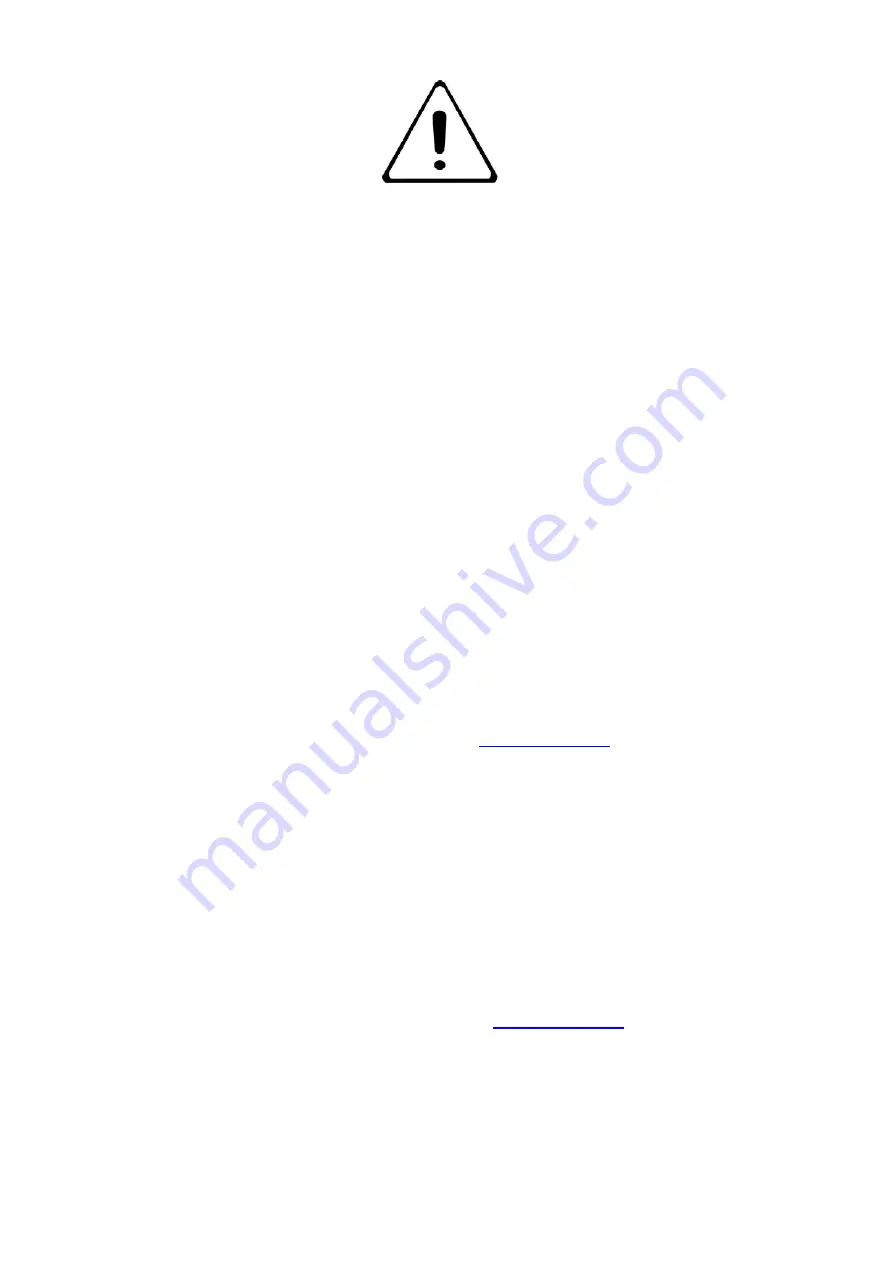
3
These instructions are only valid if the country code appears on the
appliance. If the code does not appear on the appliance, refer to the
technical instructions for adapting the appliance to the conditions for use
in that country.
Installation must meet national or local regulations. Attention must be paid
to: gas safety (installation & use) regulations, health and safety at work
act, local and national building regulations, fire precautions act.
To prevent shocks, all appliances must be earthed.
This appliance has been CE-marked on the basis of compliance with the
Low Voltage and EMC Directives for the voltages stated on the data plate.
This equipment is for professional use only and must be used by
competent persons.
The installer must instruct the responsible person(s) of the correct
operation and maintenance of the appliance.
Training and competence
To help ensure the safe use of this appliance there is a requirement for you to
provide whatever information, instruction, training and supervision as is
necessary to ensure, so far as is reasonably practicable, the health and safety of
all users.
For further help and information on training and competence we would refer you
the Health and Safety Executive website;
www.hse.gov.uk
document ref: health
and safety training INDG345. International customers should default to the health
and safety guidelines provided by your government body.
Risk assessment
As part of managing the health and safety of your business you must control any
risks identified in your commercial kitchen. To do this you need to think about
what might cause harm to people and decide whether you are taking reasonable
steps to prevent that harm. This is known as risk assessment. It is important to
consider the environment around the product as well as the product itself. For
example oil or food spills will present a significant risk so users so the need to
immediately clean up such spills must be reflected in staff training.
For further help and information on risk assessments we would refer you to you
the Health and Safety Executive website;
www.hse.gov.uk
document ref: risk
assessment INDG163. International customers should default to the health and
safety guidelines provided by your government body.
Cleaning and maintenance
When removing heavy items to aid cleaning or maintenance particular care
Summary of Contents for 100LT
Page 21: ...21 4 2 MEASURING INLET PRESSURE A Inlet pressure intake B Outlet pressure intake A B...
Page 23: ...23 4 4 PILOT BURNER A Thermocouple B Pilot burner C Ignition plug D Injector E Tightness screw...
Page 24: ...24 4 5 MAIN BURNER A Burner B Injector C Injector pipe B C A 4 6 PRIMARY AIR REGULATION H...