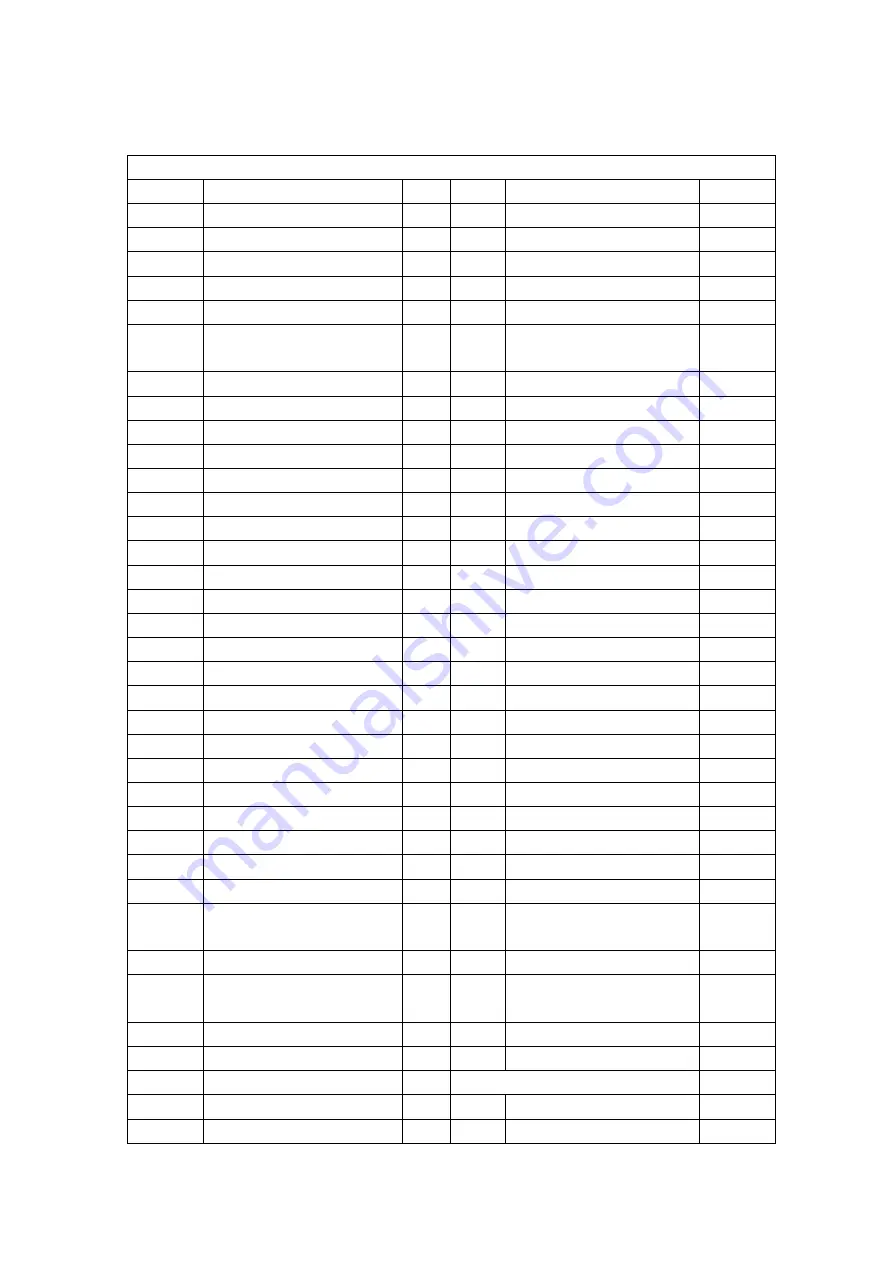
18
7. Explore view and spare parts list
Spare parts list
No.
NAME
QTY
NO.
NAME
QTY
1
sandpaper
1
46
right Connection block
1
2
adhibit tray
1
47
left Connection block
1
3
wool mat
1
48
cross-flat screw ST4X20
2
4
snap-ring φ40
1
49
cross-flat screw ST4X25
2
5
plastic disc
1
50
left handle
1
6
spring
Φ2XΦ45XΦ49X40X4
1
51
cable cover
7
circlip-internal φ32
1
52
cable (plug)
8
ball-bearing 6002 2RS
1
53
handle's screw
1
9
connecting spindle
1
54
aluminum pipe
1
10
pivot hub
1
55
left Clamping block
1
11
hex screw M6X20
2
56
right Clamping block
1
12
support arm
1
57
LC
1set
13
O-ring 2.75X15
1
58
variable speed control
1
14A
drive shaft cover
1
59
right handle
1
14B
drive shaft
1
60
switch
1
15
dust shroud
1
61
cable
1
16
cross-flat screw M4x12
2
62
cable clip
1
17
flexible pad φ4
2
63
cross-flat screw ST4X12
2
18
hex screw M6X20
2
64
hose clamp φ25-38
1
19
string board
1
65
soft pipe
1
20
sharp-cross screw ST4X45
4
66
left fork arm
1
21
gear box
1
67
right fork arm
1
22
spindle
1
68
hex screw M5X12
4
23
ball-bearing 6001 2RS
1
69
cross-flat screw ST4X18
2
24
circlip-internal φ12
1
70
cross-flat screw ST4X20
3
25
circlip-external φ28
1
71
big aluminum pipe( front)
1
26
big gear M1X32T
1
72
cross-flat screw ST4X20
11
27
ball bearing 698ZZ
1
73
cross-flat screw ST4X18
2
28A
needle bearing
HK0810(φ8Xφ12X10)
1
74
cross-flat screw ST4X14
3
28B
flat washer Φ8X1
1
75
circlip-internal φ10
1
29
intermediate spindle
M1X11T
1
76
grease holder
2
30
parallel key 4X4X6
2
77
cross-flat screw
6
31
input gear M0.8X35T
1
78
nylon brush/skirt
1
32
ball bearing 608ZZ
1
accessories
33
gear plate
1
1
soft pipe
1
34
ball bearing 6000 2RS
1
2
adaptor
2
个
Summary of Contents for FPG710-SH
Page 14: ...14 3 4 7 Delivered with harness 3 4 8 Correct method of use ...
Page 20: ...20 ...