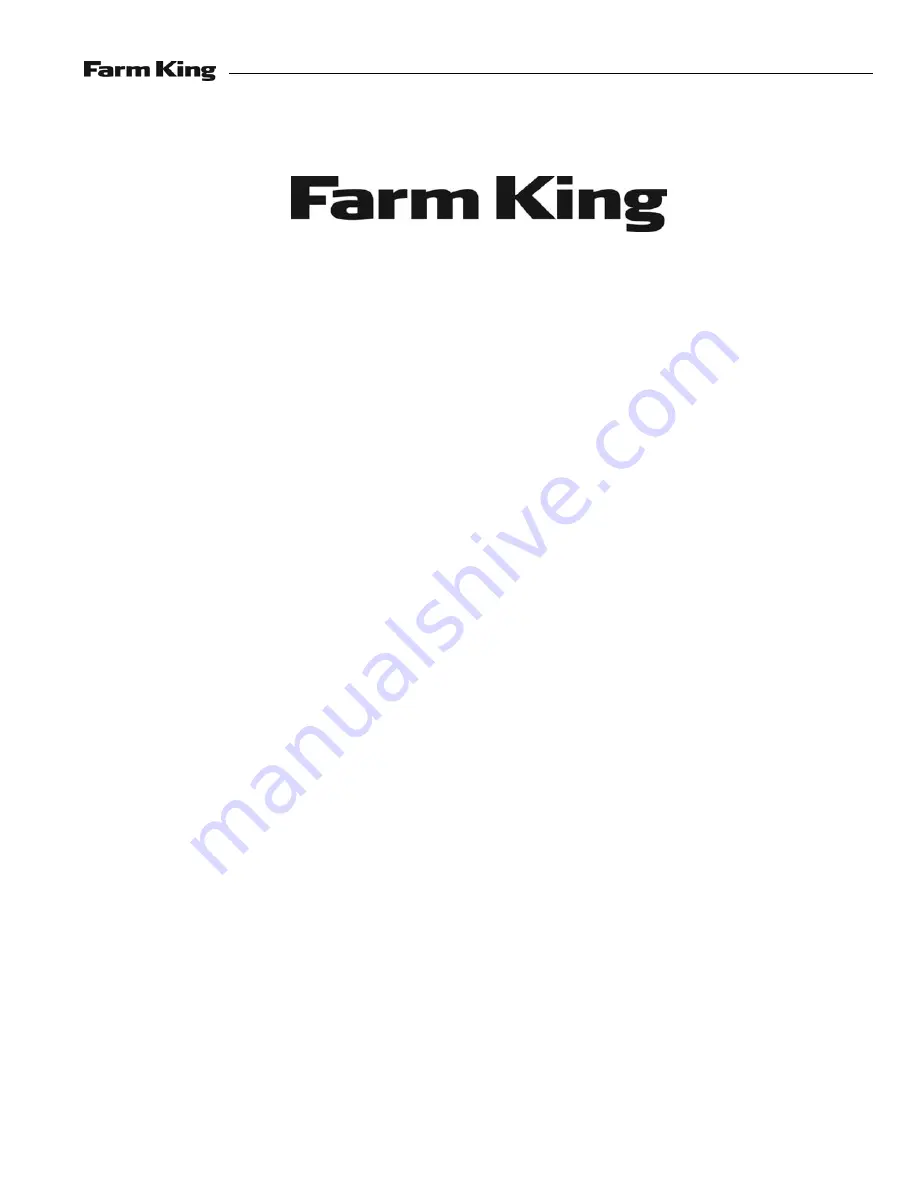
Warranty - 13" Backsaver Auger
263
WARRANTY
Limited Warranty
BASE LIMITED WARRANTY
Farm King provides this warranty only to original retail purchasers of its products. Farm King warrants to such
purchasers that all Farm King manufactured parts and components used and serviced as provided for in the
Operator’s Manual shall be free from defects in materials and workmanship for a period following delivery to the
original retail purchaser of two (2) years. This limited warranty applies only to those parts and components
manufactured by Farm King. Parts and components manufactured by others are subject to their manufacturer’s
warranties, if any.
Farm King will fulfill this limited warranty by, at its option, repairing or replacing any covered part that is
defective or is the result of improper workmanship, provided that the part is returned to Farm King within thirty
(30) days of the date that such defect or improper workmanship is, or should have been, discovered. Parts must
be returned through the selling representative and the buyer must prepay transportation charges.
Farm King will not be responsible for repairs or replacements that are necessitated, in whole or part, by the use
of parts not manufactured by or obtained from Farm King. Under no circumstances are component parts
warranted against normal wear and tear. There is no warranty on product pump seals, product pump bearings,
rubber product hoses, pressure gauges, or other components that require replacement as part of normal
maintenance.
REPAIR PARTS LIMITED WARRANTY
Farm King warrants genuine Farm King replacement parts purchased after the expiration of the Farm King Limited
Warranty, and used and serviced as provided for in the Operator’s Manual, to be free from defects in materials or
workmanship for a period of thirty (30) days from the invoice date for the parts. Farm King will fulfill this limited
warranty by, at its option, repairing or replacing any covered part that is defective or is the result of improper
workmanship, provided that the part is returned to Farm King within thirty (30) days of the date that such defect
or improper workmanship is, or should have been, discovered. Such parts must be shipped to the Farm King
factory at the purchaser’s expense.
WHAT IS NOT COVERED
Under no circumstances does this limited warranty cover any components or parts that have been subject to the
following: negligence; alteration or modification not approved by Farm King; misuse; improper storage; lack of
reasonable and proper maintenance, service, or repair; normal wear; damage from failure to follow operating
instructions; accident; and/or repairs that have been made with parts other than those manufactured, supplied,
and or authorized by Farm King.
AUTHORIZED DEALER AND LABOR COSTS
Repairs eligible for labor under this limited warranty must be made by Farm King or an authorized Farm King
dealer. Farm King retains the exclusive discretion to determine whether it will pay labor costs for warranty
repairs or replacements, and the amount of such costs that it will pay and the time in which the repairs will be
made. If Farm King determines that it will pay labor costs for warranty work, it will do so by issuing a credit to
the dealer’s or distributor’s account. Farm King will not approve or pay invoices sent for repairs that Farm King
has not previously approved. Warranty service does not extend the original term of this limited warranty.
Summary of Contents for 13114
Page 2: ......
Page 4: ...Table of Contents 13 Backsaver Auger 4 ...
Page 6: ...Warranty Registration 13 Backsaver Auger 6 ...
Page 8: ...Introduction 13 Backsaver Auger 8 ...
Page 12: ...Safety 13 Backsaver Auger 12 ...
Page 26: ...Assembly 13 Backsaver Auger 26 ...
Page 116: ...Assembly 13 Backsaver Auger 116 ...
Page 118: ...Operation 13 Backsaver Auger 118 ...
Page 142: ...Maintenance 13 Backsaver Auger 142 ...
Page 154: ...Maintenance 13 Backsaver Auger 154 ...
Page 158: ...Parts Identification 13 Backsaver Auger 158 ...
Page 164: ...Maintenance 13 Backsaver Auger 164 STUB AXLE ASSEMBLY BS1370 906572 2 4 5 3 4 4 6 1 ...
Page 170: ...Maintenance 13 Backsaver Auger 170 STUB AXLE ASSEMBLY BS1385 BS1395 906573 3 4 5 6 1 4 2 ...
Page 176: ...Maintenance 13 Backsaver Auger 176 STUB AXLE ASSEMBLY BS13114 909191 2 4 5 3 4 4 6 1 ...
Page 242: ...Maintenance 13 Backsaver Auger 242 ...
Page 244: ...Shipping Kit and Bundle Numbers 13 Backsaver Auger 244 ...
Page 250: ...Shipping Kit and Bundle Numbers 13 Backsaver Auger 250 ...
Page 252: ...Specifications 13 Backsaver Auger 252 ...
Page 260: ...Specifications 13 Backsaver Auger 260 ...
Page 261: ...Warranty 13 Backsaver Auger 261 WARRANTY WARRANTY 263 ...
Page 262: ...Warranty 13 Backsaver Auger 262 ...
Page 267: ......