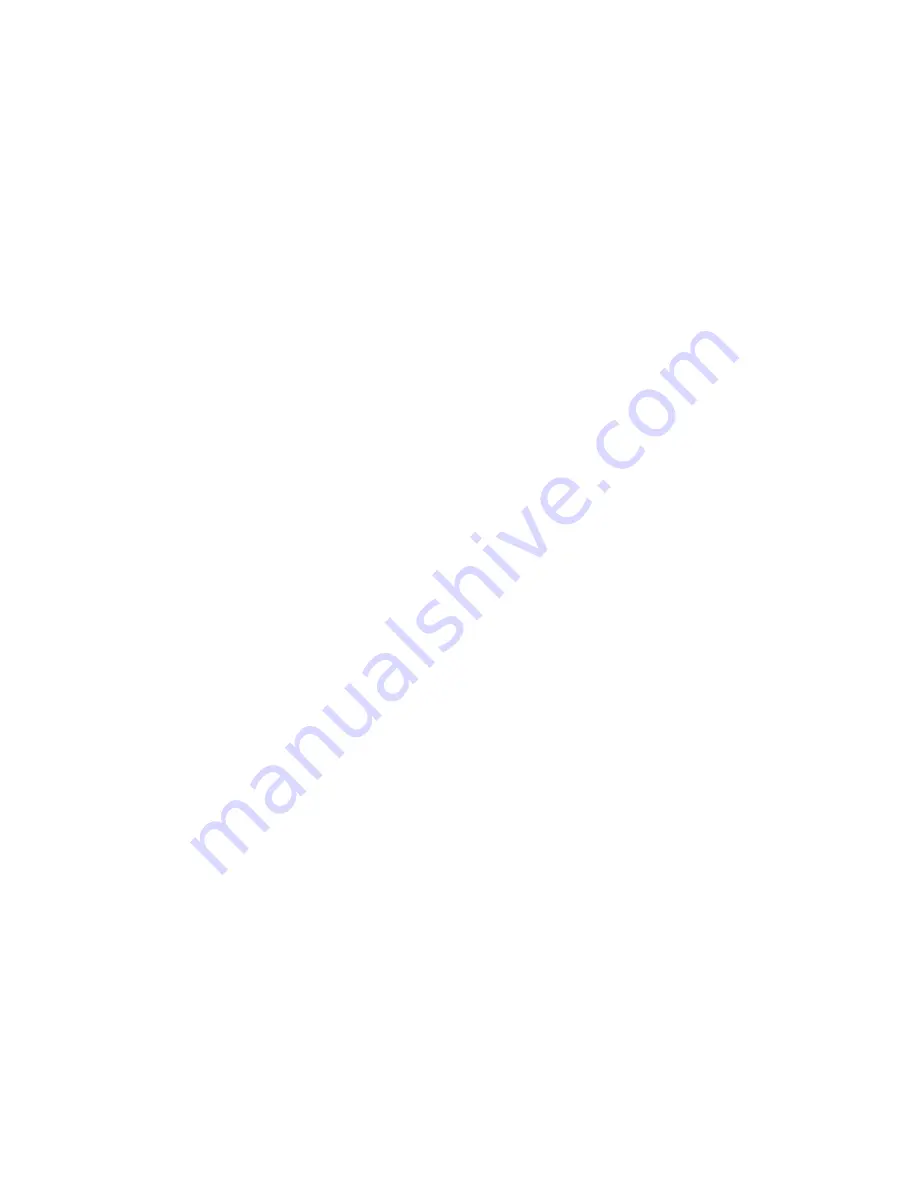
5.5.4
Using the SRD:
Do not use the SRD if inspection shows damage or any malfunction. Don the FBH in accordance with the FBH
manufacturer’s instructions. Follow the instructions contained in this manual and on the labels. Failure to follow instructions may result
in serious injury or death. Connect the SRL-FBH Connector to the dorsal D-ring on the FBH. Ensure the connector closes and locks. Attach
the leg-end carabiner to the chosen anchorage and ensure the leg-end connector closes and locks. Ensure all connections are compatible.
Normal operation will allow the working length of the lifeline to extend and retract as the worker moves about. A certain amount of
tension must remain on the web at all times to ensure proper operation of the internal brake. Do not allow the lifeline to become slack.
If the lifeline becomes slack, remove the SRD from service for inspection. See Section 7.
Avoid sudden or quick movements during the normal work operation, as this may cause the SRD brake to engage and possibly cause loss
of balance and injury or death.
If a fall occurs, the brake will engage and lock the lifeline. The EA will deploy to arrest the fall and limit arrest forces on the user.
•
DO NOT extend the lifeline past the operational limit.
•
DO NOT allow one SRD lifeline to become tangled or twisted with another SRD lifeline during use.
•
DO NOT allow any lifeline to pass under arms or between legs during use.
•
DO NOT clamp, knot, or prevent the lifeline from retracting or being taut.
•
DO NOT lengthen the SRD by connecting a lifeline or similar component.
•
DO NOT allow the lifeline to remain outside the housing when not in use.
102022
MSRD07 Rev F
10
Avoid sudden or quick movements during the normal work operation, as this may cause the SRL pawl system to engage and possibly
cause loss of balance, which may cause injury or death. If a fall occurs, the pawl system will engage and lock the lifeline. The EA will
deploy to arrest the fall and limit arrest forces on the user.
5.5.1
Locking Mechanism:
The SRD utilizes an acceleration based locking mechanism. The locking function requires a certain payout rate during
a fall event to function correctly. Certain situations, confined or cramped spaces, shifting footing such as sand, gravel, grain, or a sloped
surface may not allow the lifeline to reach sufficient speed to activate the lock mechanism. A clear path is required to assure positive
locking of the SRD. Ensure the lock is functioning properly. Pull the lifeline out a short distance and give it a sharp tug. The lifeline must
lock. If it fails to lock, remove it from service immediately. Ensure the work zone remains within stated parameters.
5.5.2
Visual Indicator:
The primary fall arrest impact indicator is the energy absorber in the lifeline between the housing and the leg-end
connector. Torn stitching, deployment, expansion, or lengthening of the white internal energy absorber webbing is an indication that a fall
event has occurred and the unit must be removed from service. Remove from service any unit that fails inspection, including inspection of
the fall arrest impact indicator. If you have any questions, contact FallTech.
5.5.3
After A Fall:
A fall event over an edge may require special rescue equipment and measures. Ensure a written rescue plan, method and
system is in place and readily available to all users for rapid response. Ensure all users are trained in rescue procedures. If a fall event
occurs, remove it from service, and store it separately. Remove from service any unit that has been subjected to fall arrest forces or that
exhibits damage consistent with such forces. For questions, contact FallTech.