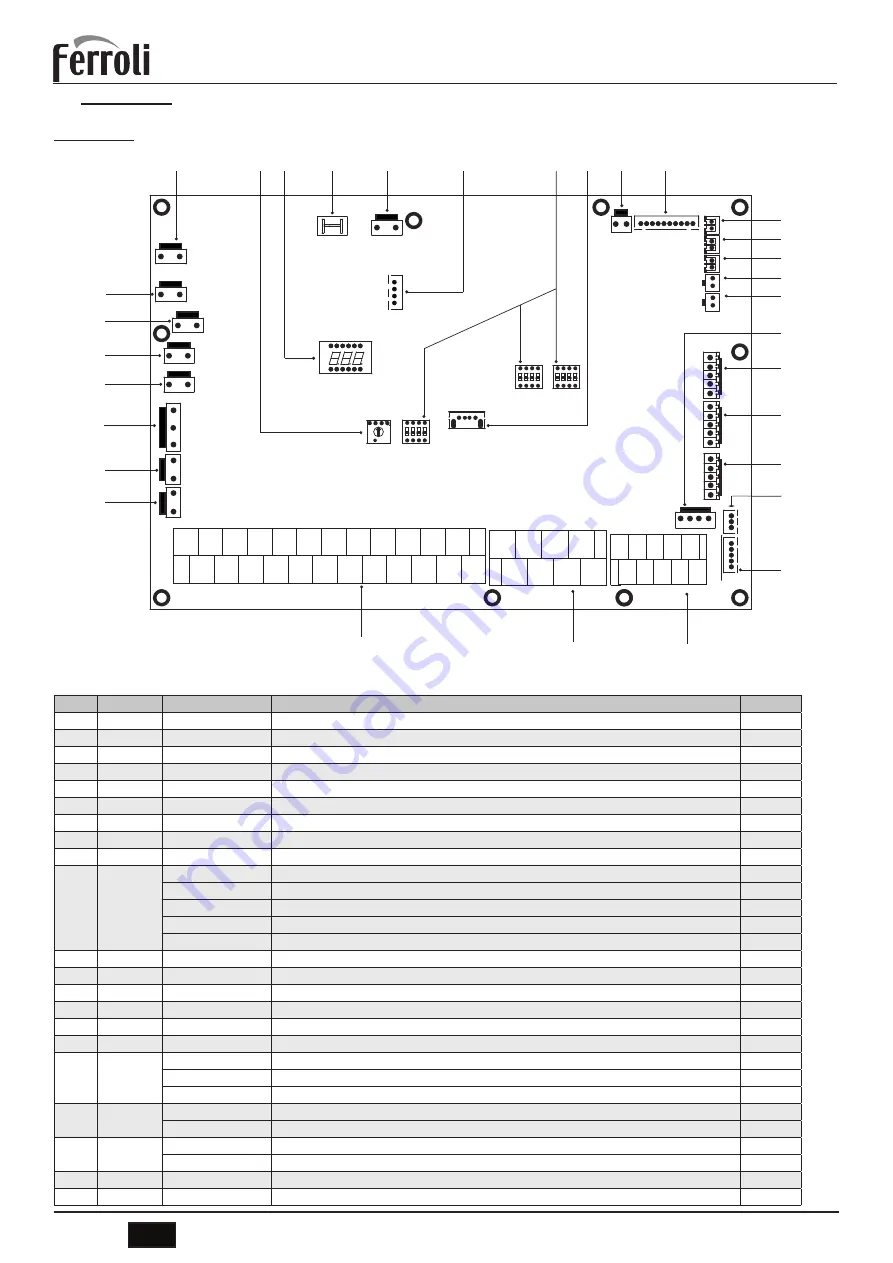
34
EN
Cod. 3541V950 - Rev. 00 - 05/2021
OMNIA S 3.2
7.6.3 User connections
All the connections have to be done on the terminals of the hydronic board placed in the electric box.
Hydronic board
&1
&1
&1
6
',6
&1
&1
&1
&1
&1
&1
&1
&1
&1
&1
6
&1
&1
6
6
&1
&1
&1
&1
&1
&1
&1
&1
&1
&1
1
A
2
B
3
X
4
Y
5
E
6
P
7
Q
8
E
9
H1
10
H2
1
SL1
2
SL2
3
H
4
C
5
6
1ON
7
1OFF
8
9
10
11
12
3
2
4
2
N
21
N
20
IBH1
19
18
13
14
L1
15
16 17
N
22
2ON
2OFF
P_c P_o P_s P_d
TBH
N
N 3ON
3OFF
N
N
CN11
25
HT
29
30
31
DFT2
32
DFT1
26
R2
27
AHS1
28
AHS2
N
R1
CN7
CN30
fig. 21 - Hydronic board
Order
Port
Code
Assembly unit
Note
1
CN21
POWER
Power supply to hydronic board
B
2
S3
/
Rotary dip switch
/
3
DIS1
/
Digital display
/
4
CN5
GND
Ground to hydronic board
B
5
CN28
PUMP
Power supply to internal water pump Pi
B
6
CN25
DEBUG
Port for IC programming
/
7
S1, S2, S4 /
Dip switch
/
8
CN4
USB
Port for USB programming
/
9
CN8
FS
Connection to internal water flow switch
/
10
CN6
T2 *
Port for temperature probe of refrigerant liquid side temperature of indoor unit (heating mode)
B
T2B *
Port for temperature probe of refrigerant gas side temperature of indoor unit (heating mode)
B
TW_in *
Port for temperature probe of inlet water temperature of plate heat exchanger
B
TW_out *
Port for temperature probe of outlet water temperature of plate heat exchanger
B
T1 *
Port for temperature probe of final outlet water temperature of indoor unit
B
11
CN24
Tbt1
Port for temp. sensor probe in the plant tank
A
12
CN16
Tbt2
Reserved
/
13
CN13
T5
Port for temp. sensor probe in the DHW boiler
A
14
CN15
Tw2
Port for outlet water for zone 2 temp. probe probe
A
15
CN18
Tsolar **
Port for solar panel temp. sensor
A
16
CN17
PUMP_BP
PWM signal to internal water pump Pi
B
17
CN31
HT
Control port for room thermostat (heating mode)
1
COM
Power port for room thermostat
1
CL
Control port for room thermostat (cooling mode)
1
18
CN35
SG
Port for smart grid (grid signal)
1
EVU
Port for smart grid (photovoltaic signal)
1
19
CN36
M1 M2
Reserved
/
T1 T2
Reserved
/
20
CN19
P Q
Reserved
/
21
CN14
A B X Y E
Port for communication with the display panel
B
Summary of Contents for OMNIA S 3.2
Page 65: ......
Page 66: ......
Page 67: ......
Page 68: ...FERROLI S p A Via Ritonda 78 a 37047 San Bonifacio Verona ITALY www ferroli com Made in Italy...