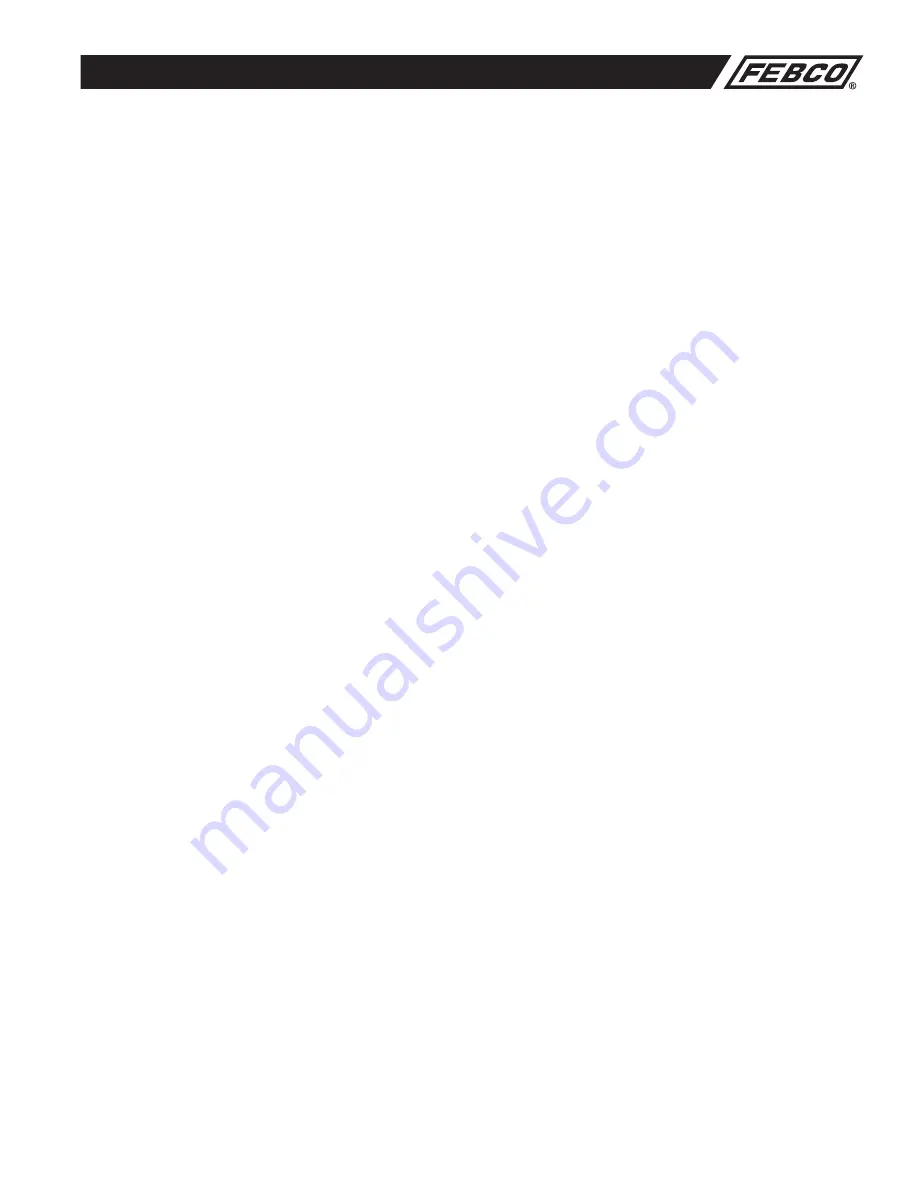
5
1 . FEBCO backflow prevention assemblies can be serviced with standard
tools and are designed for ease of maintenance . The assemblies are
designed to be serviced in line, so the unit should not need to be
removed from the line during servicing . NO special tools are required .
2 . The most common cause of check fouling is dirt and debris in the
seating areas . The line should be flushed clean of debris before instal-
lation of the assembly . To flush the line after installation of the assem-
bly, slowly close the inlet shutoff valve, remove the covers and spring
assemblies of both check valves and open the inlet shutoff valve to
allow sufficient flow of water through the assembly to clear all sand,
debris, etc . from the line . If debris in the water continues to cause
fouling, a strainer may be installed upstream of the assembly (check
local codes) .
3 . Rinse all parts with clean water before reassembly .
4 . Lubricant is recommended only for #2 check cover O-ring to help hold
O-ring in place during reassembly (Series 870V and 876V) . Apply a thin
coating of the lubricant supplied in the repair kit to the O-ring groove in
the #2 check body, and position the O-ring in the groove .
5 . Carefully inspect seals and seating surfaces for damage or debris . If
the check valve seat disc has been severely cut at the seat ring diam-
eter, the assembly has been subjected to extremely high and repeated
back pressure . Either thermal water expansion or water hammer are
the most likely causes . If back pressure persists, consider installation
of a pressure relief valve downstream of the assembly .
6 . Use caution to avoid damaging any guiding surfaces while handling
parts . Do not force parts together . The O-ring seals used in FEBCO
assemblies require only a small tightening force to insure a
positive seal .
7 . Test unit after servicing in accordance with locally approved test
methods to insure proper operation (See Page 5 for more details) .
8 . Refer to applicable parts lists and cut-a-ways (Pages 11-13)
for visual aid information .
MAINTENANCE MANUAL SERIES 850, 856, 870V & 876V 2
1
⁄
2
"- 10" (65 – 250mm)
General Service Procedures
1
⁄
2
" - 10" (15-250mm)