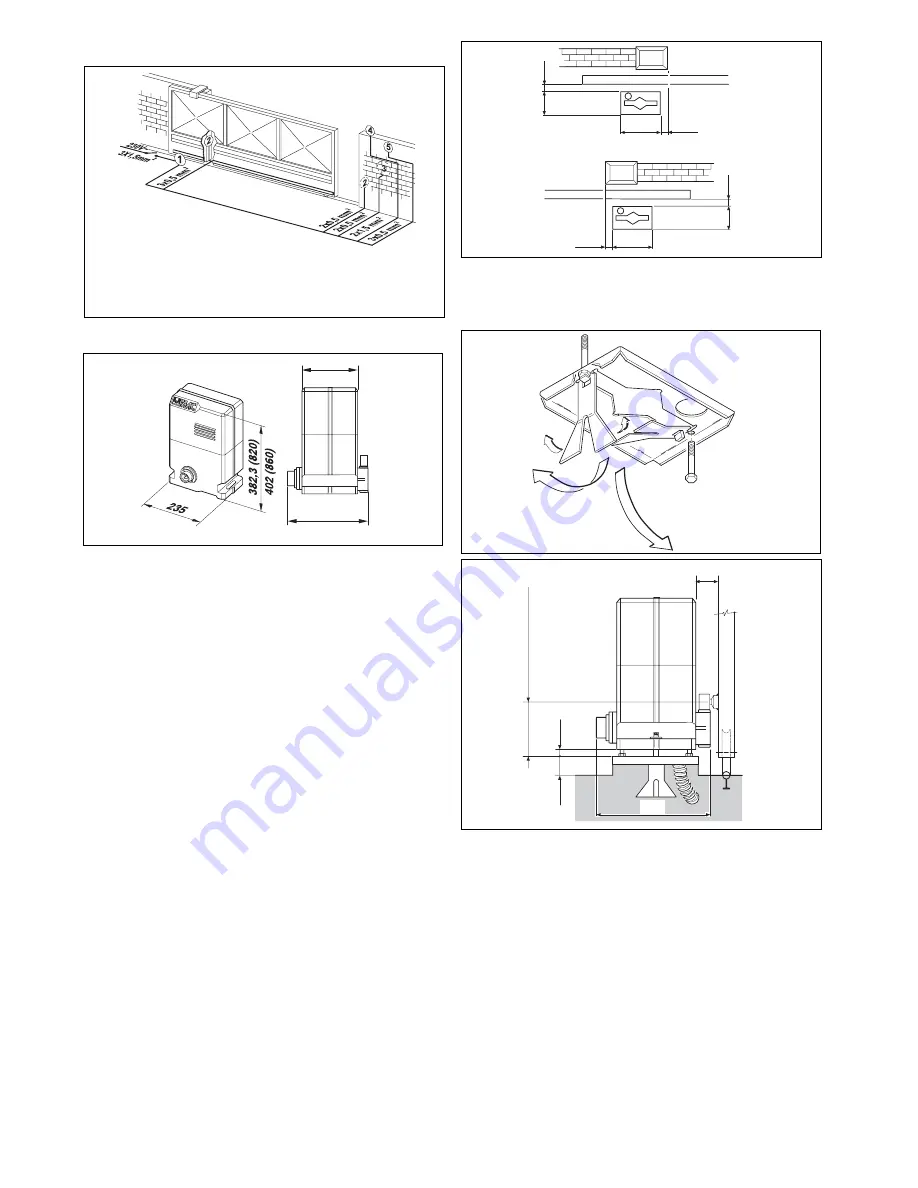
4
4. INSTALLING THE AUTOMATION
4.1.
PRELIMINARY CHECKS
For safe, correct operation of the automation, make sure
that the following requirements are met:
•
The gate’s structure must be suitable for automation.
Take special care to ensure that the wheels are large
enough to support the full weight of the gate, that a
top runner is installed and that mechanical limit stops
are fitted to prevent the gate from coming off the
runner.
•
The characteristics of the ground must ensure sufficient
support for the foundation plinth.
•
There must be no pipes or electrical cables in the area
to be dug for installing the foundation plinth.
•
If the gear motor is located in a vehicle transit area, it
is a good idea to provide protection against accidental
collisions.
•
Check that the gear motor has an efficient earth
connection.
4.2.
INSTALLING THE BASE PLATE
1) The base plate must be positioned as shown in Fig. 4
(right-handed closure) or Fig. 5 (left-handed closure) to
ensure that the pinion and rack mesh correctly.
N.B.:
It is advisable to install the base plate on a concrete
base raised about 50 mm from the ground (Fig. 7).
2) Assemble the foundation plate as shown in Fig. 6.
3) Prepare a foundation plinth as shown in Fig. 8 and install
the base plate providing one or more conduits for
electrical cables. Use a level to check that the plate is
perfectly horizontal and wait for the cement to set.
4) Set up the electrical cables for connection to the
accessories and the electricity supply as described in
section 2. For ease of connection, ensure that the
cables protrude by about 45 cm from the hole in the
base plate.
햲
820/860 operator with
826 MPS control unit
햳
Photocells
햴
Key switch
햵
Flashing light
햶
Radio receiver
Fig. 2
3. DIMENSIONS
221,2
140
Fig. 3
Values are expressed in mm.
40
165
40
165
235
235
0
¸
50
0
¸
50
Fig. 4
Fig. 6
4.3.
MECHANICAL INSTALLATION
1) With the aid of a Teflon hammer insert the adjustable
feet into the hexagonal holes under the base of the
gear motor as shown in Fig. 9.
2) Remove the casing and position the gear motor on the
foundation plate, threading the electrical cables into
the conduit in the operator body.
3) Adjust the height of the feet and the distance from the
gate as shown in Fig. 7.
4) Secure the gear motor onto the base plate using the
two nuts and the plates provided as shown in Fig. 10.
5) Set up the operator for manual operation as described
in section 6.
6) Remove the breather screw as shown in Fig. 11 and
keep it in a safe place.
13
53
221,2
50
Z20 131 mm (820)
Z16 123 mm (860)
Fig. 7
2. ELECTRICAL SET-UP (standard system)
Fig. 5