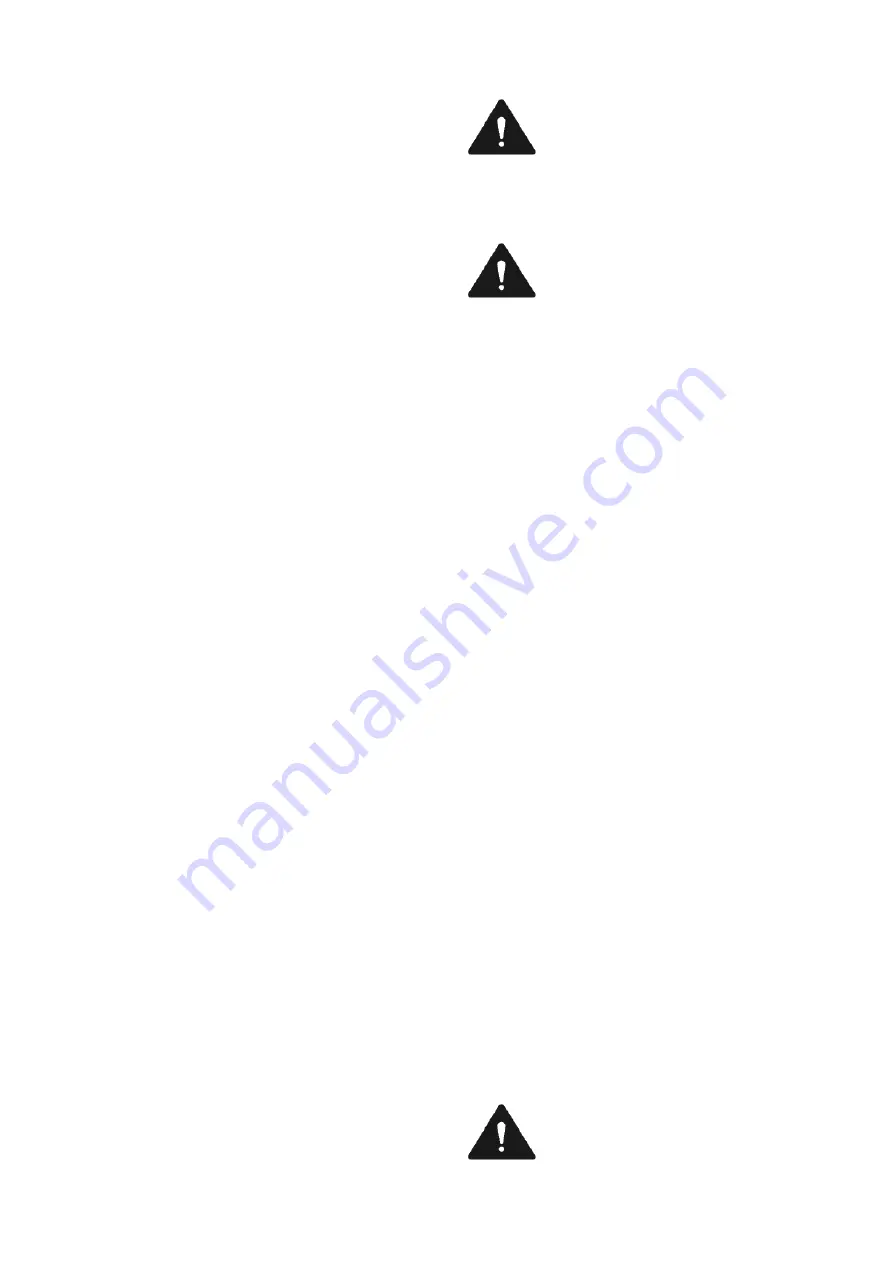
9
CR47
TRANSPORT
1.
Before driving with the machine, ensure the safe
mounting of the machine. Make sure that the jour-
nals are seating correctly and that the pins are tight.
Check the tension of the lower link stabilizers.
2.
Before driving with the machine, make sure that
the required lamps and reflectors as well as the slow
moving vehicle sign are attached correctly. Moreover,
the lamps should be checked for correct functioning.
3.
Before driving with the attached machine, make sure that
the hydraulic unit of the machine is depressurized
(unless otherwise instructed in the operating instruc
-
tions).
4.
When driving on public roads, always observe the valid
traffic regulations. The travel speed must be adapted
to the specific conditions.
5. When driving, please take into consideration the
additional mass resulting from the machine’s weight.
It may affect the reactions, the steerability and the
braking function of the tractor.
6.
Please note that the machine rear sways when
turning.
7.
Pay attention to the machine’s height near bridges or ot
-
her height restricting objects.
8.
When backing off, the machine may obstruct the rear
view. Exercise extreme caution. If necessary, ask
a flagman to help you; he can indicate the required
distances.
9. It is prohibited for other people to ride on the
machine.
OPERATION
Many occupational accidents take
place in abnormal circumstances.
Therefore it is important to take into
account all the possible circumstan-
ces that may arise during operation
of the machine.
The machine’s operator must have
constant, unobstructed visibility of
the work area. If this is not possible,
the operator must work with an as-
sistant.
1.
Depending on the machine’s type, it will have
diverse safety devices and protectors. These are
meant to protect the machine and its operator, and
they must never be removed or altered. Never start
up or use the machine without all the safety devices
and protectors in place.
2.
Also check the universal joint’s safety equipment
and joints.
3.
Never insert any body part into the machine with the
engine running.
4. If any faults arise that may jeopardize occupational safety,
turn off the machine.
5.
During operation, the machine’s operator is
responsible for safety in the whole work area. Work
may not be carried out in the presence of any factors
that jeopardize occupational safety.
6.
Exercise extreme caution when hitching/unhitching the
machine from a tractor/trailer.
7.
Look out for moving parts when the machine is in
operation.
8. Secure the machine against unauthorized and acciden-
tal operation (e.g. moving when parked) whenever
it is left unattended.
9. Never leave the machine running unattended.
10. Avoid causing fast, stroke-like loading.
11. Never exceed the given operating values.
12.
All safety and warning signs on and in the machine must
be legible and intact.
13.
The machine may not be operated by persons who are
unwell or under the influence of drugs or alcohol.
WARNING
ATTENTION
The noise level from the engine
should not exceed 70 dB. Check the
engine noise and wear ear protection
if it exceeds 70 dB.
ATTENTION
Summary of Contents for CR47
Page 2: ...2 CR47 ...
Page 29: ...29 CR47 A H F E D G H C I C B B 6 C B B LUBRICATION POINTS ...
Page 36: ...36 CR47 17 8 6 7 5 19 4 16 21 18 15 3 9 2 14 1 12 10 11 13 20 CR47 SLEWING AND COLUMN ...
Page 40: ...40 ...
Page 42: ...42 CR47 1 10 8 7 6 5 4 3 2 11 16 15 14 13 12 14 13 13 15 9 200002614 ROTATOR CR404S W25A30 ...
Page 46: ...46 ...
Page 52: ...Farmi Forest Ahmolantie 6 74510 IISALMI FINLAND 358 0 17 832 4400 info farmiforest fi ...