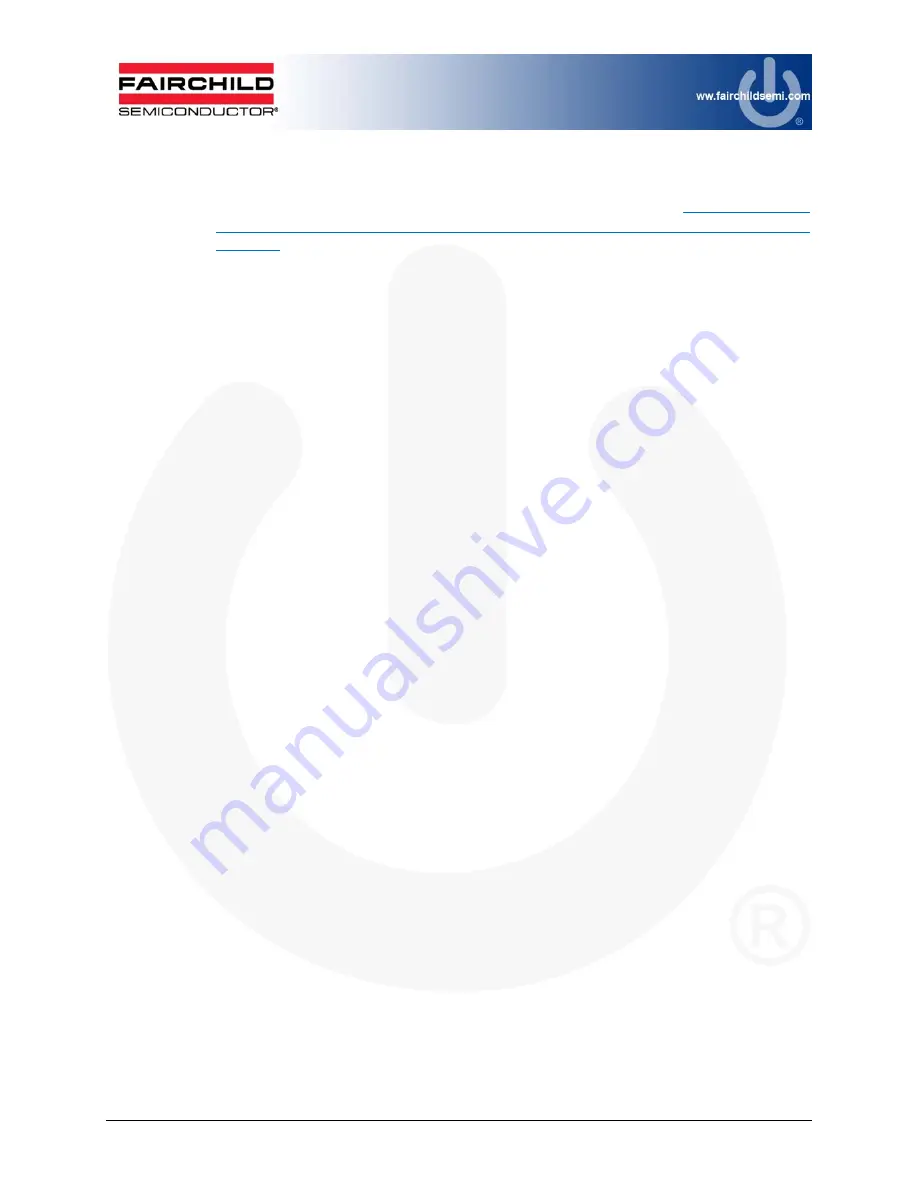
© 2012 Fairchild Semiconductor Corporation
3
FEBFAN9611_S01U300A • Rev. 0.0.1
The following user guide supports the FAN9611 300W evaluation board for interleaved
boundary-conduction-mode power-factor-corrected supply. It should be used in
conjunction with the FAN9611 datasheet, Fairchild application note
AN-6086 —Design
Considerations for Interleaved Boundary-Conduction Mode PFC Using FAN9611 /
FAN9612
and FAN9611/12 PFC Excel®-based Design Tool.
1.
Overview of the Evaluation Board
The FAN9611 interleaved, dual Boundary-Conduction-Mode (BCM), Power-Factor-
Correction (PFC) controllers operate two parallel-connected boost power trains 180º out
of phase. Interleaving extends the maximum practical power level of the control
technique from about 300W to greater than 800W. Unlike the Continuous Conduction
Mode (CCM) technique often used at higher power levels, BCM offers inherent zero-
current switching of the boost diodes (no reverse-recovery losses), which permits the use
of less expensive diodes without sacrificing efficiency. Furthermore, the input and output
filters can be smaller due to ripple current cancellation between the power trains and
doubling of effective switching frequency.
The advanced line feed-forward with peak detection circuit minimizes the output voltage
variation during line transients. To guarantee stable operation with less switching loss at
light load, the maximum switching frequency is clamped at 525kHz. Synchronization is
maintained under all operating conditions.
Protection functions include output over-voltage, over-current, open-feedback, under-
voltage lockout, brownout, and redundant latching over-voltage protection. FAN9611 is
available in a lead-free, 16-lead, Small-Outline Integrated-Circuit (SOIC) package.
This FAN9611 evaluation board uses a four-layer Printed Circuit Board (PCB) designed
for 300W (400V/0.75A) rated power. The maximum rated power is 350W and the
Maximum On-Time (MOT) power limit is set to 360W. The FEBFAN9611_S01U300A
is optimized to demonstrate all the FAN9611 efficiency and protection features in a low-
profile height form factor less than 18mm.