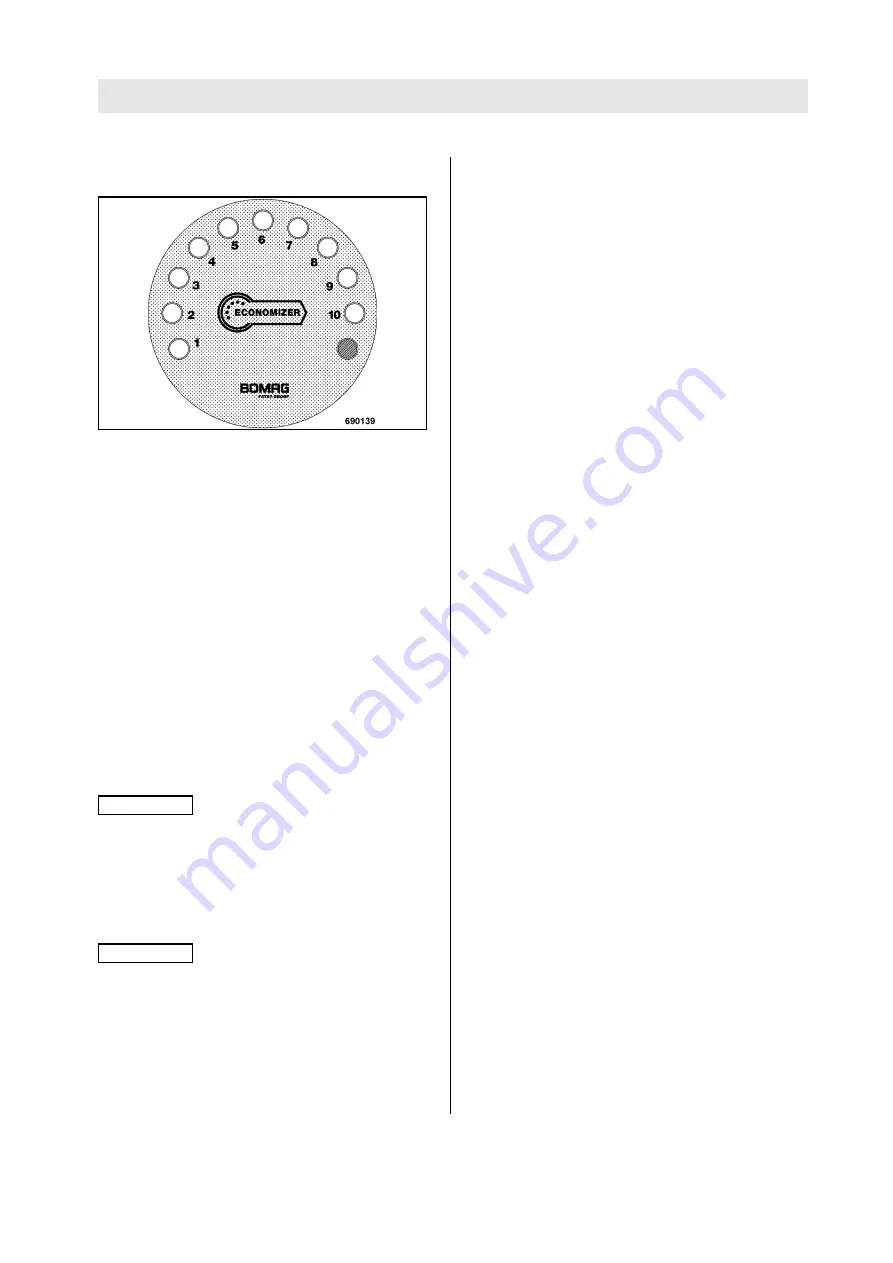
Indicators and Controls
BOMAG
21
BPR 70/70 D
Evaluation and display module
Fig. 15
The yellow LEDs represent the measuring value
from the compaction control in 10 stages.
The brightness of the respective last LED varies in
order to show intermediate values (example: 4,5:
four LEDs are fully on, the fifth LED lights with re-
duced brightness).
The red LED informs about the system status.
Acceleration sensor
The sensor consists of a sensor element, which is
enclosed in a sensor housing, and a connecting
cable with plug-in connector. Actual sensor, hous-
ing, cable and plug-in connector come as a unit,
which cannot be repaired on its own.
The unit is mounted to the base plate of the ma-
chine.
i
Note
The Economizer is maintenance free.
Do not clean the front screen with hard objects!
The material may be destroyed. Possibly disturb-
ing scratches can be removed by polishing, e.g.
with lacquer polish.
i
Note
Vibrating plates of the same type show identical
measuring values when used on the same soil.
The measuring values achieved with different vi-
bratory plates with Economizer from BOMAG can
be made comparable by calibration to a reference
value.
Go to
Discount-Equipment.com
to
order your parts