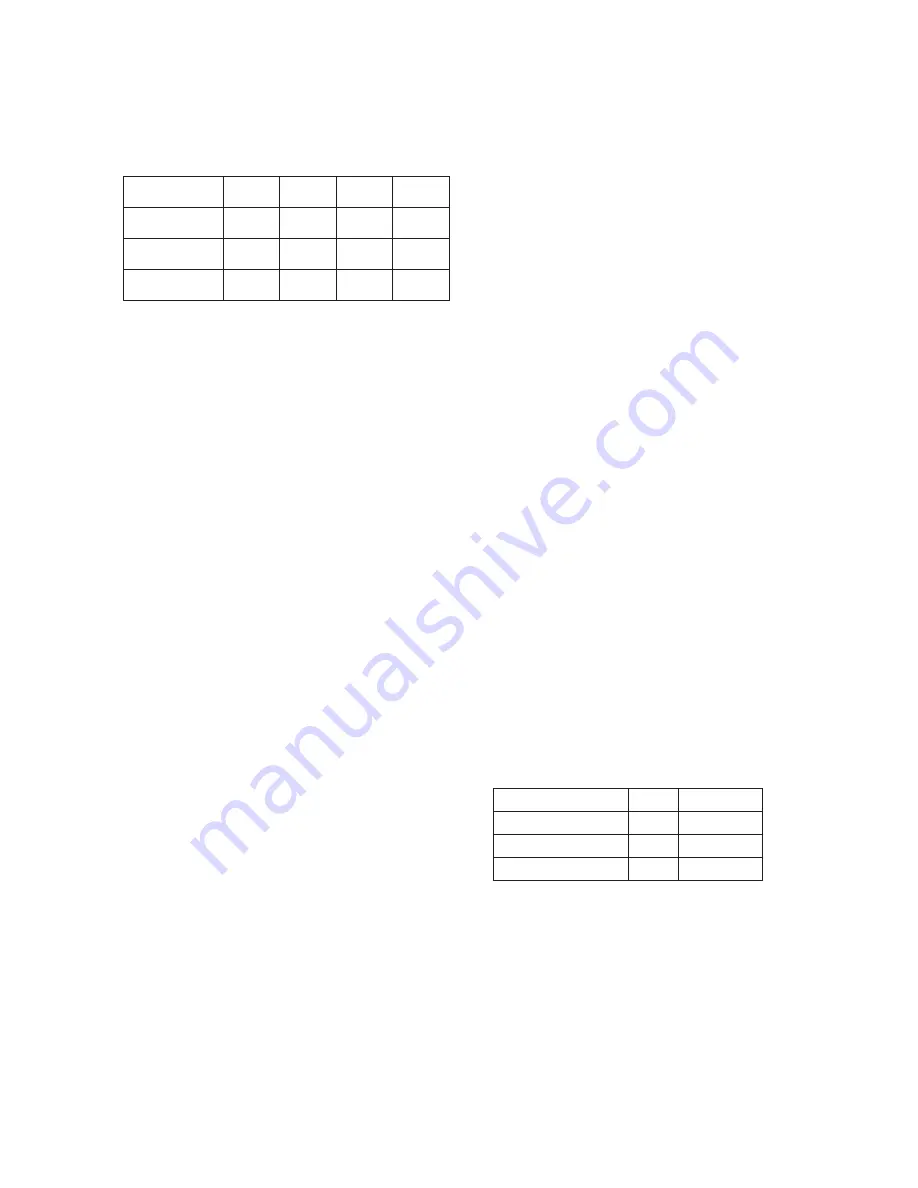
1.4 GAS SUPPLY
The incoming service must be of sufficient size to supply
full rate gas without excessive pressure drop. A gas meter
is connected to the service pipe by Gas Supplier.
Any existing meter should be checked by the supplier to
ensure that it is of adequate capacity to pass required
rate of gas for the unit, in addition to any other gas
equipment that has been installed.
The multifunctional control has an in-built governor
therefore an external device does not require to be fitted.
Installation pipework should be fitted in accordance with
IGE/UP/2. This should not be smaller than gas inlet
connection.
G3830
- Rp½
(½" BSP)
G3860
- Rp¾
(¾" BSP)
G3865
- 2 x Rp½
(½" BSP)
An inlet manifold may be purchased to connect G3865 to
1 x Rp¾
(¾" BSP)
mains inlet.
An isolating cock must be located close to the unit to
allow shutdown during an emergency or servicing.
The installation should be checked for gas tightness and
purged as specified in IGE/UP/1.
1.5 ELECTRICAL SUPPLY
Not applicable to these units.
1.6 WATER SUPPLY
Not applicable to these units.
1.7 TOTAL GAS RATES -
NATURAL and PROPANE GAS
1.1 MODEL NUMBERS, NETT WEIGHTS
and DIMENSIONS
1.2 SITING
The unit should be installed on a level, fireproof surface
in a well lit, draught free position. A clear space of 150mm
should be left between the rear and sides of the fryer and
any combustible wall.
If the floor is constructed of combustible material,
then local fire requirements should be checked to ensure
compliance.
Important
If appliance is to be installed in suite formation with other
matching units, the instructions for all models must be
consulted to determine the necessary clearances to any
combustible rear wall or overlying surface. Some models
require greater clearances than others and the largest
figure quoted in individual instructions will therefore
determine clearance of complete suite adjoining
appliances.
1.3 VENTILATION
Adequate ventilation must be provided to supply sufficient
fresh air for combustion. This should allow easy removal
of combustion products which may be harmful to health.
Recommendations for Ventilation of Catering Appliances
are given in BS5440:2.
For multiple installations, the requirements for individual
units require to be added together. Installation should be
carried out in accordance with local and/or national
regulations which apply at the time. A competent installer
MUST be employed.
Model
Width
(mm)
Depth
(mm)
Height
(mm)
Weight
(kg)
G3830 Fryer
300
770
870
59
G3860 Fryer
600
770
870
74
G3865 Fryer
600
770
870
99
SECTION 1 - INSTALLATION
UNLESS OTHERWISE STATED, PARTS WHICH HAVE BEEN PROTECTED BY THE MANUFACTURER
ARE NOT TO BE ADJUSTED BY THE INSTALLER.
Model
kW
Btu/hr
G3830 Fryer
18.1
61,757
G3860 Fryer
32.5
110,890
G3865 Fryer
2 x 18.1
2 x 61,757
Summary of Contents for G3830
Page 8: ......