 0211a Chapter 7...
Page 103: ...Technical appendix A 1 Festo P BE CB COMP EN en 0211a Appendix A...
Page 130: ...A Technical appendix A 28 Festo P BE CB COMP EN en 0211a...
Page 131: ...Index B 1 Festo P BE CB COMP EN en 0211a Appendix B...
Page 132: ...B Index B 2 Festo P BE CB COMP EN en 0211a Contents B Index B 3...