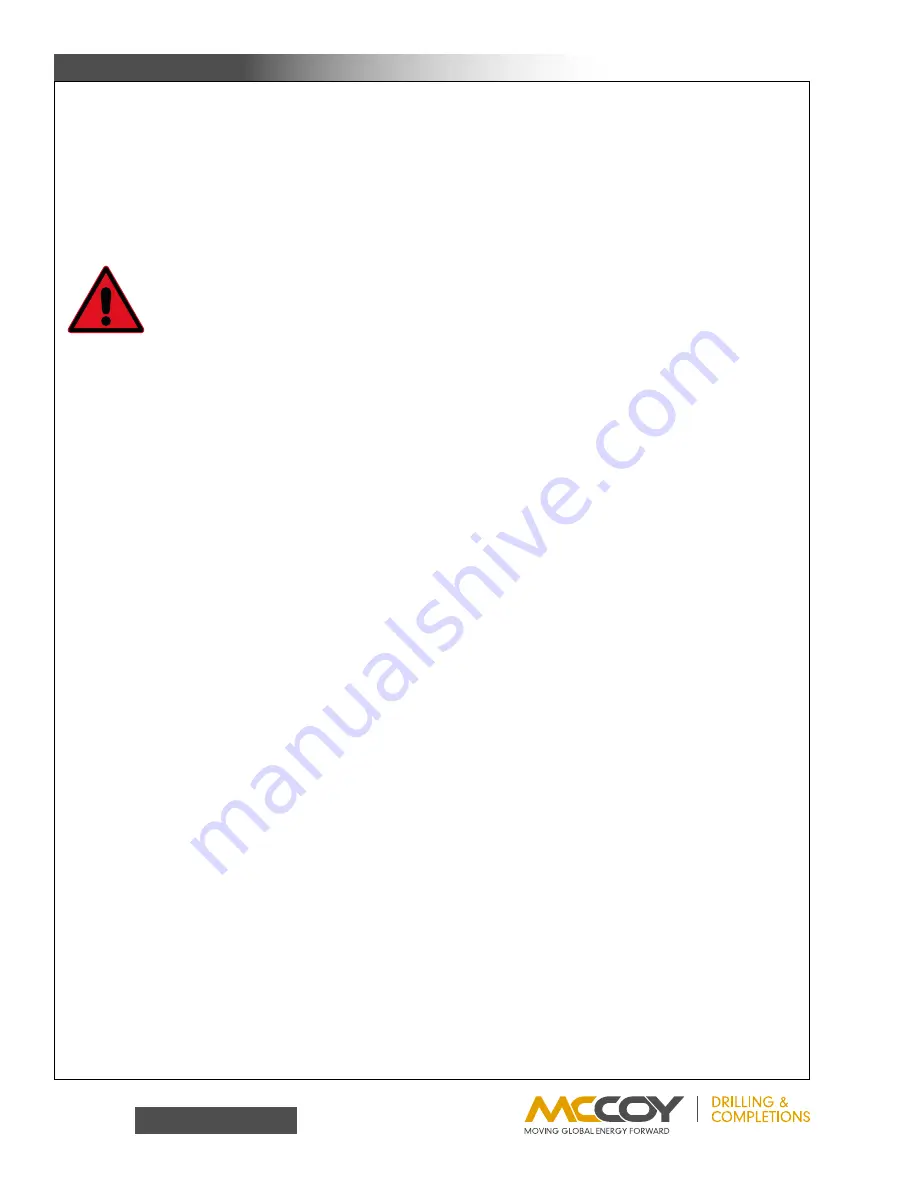
KT5500 5-
1
/
2
” T
ong
& CLInCHER® B
aCKup
S
ECTIon
C
onTEnTS
2.24
T
ECHnICaL
M
anuaL
4.
GENERAL COMMENTS
a) Position rotary gear in contact with both idler gears when breaking out joints or collars where high torques are required.
b) When making-up integral (shouldered) joints, it is essential to make up the last turn of the threads in low gear. This reduces
the tendency of an instant stop or a sudden increase in torque, which induces extremely high stresses on the gear train.
c) DO NOT employ the “snap break” method of breaking-out joints when pulling a string. By definition, the “snap break”
method is a procedure used by some operators to break out connections, accomplished by leaving slack in the “jaw-pipe”
engagement, and then quickly pulling the throttle valve control lever allowing the tong to snap into its loaded or high torque
condition. Although this method is very effective in breaking out joints, the extremely high stress placed on the gear train
frequently causes gear breakage.
G. EXTREME COLD WEATHER OPERATION PROCEDURES
1) Consult the power unit engine operator’s manual for all cold weather operating procedures and precautions.
2) Select gear and bearing lubricants that are compatible with expected climatic conditions.
3) Select hydraulic fluid that is compatible with expected climatic conditions.
4) Allow hydraulic fluid to circulate for approximately 20 minutes after starting the power unit, prior to activating the bypass valve
to allow fluid to circulate to tong. If the power unit is equipped with an oil temperature gauge, ensure that the fluid has reached
operating temperature as specified by hydraulic fluid data sheet.
5) Allow for adequate drying of moisture (prior to lubricating) when cleaning tong parts in cold weather.
S
ETup
& o
pERaTIon
THE “SNAP-BREAK’ METHOD IS HAZARDOUS TO PERSONNEL AND EQUIPMENT
Summary of Contents for 80-0420-16
Page 2: ......
Page 4: ...This page intentionally left blank ...
Page 6: ...This page intentionally left blank ...
Page 10: ...This page intentionally left blank ...
Page 34: ...This page intentionally left blank ...
Page 120: ...This page intentionally left blank ...
Page 128: ...This page intentionally left blank ...