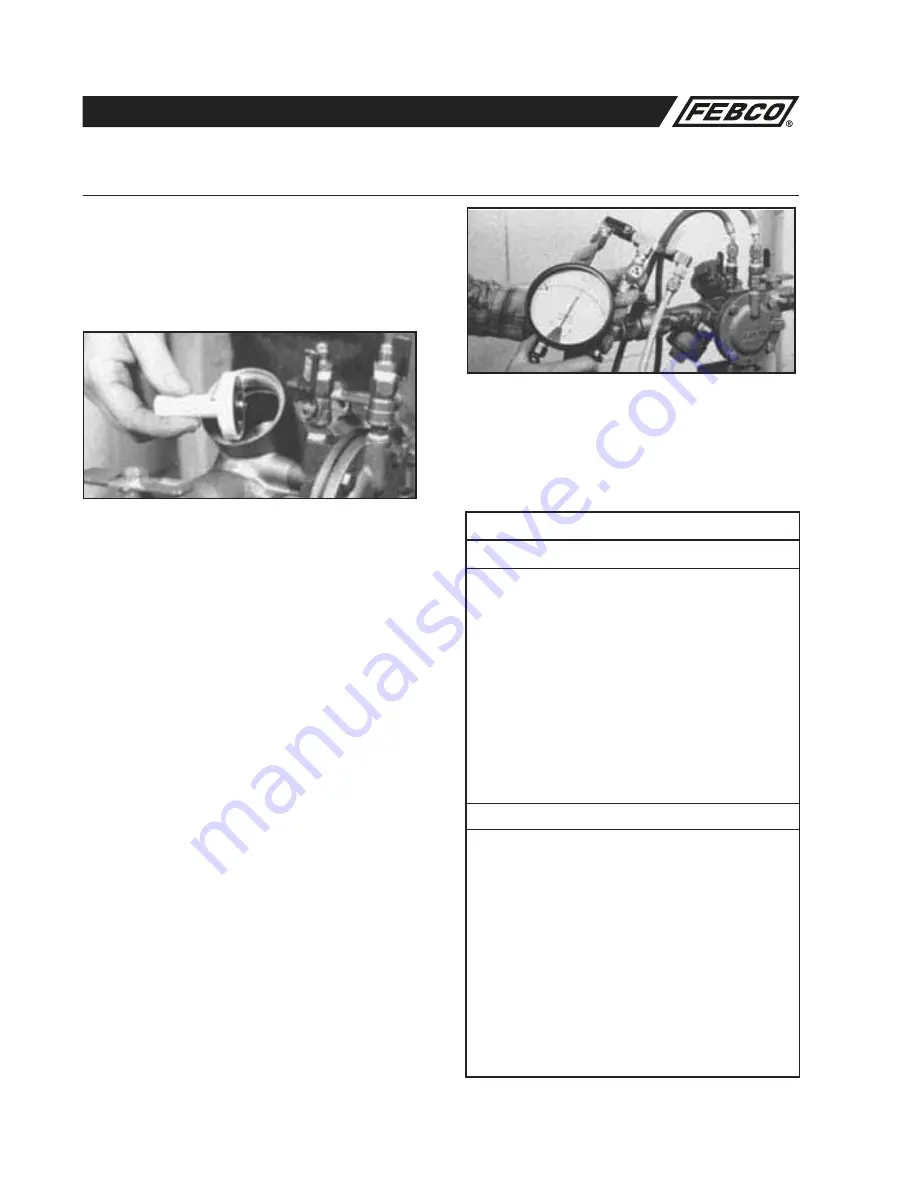
6
MAINTENANCE MANUAL MODELS 825Y, 825YA, 825, 825D, 825YD & 826YD
1. FEBCO backflow prevention assemblies can be serviced with
commonly available tools and are designed for ease of mainte-
nance. The assemblies are designed to be serviced in line, so
the unit should not need to be removed from the line during
servicing.
2. The most common cause of check fouling and relief valve dis-
charge is dirt and debris in the seating areas. The line should
be flushed clean of debris before installation of the assembly.
To flush the line after installation of the assembly, slowly close
the inlet shutoff valve, remove the covers and internal assem-
blies of both check valves and open the inlet shutoff valve to
allow sufficient flow of water through the assembly to clear all
sand, debris, etc. from the line. If debris in the water continues
to cause fouling, a strainer may be installed upstream of the
assembly.
3. Rinse all parts with clean water before reassembly.
4. Do not use any petroleum based oil, grease, solvent or pipe
dope on any parts unless instructed to do so. Use only water
resistant lubricants that comply with FDA requirements for use
in potable water systems.
5. Carefully inspect diaphragms, seals and seating surfaces
for damage or debris. If the check valve seat disc has been
severely cut at the seat ring diameter, the assembly has been
subjected to extremely high and repeated back pressure.
Either thermal water expansion or water hammer are the most
likely causes. If back pressure persists, consider installation of
a pressure relief valve downstream of the assembly.
6. Use caution to avoid damaging any guiding surfaces while han-
dling parts. Do not force parts together. The o-ring seals used
in FEBCO assemblies require only a small tightening force to
ensure a positive seal.
7. Test unit after servicing to ensure proper operation.
General Service Procedures
General Service Instructions applicable to all models and sizes.
8. Refer to applicable parts list and figures for visual aid informa-
tion
Suggested Tool Kits
Model 825Y (
3
/
4
–2")
• 1 Crescent wrench ( 10")
• 1 Medium Phillips screwdriver
• 1 Medium straight blade screw driver
• Allen head wrench (3/16" & 1/4" size)
• 1 Thin blade knife or reamer
• 1 Socket (1/2" and 9/16" size)
• Differential pressure test kit
• FDA approved lubricant
• Needle nose pliers
Model 825, 825D and 825YD (2
1
/
2
–10")
• 1 Crescent wrench (12")
• 1 Medium Phillips screw driver
• 1 Medium straight blade screw driver
• 1 Set of drive sockets (3/8" or 1/2")
• 1 Spring removal tool (see page 33)
• 1 Torque wrench
• Differential pressure test kit
• FDA approved lubricant
Figure No. 6