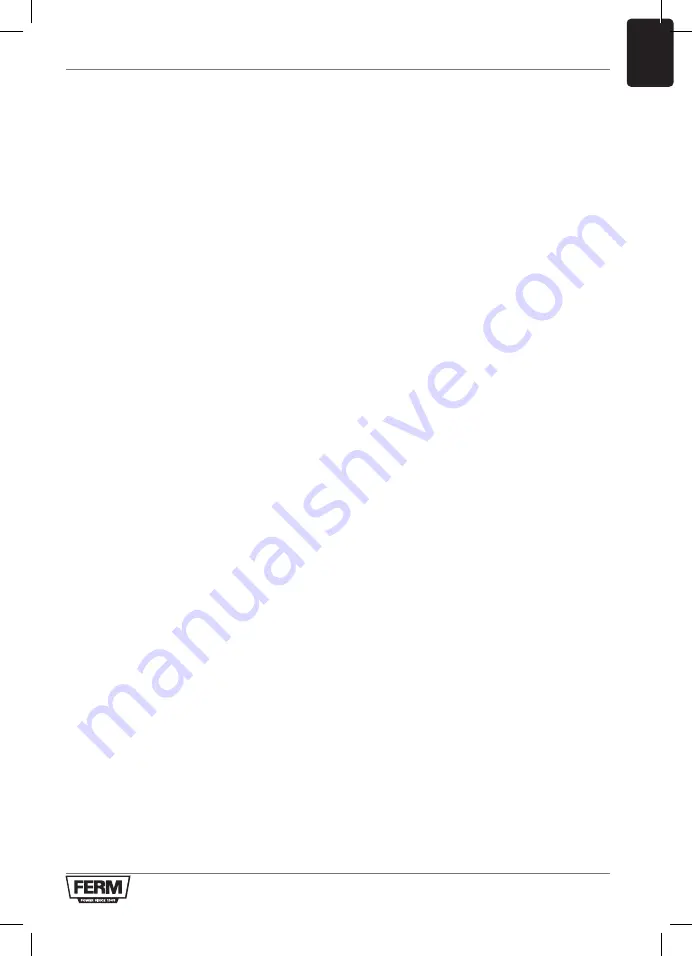
7
EN
a. General information about electric arc
welding
The temperature of the arc amounts to approx.
7000° Celsius, so the end of the electrode and the
workpiece fuse. For as long as the arc is
maintained, the electrode will melt and supply the
necessary welding material to the parts to be
joined. The distance between the electrode and
the workpiece must be as short as possible
(approx. 1.5 - 4 mm) depending on the diameter
and type of electrode. The current needed for
welding is supplied by the welding appliance.
The power required by the welding appliance
depends on the work to be done.
Make sure that the electrodes are completely dry,
as moist electrodes cause problems. If the
electrode sticks to the workpiece during welding
your current intensity is set too low.
b. The electrode
• The electrode consists of a metal core
enclosed by a coating. The coating has the
most important purpose of protecting the
welding pool and the transferring droplets
against oxygen and nitrogen in the
surrounding air. The electrode melts during
welding. A part of the coating vaporises so a
protective gaseous shield originates.
part of the coating floats on the welding pool
(it is lighter than steel) and also protects the
cooling weld. After cooling this coating
becomes a solid but easily removable slag on
the welded joint.
• Handle the electrodes with care so the
coating is not broken. Make sure that the
electrodes are thoroughly dry, so store them
in a moisture-free place.
• It is of great importance to use the right
electrode to make a good and strong welded
joint. A universal electrode will in many cases
be suitable for your work.The electrode
packaging mentions in which positions
welding can be done with the electrodes
concerned (above the head, downwards, etc.
bearing in mind the speed of melting of the
electrode). Separate electrodes are
commercially available for the welding of
types of stainless steel and cast iron. Consult
your dealer about purchasing the right
electrode.
c. Protective clothing
Wear thoroughly covering clothing so that the
likelihood of the skin being burnt by ultraviolet
radiation or splashes of metal is minimised.
Preferably wear cotton overalls, welding gloves
and safety shoes. Make sure that welding spatter
cannot end up in gloves or shoes.
A (leather) welding apron stops burning and
sparks damaging overalls.
d. Face protection
Fig. 2
Use a good welding mask with (dark) welding
glass and protective glass. Check that both
glasses are correctly fitted (well-fastened and not
allowing any sunlight in).
The welding mask protects the welder against
radiation, heat and weld spatter released during
the welding process. This also reduces the
inhalation of welding fumes. The invisible
ultraviolet rays cause so-called “welder’s flash”.
This already originates after a few seconds of
looking into the electric arc.
Avoid the effects of this radiation and high
temperatures on the face and other exposed body
parts such as the neck and arms.
Protect yourself against the dangerous effects of
the electric arc and keep persons who are not
participating in the work at least 15 m from the arc.
Persons or assistants working in the vicinity of the
electric arc must be advised of the hazards and
they must be equipped with the required
protective gear. If required, set up protective
walls.
e. Working environment
• Ensure a well ventilated working environment.
Gases are released when welding that are a
danger to your health.
• Remove all flammable objects from the
working environment. Welding causes sparks
and hot metal.
• Make sure that cooling water is present in the
vicinity of workplace. Do not leave just welded
(hot) workpieces unattended in the workplace.
Cool the workpiece before leaving the
workplace.
Protection against radiation and burns
• At the work place, the hazard to the eyes
must be indicated by a sign stating “Caution!
Do not look at the flames!” The workstations
must be shielded as much as possible in such
a manner that personnel standing in the
vicinity of the workstation are protected. Keep
unauthorized personnel away from the
welding work.
Summary of Contents for WEM1042
Page 2: ...2 10 1 2 4 6 5 60 70 3 Fig 1 Fig 2 Fig 3...
Page 137: ...137 RU EN60974 6 O 1 3 50 60 I1eff I2 IP21S S 12 H U0 U1 U2 EMC 60974 10 O O...
Page 138: ...138 RU O O O 10 2...
Page 140: ...140 RU P 2 O 2 O 5 4 O O a O b c d e O 7000 C 1 5 4 b...
Page 141: ...141 RU O O O c d P 2 15 e O O...
Page 142: ...142 RU P 3 O 60 70 O O P 1 5...
Page 143: ...143 RU 3 3 3 H 2012 19 EU...
Page 145: ...145 BG EN60974 6 1 3 50 Hz 60 Hz I1eff I2 IP21S 12 mm H U0 U1 U2 IEC 60974 10...
Page 146: ...146 BG 0 10 2...
Page 147: ...147 BG VDE0100 16 RT14 20 10 x 38 AC 400 V 16A IEC 60269 Chint 230 16 1 5 mm2 3 20 2...
Page 148: ...148 BG 2 cm 5 cm 4 7 0000 1 5 4 mm b...
Page 149: ...149 BG d 2 15 3...
Page 150: ...150 BG 600 700 1 5...
Page 151: ...151 BG 3 3 3 2012 19 EU...
Page 153: ...153 Exploded view...
Page 154: ...154...
Page 156: ...WWW FERM COM 2020 FERM 2005 10...