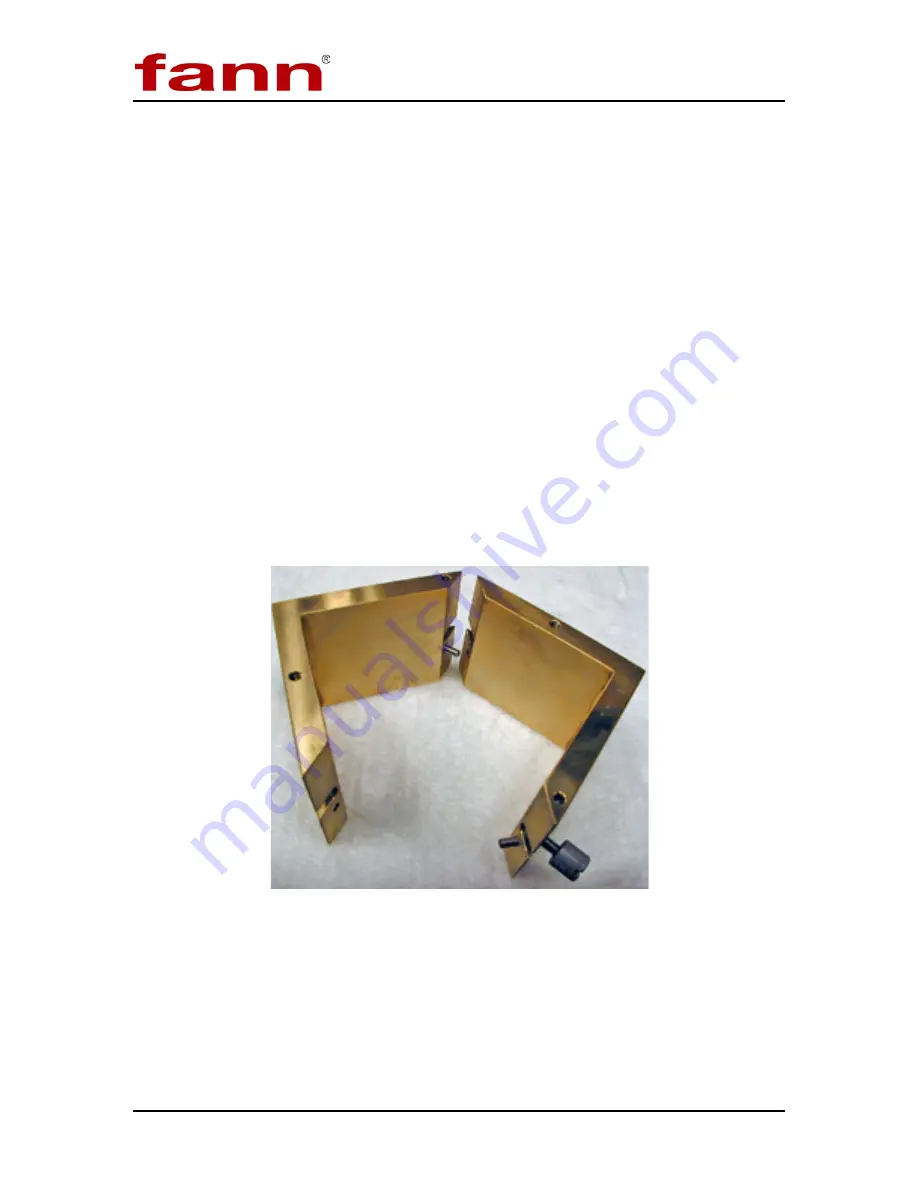
Cement Curing Autoclave User Manual
100072577
Revision H
28
5 Operation
5.1
Sample Preparation
5.1.1
Preparation of the cement slurry, curing, and strength testing of the
cured sample should be done by following the procedures in the latest
edition of the API Recommended Practice for Testing Oil Well Cements
and Cement Additives (API RP 10B). This publication is available from
the American Petroleum Institute, Division of production, 300 Corrigan
Tower Building, Dallas, Texas, 75201, USA. These procedures should be
reviewed prior to using the Cement Curing Autoclave.
5.2
Prepare the Cube Mold
5.2.1
One or two, 2 inch, cube molds are used with the Cement Curing
Autoclave chamber. To prevent the cement slurry from seeping into the
joints between the sides and base plates, apply a thin coat of grease to the
bottom edges of the mold. Keep and use like numbered cement mold
halves together.
Figure 5-1
Pins align the mold halves