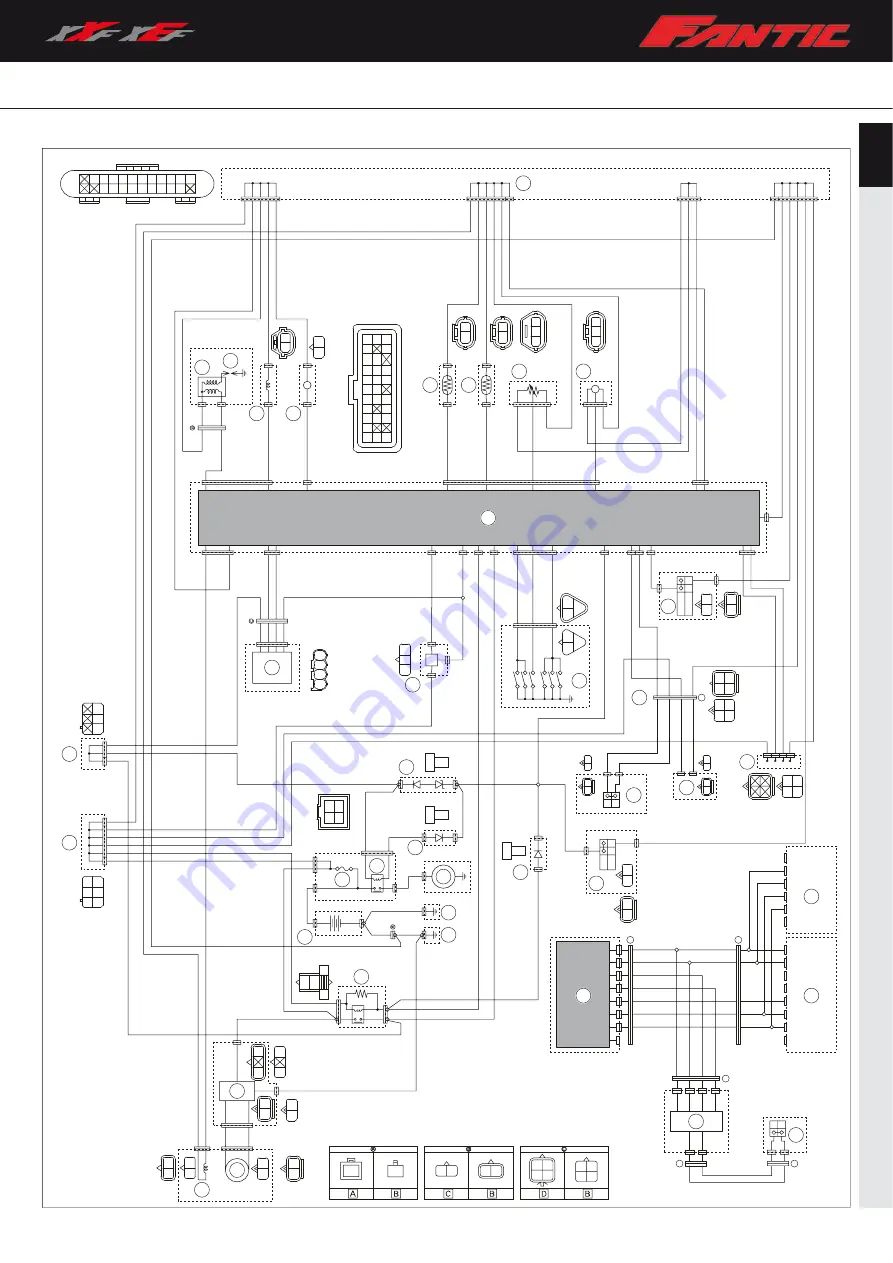
1. General information
USE AND MAINTENANCE MANUAL
CHAPTER 1
GENERAL INFORMATION
4-Strokes - Edition 00 / 2022
57
1
WJ01
WJ02
R R R R R NL NL NL NL NL
N N N N N N L L L
R
R
R
C
C
RN
NG
RN
RN
R
R
RN A G
VH LN GR
B R
VG NC
S
NG NB L
BN GN M
C NR N
NL
NL
MB
NL
VB
L
G
NL
SN
L
NL
MB
NL
VB
L
L
SN
NL
G NL
MB
VB
G
SN
L
NL
H
LR
V
NL
VB MB
SN
NG
NG
R R R R
L L L
N N
N
N
N
N
N
RL
NB
NR
N
NC
NB
LN
GN
A
S
M
LR
BN
V
V
RL
V
BN
BN
BN
RL
BN
BN
BN
B
VG
B
VG
H
M
M
M
M
M
M
MB
M LV LB
MB
RG
RB
R
MB
L
N
N
N
N
R
RB M
LR
RL
RL
RB
R
R
R
N
N
B
B
B
B
B
B
N
H
H
NL
B
B
H
NL
B
B
N
R
M
M
N
N
C R
R C
B VG
BN M
VG B
M BN
LR
LR
N
N
N
L
LV L
RG
RB
MB
L
LV
LV
M
R
RL
RL
RL
RL
RG
R
RG
RL
RL
RL
RG
R
M
B
VG
BN
M
M
GN
A
S
S
GN
A
GN
S
A
LN
LN
LR
LR
LN
LB
LB
LN
LN
N
N
LN
MR
N
CR
CL
NL
MG
S
MR N
CR CL
MR
N
NL
MG
S
N
N
NR
NC
NB
RL
NR
N
BL
N
BN
N
BN
BN
BN
N
N
BR
BL
BL
BL
BR
BR
BR
N
GV
RL
GV
GR N
GR
N N N N
NL
NL NL
NL
NL NL
NL
N
RL
GR
GV
B
BR
BN
BL
17
18
19
20
21
04
22
23
24
16
04
04
01
02
03
05
06
07
08
11
09
10
12
13
30
29
33
34
37
35
36
26
31
32
28
E
F
F
F
G
G
25
27
15
14
Wiring diagram (XXF 450 version)