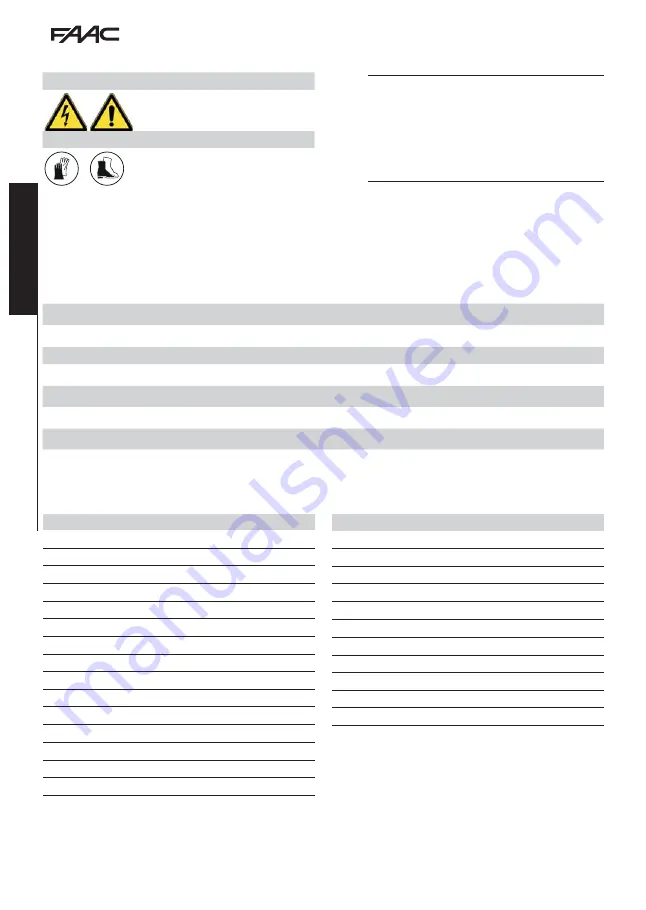
B614
32
732998 - Rev.A_DRAFT
Tr
ansla
tion of the original instruc
tions
ENGLISH
7. ELECTRONIC INSTALLATION
RISKS
PERSONAL PROTECTIVE EQUIPMENT
F
ALWAYS DISCONNECT THE POWER SUPPLY before working
on the board. Turn power on only after having made all
the electrical connections and carried out the preliminary
start-up checks.
The board cover must never be removed unless the board
is to be replaced. No installation operation requires the
removal of the cover.
7.1 BOARD E614
7
Board technical data sheet E614
230V~
115V~
Supply voltage
220-240 V~ 50/60 Hz
115V~ +/-10% 50/60 Hz
Max power
150 W
150 W
Accessory output voltage
24 V
"
24 V
"
Max. accessories load
500 mA
500 mA
Max. accessories load BUS 2easy
500 mA
500 mA
Max. flashing light load
Ambient operating temperature
-20 °C - +55 °C
COMPONENTS
See figure
42
BOARD:
J1
Mains power supply terminal board
J3
Terminal board for BUS 2easy
J6
Accessory/input terminal board
J7
Radio module connector XF
J8
Battery connector XBAT 24
J10
Terminal board for external detector LOOP1
J11
Connector for encoder
J13
Terminal board for external detector LOOP2
J16
Terminal board for external flashing light
J18
Terminal board for the beam lights
J20
Terminal board for outputs
J21
Connector for integrated flasher
J23
Connector for motor
F3
Board protection fuse (F3 = T2.5A)
DISPLAY
Programming display
BOARD:
DL1
Device signalling LED to BUS 2easy ACTIVE
DL2
BUS 2easy “BUS MON“ diagnostic signalling LED
DL3
“RADIO1” (OMNIDEC) signalling LED
DL4
“RADIO2” (OMNIDEC) signalling LED
DL5
Error/alarm signalling LED
DL8
EMER status LED
DL9
STOP/FSW-CL status LED
DL10
CLOSE status LED
DL11
OPEN status LED
DL12
LOOP1 status LED
DL13
LOOP2 status LED