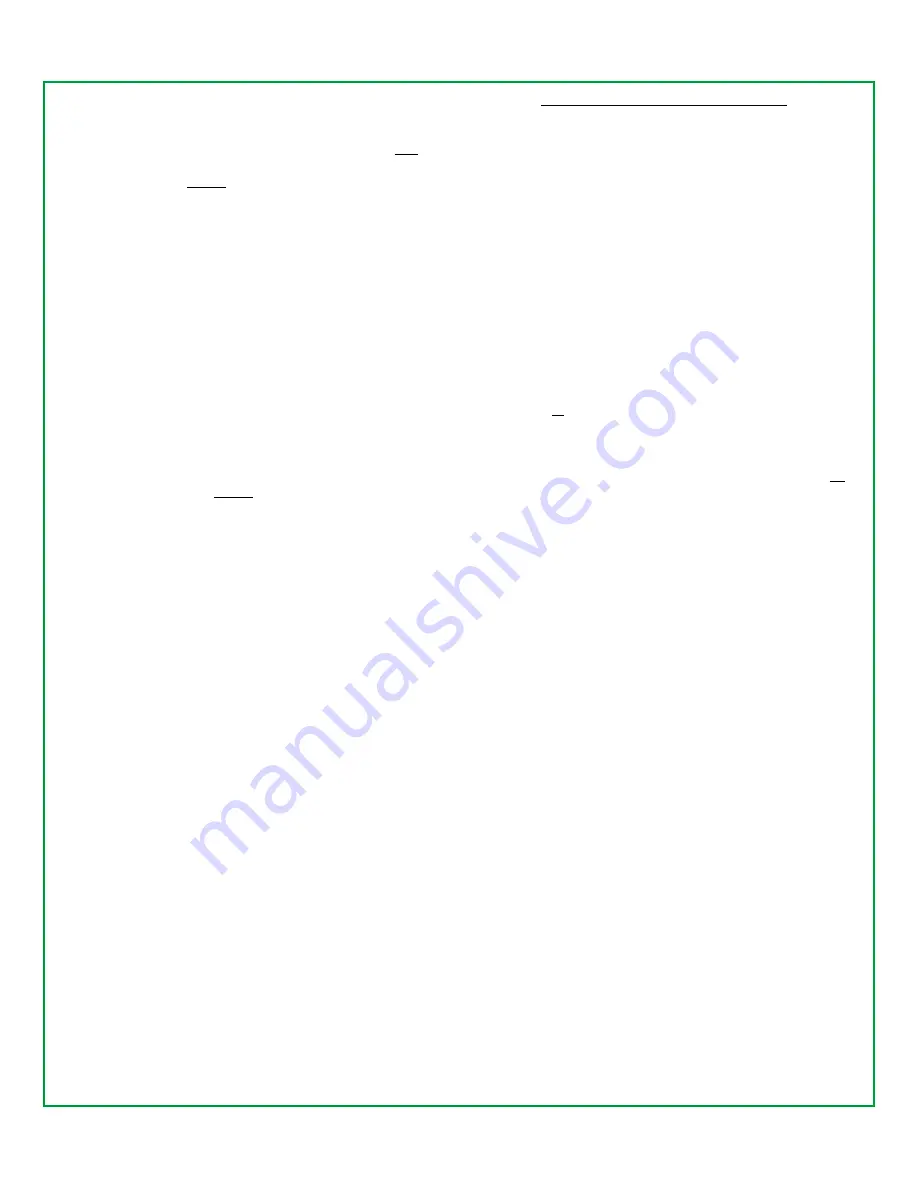
cause unnecessary expense, effort and delay, so be sure to read through all of the potential causes, below,
before taking action.
▪
A: The bottom end of the sensor and the bowl rim must both be clean, not coated with flour or dough. The
sensor must be positioned no more than 1/8” above the rim of the bowl. It also must be positioned directly
above the rim of the bowl (view this from the side, not the front). Adjust as necessary and retighten firmly,
being careful not to strip the fine threads of the sensor barrel.
▪
B: The bowl sensor must be functioning properly internally. Function of the bowl sensor can be tested by
holding (or wrapping) a piece of aluminum foil against the bottom of the sensor and attempting to start the
mixer. Do not use hard metal objects for this testing, as injury or machine damage could occur.
•
If the aluminum foil allows the mixer to run, this means the sensor is good and you can skip to point
10.3.2, below. But if the mixer still does not run, that would not necessarily mean that the sensor is
bad; the cause of non-running may be something else. The following directions, about the sensor light,
are for qualified personnel only, because they require the machine to be powered with the top cover
removed.
(An individual is qualified if they are competent to avoid contact with dangerous moving parts
and electrical components.)
There is a small LED indicator light embedded below the dark plastic top of
the sensor. (When it is not lit, the LED cannot be seen.) With the top panel removed and with tin foil
against the bottom of the sensor, if the sensor light is
lit
, this indicates that the sensor detects the
metal, and, in most cases, also indicates that the sensor is also completing its part of the safety circuit
and is not the cause of the mixer not running.
With the machine connected to power and foil against the bottom of the sensor, if the sensor light i
s
not lit
, then either the sensor or the main control board is defective. Determination of which one is
defective begins with replacement of the bowl sensor, because it is more often at fault and is quicker to
replace. For convenient testing, a new bowl sensor can be wired into its junction block and machine
function tried again without mechanically mounting the new sensor into position above the bowl: Just
wrap foil around the end of the new sensor and if the old sensor was bad, the mixer will run because
the sensor doesn’t “know” where it is—it only knows whether there is metal in its detection zone.
Before normal operation of the mixer, the new sensor must be mounted in its proper position above the
rim of the bowl. If your mixer does not run with a new bowl sensor, the control board may be defective
and require replacement.
▪
C: For more information about troubleshooting the bowl sensor, see video #06 in
the online Famag Use
Video Library.
•
(10.3.2) Bowl Guard Safety Switch
▪
A: The bowl guard must be in the lowered position, covering the bowl, or the mixer will not run.
▪
B: The arm on the microswitch inside the head of the mixer must be adjusted properly so that it is
mechanically actuated (causing that switch to click audibly) when the bowl guard is lowered.
▪
C: The microswitch must be functioning correctly electrically, so that it actually completes its circuit when it
clicks.
▪
D: For important info about the bowl guard safety switch, see video #03
the online Famag Use Video
Library.
•
(10.3.3)
Defective Control Board:
If power is supplied to the mixer and you have determined that neither the bowl
sensor or the bowl guard safety switch is the cause, the main control board may be defective. Individual
components of the control board are not replaceable; the solution would be replacement of the entire control board.
If a new board is installed and the mixer runs, this confirms that the original board was bad.
•
(10.3.4) GFCI Tripping:
Some homes are equipped with GFCI power outlets, and a small percentage of Famag
users experience GFCI tripping.
11
Summary of Contents for IM-10S
Page 1: ...Famag User Manual Professional Spiral Dough Mixers Models IM 5 8 10...
Page 2: ...2...
Page 8: ...8 0 Parts Diagram 8...