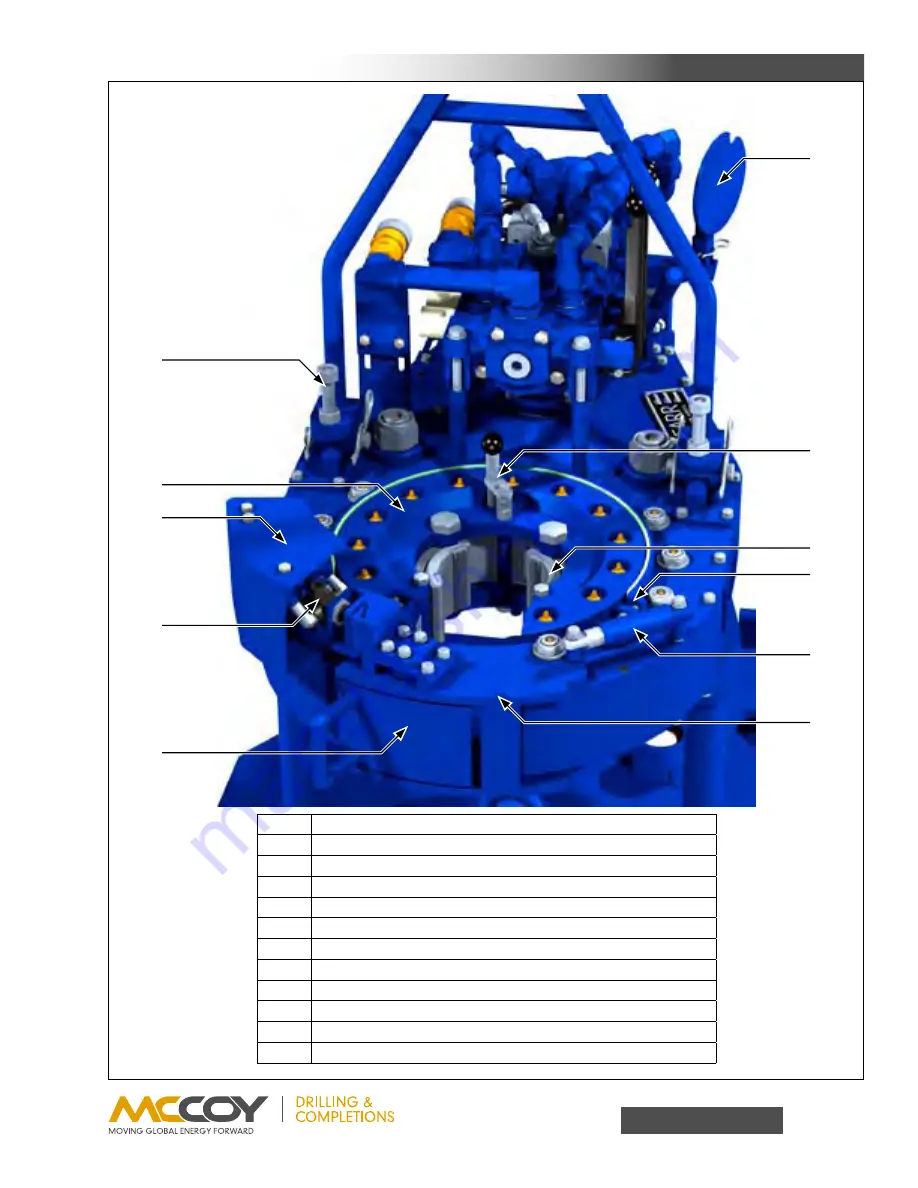
KT5500 5-
1
/
2
” T
ong
& CLInCHER® B
aCKup
S
ECTIon
C
onTEnTS
2.5
T
ECHnICaL
M
anuaL
S
ETup
& o
pERaTIon
Item
Description
7
Rigid Sling Leveling Device
8
Cage Plate Assembly
9
Safety Door Switch Guard
10
Safety Door Switch
11
Tong Door Latch
12
Torque Gauge Mounting Plate
13
Backing Pin Assembly
14
Tong Jaws with Die Inserts
15
Brake Band Adjustment
16
Tong Door Cylinder
17
Tong Door Weldment
7
8
9
12
13
10
11
14
15
16
17
Summary of Contents for 80-0420-16
Page 2: ......
Page 4: ...This page intentionally left blank ...
Page 6: ...This page intentionally left blank ...
Page 10: ...This page intentionally left blank ...
Page 34: ...This page intentionally left blank ...
Page 120: ...This page intentionally left blank ...
Page 128: ...This page intentionally left blank ...