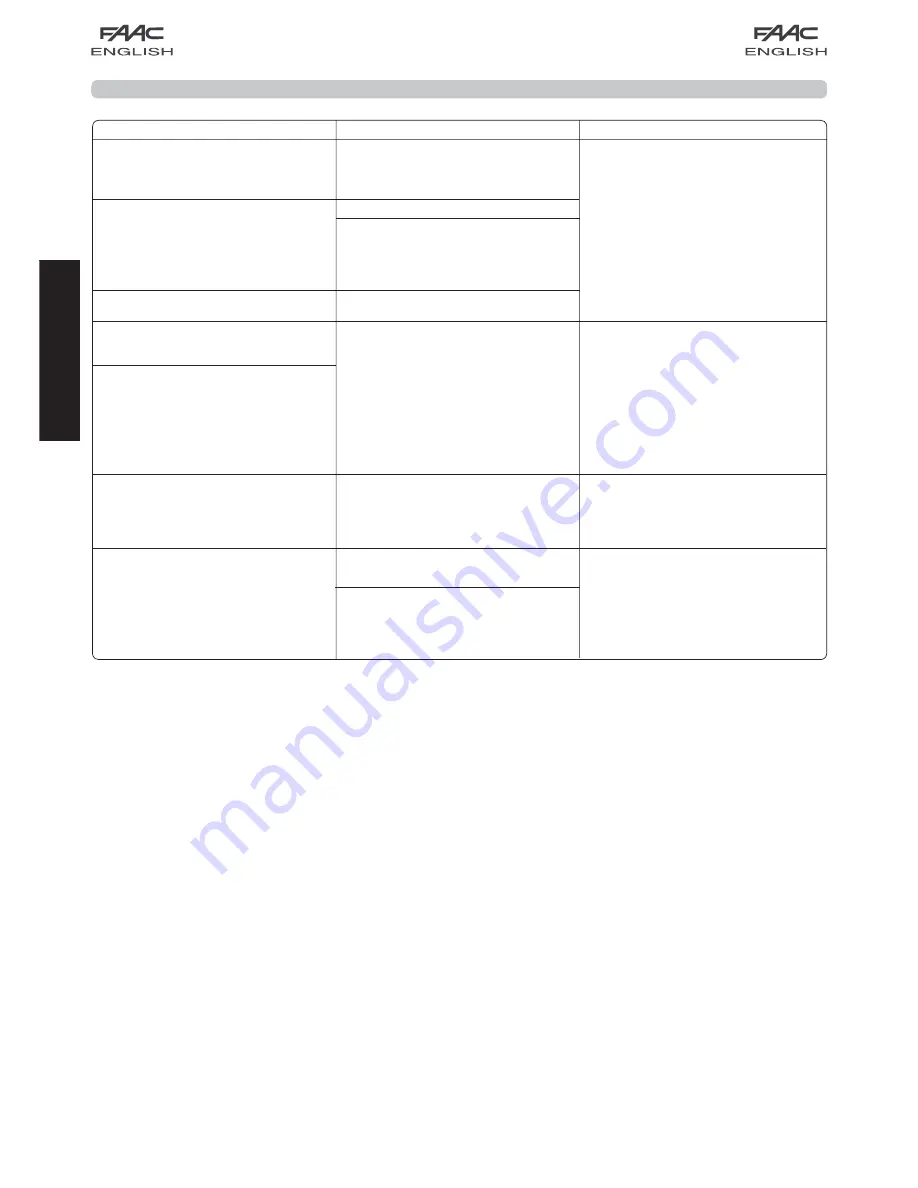
17
ENGLISH
18
. TROUBLESHOOTING
Trouble
Possible causes
Solution
When the learning procedure is started,
the SET UP LED flashes but the automated
system does not perform any
manoeuvre
The STOP and FSW safety devices are
enabled also during the learning stage.
Non-connection or wrong connection
prevents the operator from working
Check the LEDs’ status following the
instructions of the “Inputs status LEDs”.
Check the connections shown in fig. 27
The automated system does not
perform any movement
STOP command enabled
The automated system opens the door
but does not close it
FSW safety devices engaged
The Fail-Safe function is enabled, but the
NC contact of the devices connected
to the FSW input does not open during
test by the unit before the manoeuvre
is started
Learning is not finished correctly and the
SET UP LED flashes to signal a fault
The automated system frequently
reverses motion during the opening
and/or closing manoeuvre
-The automated system detects that
the door movement is too difficult.
- If you are using manual adjustment of
force, the set thrust could be insufficient.
Check the balance of the door and
make sure that it moves without too much
friction. Move the door manually, using
the rod fitting on the door, and check
if the movement is smooth and does
not require too much traction or thrust.
Execute a new learning cycle. If necessary,
vary the thrust force (if using manual
adjustment) or start learning with a ma-
ximum thrust of 1000N.
It is difficult to release the automated
system while the door is closed
Too much mechanical load on the release
system with the door closed
Run a new learning cycle and,
when over, lighten the closing thrust,
commanding the carriage to withdraw
as described in paragraph 11.2.
The SET UP LED flashes to signal a fault
status
The learning cycle did not finish
positively.
Run a new learning cycle
DS1’s switch No. 3 (automatic/manual
adjustment of force) was shifted and a
new learning cycle was not executed.
Summary of Contents for D1000
Page 1: ...D1000 D1000...