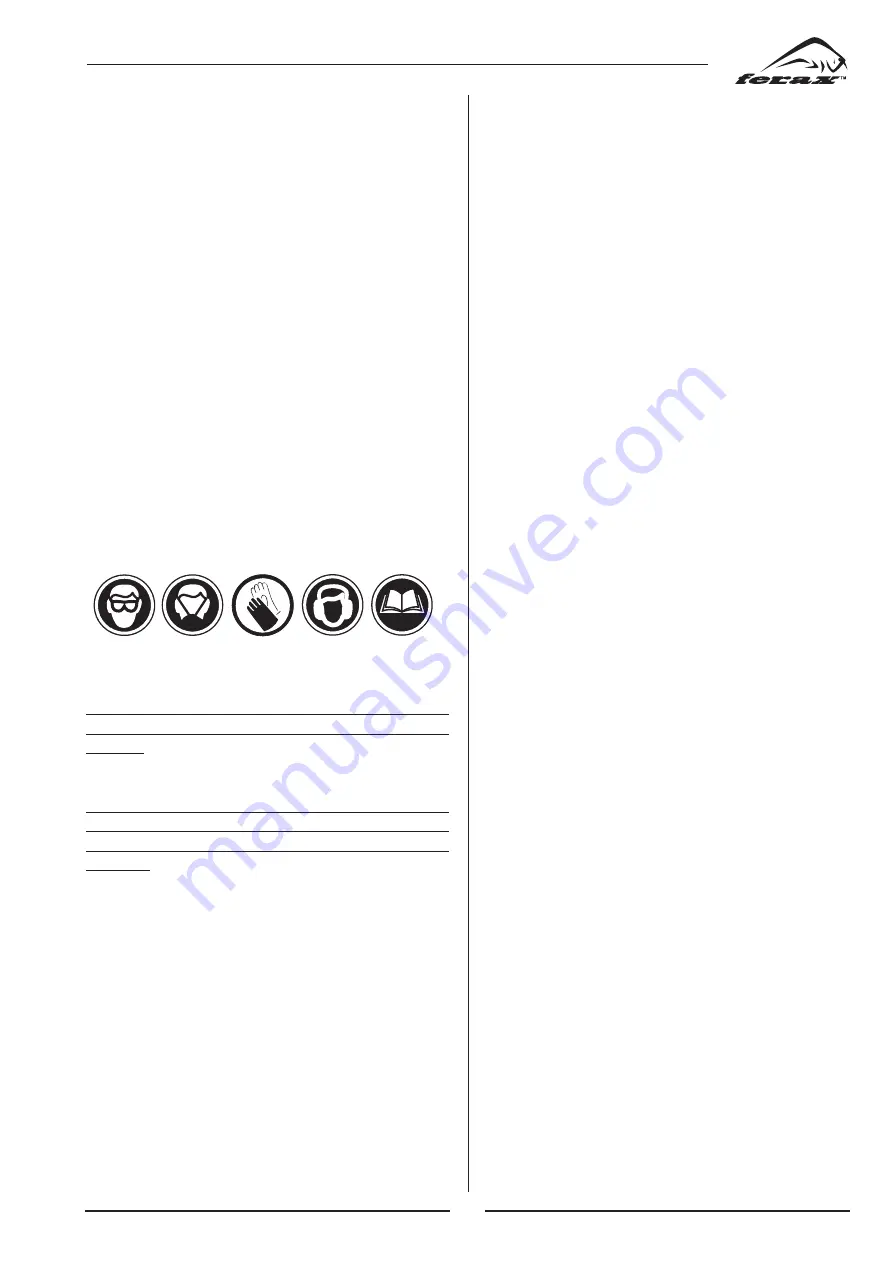
31
1.0 SAFETY NORMS
1.1 GENERAL INSTRUCTIONS
Make sure this manual is carefully read and understood
by the welder, and by the maintenance and technical
workers.
1.2 LOCATION
Welding processes of any kind can be dangerous not
only to the operator but to any person situated near the
equipment, if safety and operating rules are not strictly
observed.
These are the main precautionary measures to observe:
• Operators should protect their body by wearing clo-
sed, non-flammable protective clothing, without
pockets or turned up trousers.
• The operators should wear a non-flammable welding
helmet designed so as to shield the neck and the face,
also on the sides. It is necessary to keep the protecti-
ve lens always clean and to replace it when broken or
cracked. It is advisable to interpose a transparent
glass between the lens and the welding area. Welding
should be done in a closed area that does not open
into other working areas.
• The operators should never look at the voltaic arc
without the correct protection to the eyes. They
should always wear safety glasses with side shields
to protect from flying particles.
• The welding process must be performed on metal
coatings thoroughly cleaned from layers of rust or
paint, to avoid production of harmful fumes. The
parts degreased with a solvent must be dried before
welding.
• Welding should never be done on metals or coated
metals containing zinc, mercury, chromium, graphi-
te, lead, cadmium or beryllium unless the operator
and the people standing in the same area use an air-
supplied respirator.
1.3 SAFETY INSTRUCTIONS
For your safety, before connecting the power source to
the line, closely follow these instructions:
• An adequate two-pole switch must be inserted befo-
re the main outlet; this switch must be equipped with
time-delay fuses;
• The single-phase connection with ground must be
made with a two-pole plug compatible with the
above mentioned socket;
• The two wires of the two-pole input cable are used
for the connection with the single-phase line while
the yellow – green wire for the compulsory connec-
tion to the ground in the welding area;
• When working in a confined space, the power source
must be kept outside the welding area and the ground
cable should be fixed to the workplace. Never work
in a damp or wet area, in these conditions.
• Do not use damaged input or welding cables;
• The welding torch should never be pointed at the
operator’s or at other persons’ body;
• The power source must never be operated without its
panels; this could cause serious injury to the operator
and could damage the equipment.
1.4 FIRE PREVENTION
• Make sure that appropriate fire prevention devices
are available near to the welding area;
• All combustible material must be removed from the
welding area.
1.5 SHIELDING GAS
Use the correct shielding gas for the welding process.
Make sure that the regulator mounted on the cylinder is
working well.
Remember to keep away the cylinder from any source
of heat.
1.6 ELECTROMAGNETIC COMPATIBILITY
Before installing a MIG/MAG power source, inspect
the surrounding area checking the following points:
• Make sure that close to the power source there are no
other power supply cables, control lines, telephone
cables or other devices;
ENGLISH
1.0 SAFETY NORMS ............................................31
2.0 INSTALLATION ..............................................32
3.0 ASSEMBLY......................................................32
4.0 WELDING SHIELD MAINTENANCE ..........33
5.0 INSTALLATION OF THE WELDING
WIRE ................................................................33
6.0 MIG WELDING ...............................................34
7.0 GAS WELDING ...............................................34
8.0 PREPARATION FOR WELDING ...................34
9.0 CONNECTION OF THE GAS CYLINDER
AND REGULATOR .........................................34
10.0 NO GAS WELDING ........................................35
11.0 PREPARATION FOR WELDING ...................35
12.0 ADVANTAGES OF NO GAS WELDING ......35
13.0 WELDING PROCEDURES .............................35
14.0 REPLACEMENT OF THE WIRE SPOOL......36
15.0 WELDING TIPS...............................................36
16.0 ADJUSTMENT OF THE POWER
SOURCE ...........................................................36
17.0 WELDING DISCONTINUITIES AND
DEFECTS .........................................................37