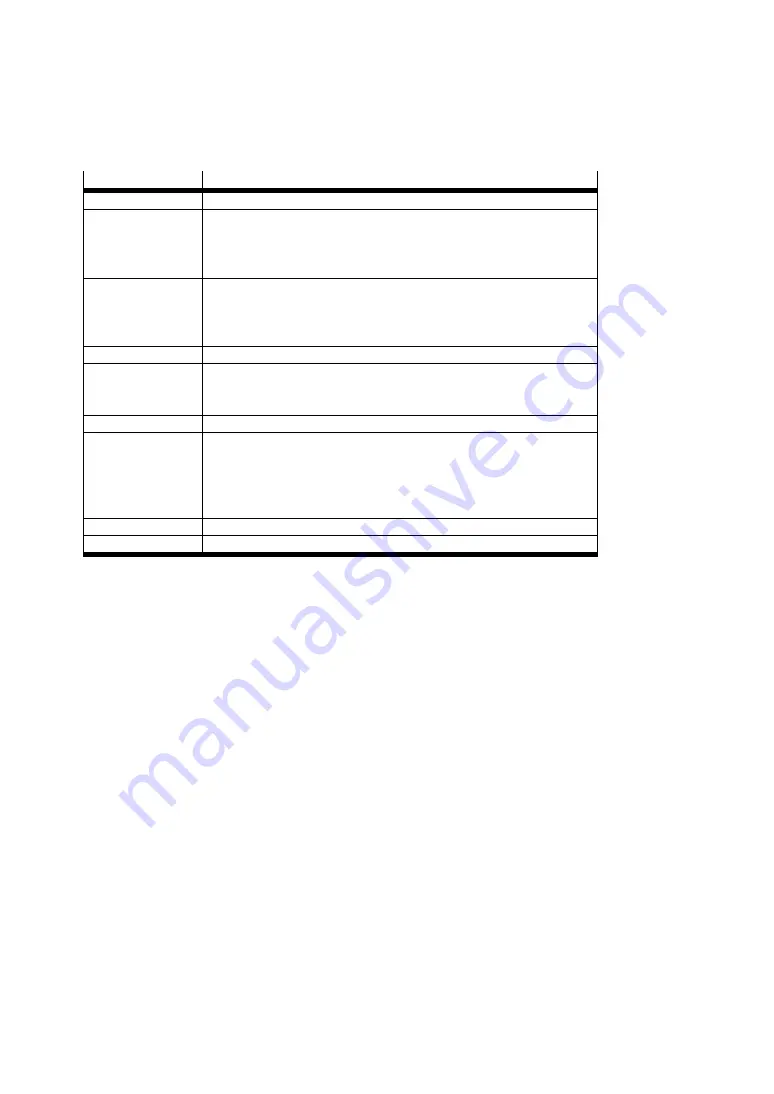
B
Glossary
40
Festo – GDCP-CMMS-AS-G2-S1-EN – 1306NH – English
B
Glossary
Term/abbreviation
Description
Cat.
Safety category in accordance with EN ISO 13849-1, Stages 1-4.
Emergency off
In accordance with EN 60204-1: Electrical safety in case of emergency by
switching off the electrical energy to all or part of the installation.
Emergence off is to be used where a risk of electric shock or other electrical
risk exists.
Emergency stop
In accordance with EN 60204-1: Functional safety in an emergency by
bringing a machine or moving parts to a stop.
Emergency stop is used to stop a process or a movement if this creates a
hazard.
FCT
Festo Configuration Tool, software for configuration and commissioning.
MTTFd
Mean Time To Failure (dangerous): Time in years until the first dangerous
failure will have occurred with 100 % probability, in accordance with
EN ISO 13849-1.
PL
Performance Level in accordance with EN ISO 13849-1: Stages a … e.
Safety switching
device
Device for execution of safety functions or achievement of a safe status of
the machine through switching off of the energy supply to dangerous
machine functions. The desired safety function is achieved only in
combination with other measures for risk reduction, although switch-off can
occur on a motor controller, for example.
STO
Safe Torque Off.
T
Duration of use in accordance with EN ISO 13849-1.
Tab. B.1
Terms and abbreviations