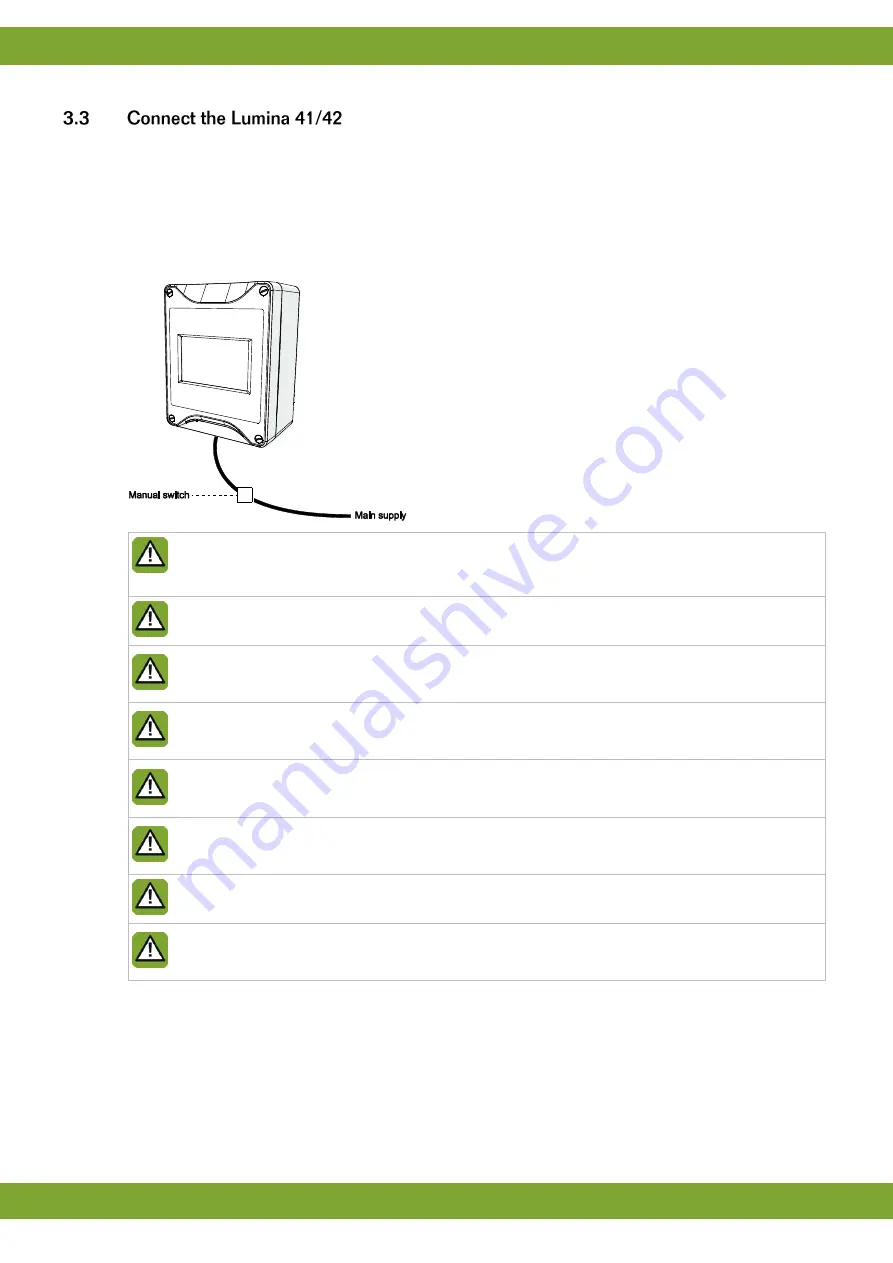
Lumina 41/42
Installing the Lumina 41/42
6
Connect the Lumina 41/42 as follows:
1. Open the cover.
2. Connect the Lumina 41/42 to the manual switch.
3. Connect the manual switch to the main supply (be sure power is disconnected).
4. Connect other (signal wires) to the Lumina 41/42, see chapter Technical specifications.
5. Close the cover.
Always use the cable swivels when connecting the Lumina 41/42. Use the sealing discs supplied to seal
off any unused swivels. Use a sealant to seal all swivels, after the computer has been connected, to
prevent the entry of moisture, dust and/or aggressive gasses.
Check that the mains voltage and frequency, for which this computer is suitable, correspond to the
mains voltage and frequency on site.
Be sure that the Lumina 41/42 is properly grounded. When using metal cable trays, grounding at one
point of the tray is recommended.
The Lumina 41/42 should be possible to shut down with a double pole switch.
Connect the Lumina 41/42 to a group from the main distributor and mount in separate cable trays.
Limit the length of the signal wires much as possible; avoid crossing high/low voltage wires.
To protect against lightning, place an over voltage protection device in the power supply of the Lumina
41/42.
Condensation should never occur in the control computer.
Summary of Contents for F41
Page 1: ...g ...
Page 39: ...Lumina 41 42 Technical specifications 35 ...
Page 41: ...Lumina 41 42 Technical specifications 37 ...
Page 44: ...Lumina 41 42 Appendix Concept feeding systems 40 ...
Page 46: ...Lumina 41 42 Appendix Concept feeding systems 42 ...
Page 47: ...Lumina 41 42 Appendix Concept feeding systems 43 ...
Page 48: ...Lumina 41 42 Appendix Concept feeding systems 44 ...
Page 50: ...Lumina 41 42 Appendix Concept feeding systems 46 ...