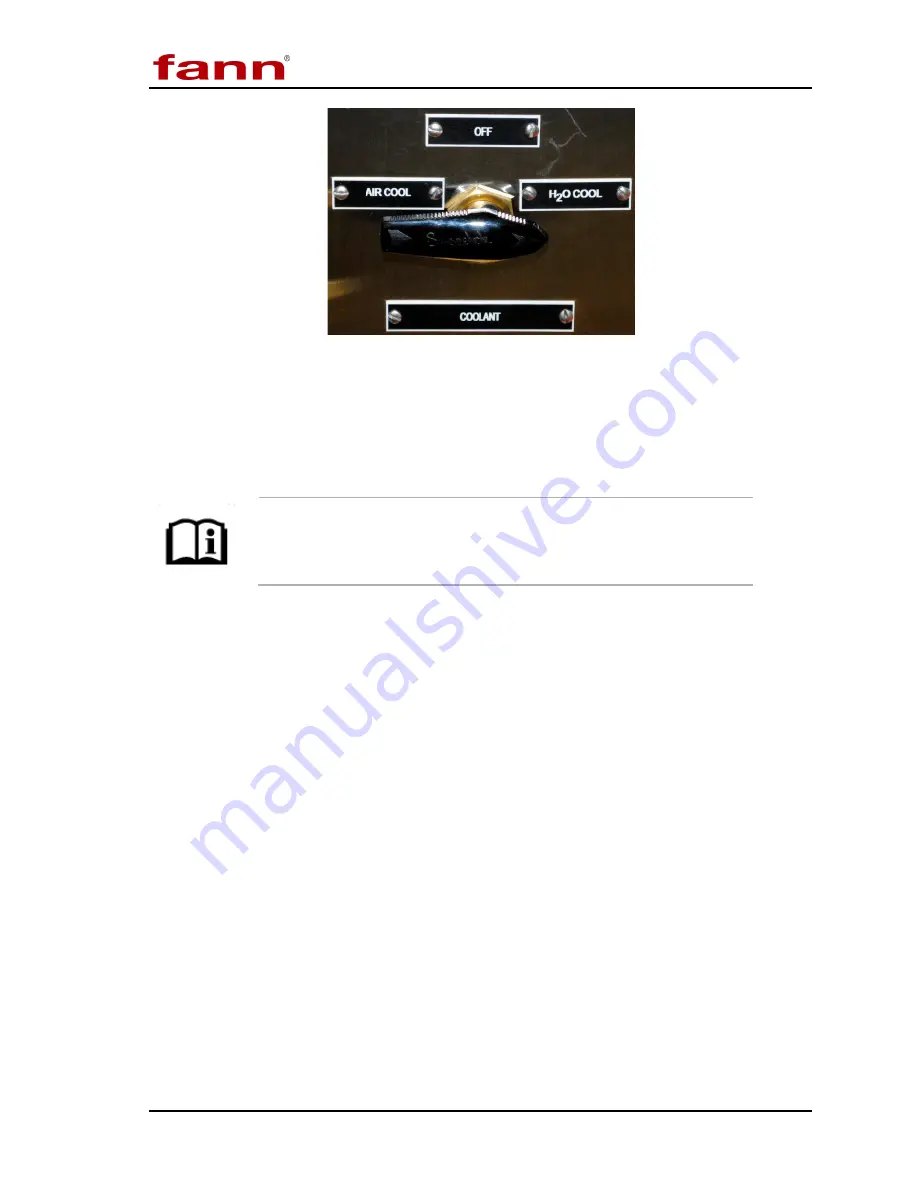
Stirring Fluid Loss Manual
100031980
Revision F
26
Figure 5-6 Coolant Valve open for water flow
10.
After sample reaches BHCT, open valve between sample chamber and filtrate
unit.
11.
Start
Timer
. Begin timing fluid loss volume (mL) when valve is opened.
If slurry samples dehydrate completely (blow out) in less than 30
minutes, you will hear a hissing sound (gas released). Record the
time.
12.
Record the time (30 minutes maximum) and end the test.
13.
If the slurry has not dehydrated after 30 minutes, stop the test.
5.5
End the Stirring Fluid Loss Test
1.
Turn off the heater.
2.
Close valve between sample chamber and filtrate unit.
3.
Reduce nitrogen regulator pressure to approximately 200-300 psi.
4.
Turn off
Coolant
valve. Valve position will be pointing up -
Off
.
Summary of Contents for 210194
Page 39: ...Stirring Fluid Loss Manual 100031980 Revision F 39 Figure 8 1 Stirring Fluid Loss Assembly...
Page 44: ...Stirring Fluid Loss Manual 100031980 Revision F 44 Figure 8 3 Mainframe Assembly Front View...
Page 45: ...Stirring Fluid Loss Manual 100031980 Revision F 45 Figure 8 4 Mainframe Assembly Rear View...
Page 50: ...Stirring Fluid Loss Manual 100031980 Revision F 50 Figure 8 7 Chamber Assembly...
Page 52: ...Stirring Fluid Loss Manual 100031980 Revision F 52 Figure 8 8 Manifold System Water Nitrogen...