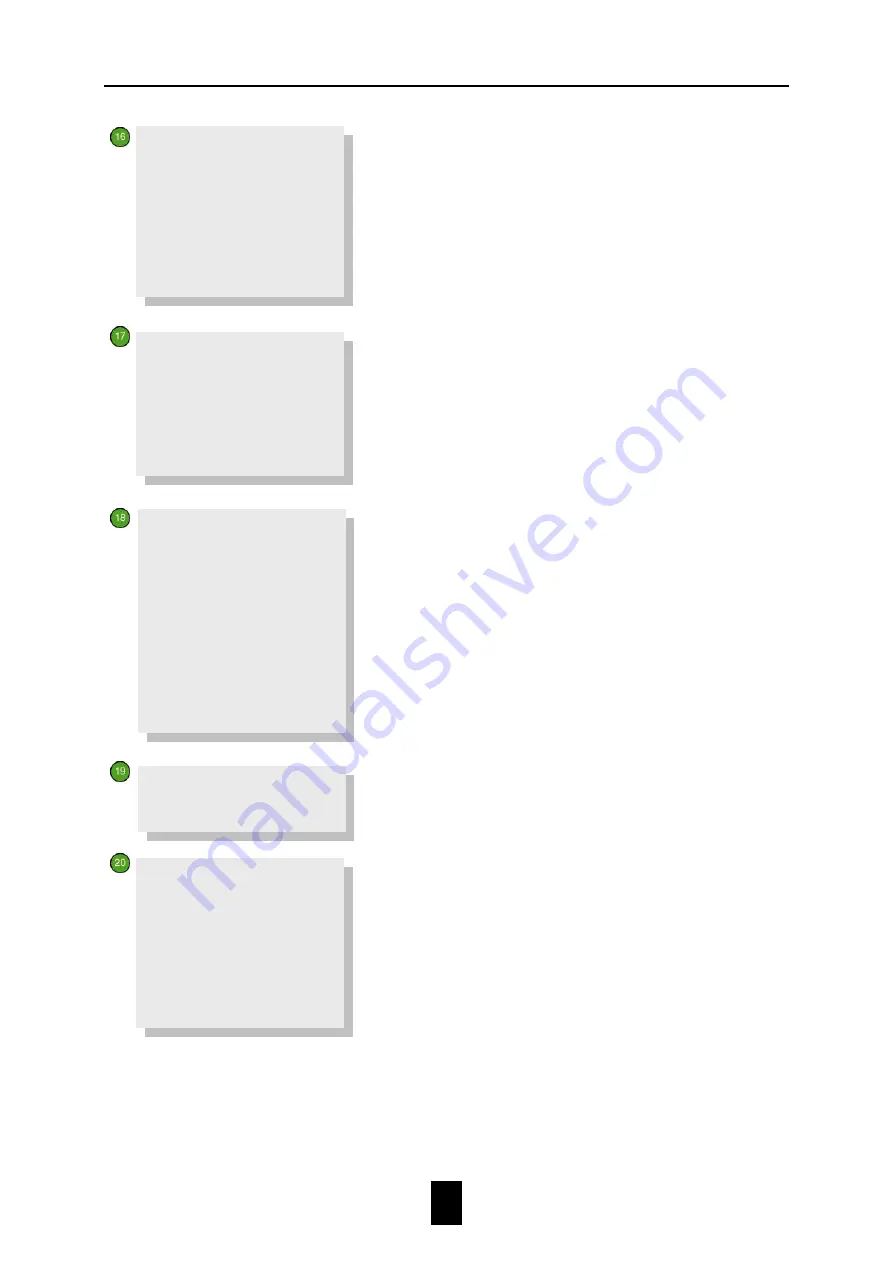
Fancom 743
APPENDIX 1: Menu overview
1-8
* = 1-16
** = 1-24
Day tot..........
*
Water ...... ..,...
Feed ...... ..,...
Water:feed ..,..
Total cons.
*
Wat. ....... ..,...
Feed ....... ..,...
Water:feed ..,..
* = 1-16
>>Program
*
Stor. silo .........
Water clock.........
Prep.feed ..........
Feed days skip-a-day
MTWTFSSMTWTFSS
(..) ..............
Block from ..:..
Block prepar. ...
>>
Copy to all
storage silos?
...
Time ..:..
Date .. ..-..-..
>>Situation overview
Prep. feed ....
A=.. B= .. --------
Weigher cont. ..,...
Ingredient --------
End weight ....
Stor.silo dem. .....
Pphase= ..Tphase= ..
Hopper .........
Mixer .....
* = 1-16
>>Time clock_**
*
Start RunT End
..:.. ..:..:.. ..:..
>>
Status ....
>>
Copy to all
storage silos?
...