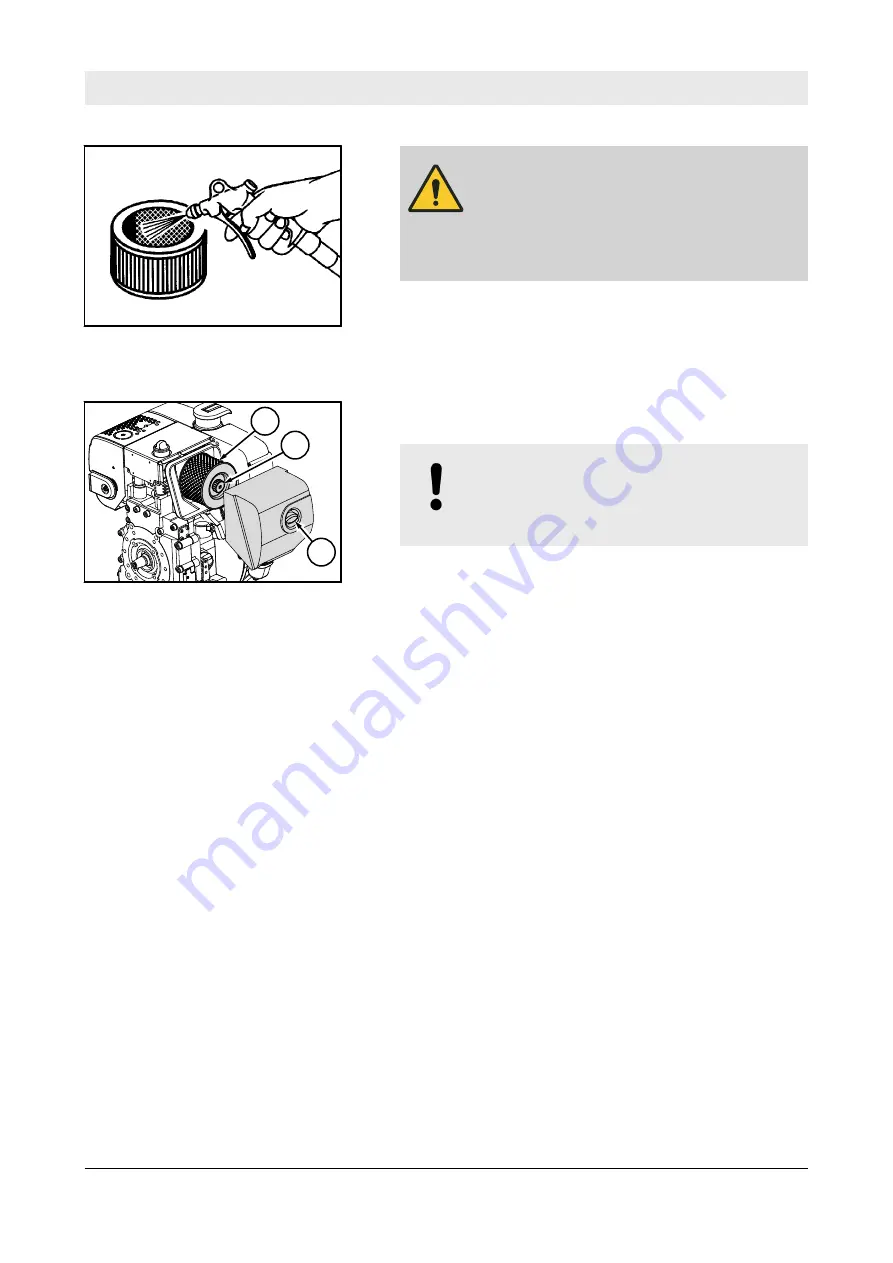
7.
CAUTION!
Danger of eye injuries caused by particles
flying around!
–
Wear your personal protective equipment
(safety gloves, protective working
clothes, goggles).
Blow the air filter out with dry compressed air (max. 5 bar
(73 psi)) from inside to outside by moving the gun up and
down inside the element, until it is free of dust.
8.
Examine the air filter with a torch for cracks and holes.
9.
Replace the air filter if it is damaged.
10.
Insert the air filter (1) carefully into the filter housing and
fasten it with the knurled nut (2).
11.
NOTICE!
Danger of engine damage!
–
Ensure correct fit of air filter cover and
seal.
Close the cap (3).
B-GEN-0042
Fig. 66
B-HAT-0006
1
2
3
Fig. 67
Maintenance – Weekly
DRP45DX
76
Summary of Contents for DYNAPAX DRP45DX
Page 6: ...Table of contents DRP45DX 6...
Page 7: ...1 Introduction Introduction DRP45DX 7...
Page 11: ...2 Technical data Technical data DRP45DX 11...
Page 15: ...3 Concerning your safety Concerning your safety DRP45DX 15...
Page 41: ...4 Indicators and control elements Indicators and control elements DRP45DX 41...
Page 47: ...5 Checks prior to start up Checks prior to start up DRP45DX 47...
Page 53: ...6 Operation Operation DRP45DX 53...
Page 61: ...7 Loading transporting the machine Loading transporting the machine DRP45DX 61...
Page 64: ...Loading transporting the machine Lashing the machine to the transport vehicle DRP45DX 64...
Page 65: ...8 Maintenance Maintenance DRP45DX 65...
Page 102: ...Maintenance As required DRP45DX 102...
Page 103: ...9 Troubleshooting Troubleshooting DRP45DX 103...
Page 114: ...Troubleshooting DCI faults DRP45DX 114...
Page 115: ...10 Disposal Disposal DRP45DX 115...
Page 117: ......
Page 118: ......