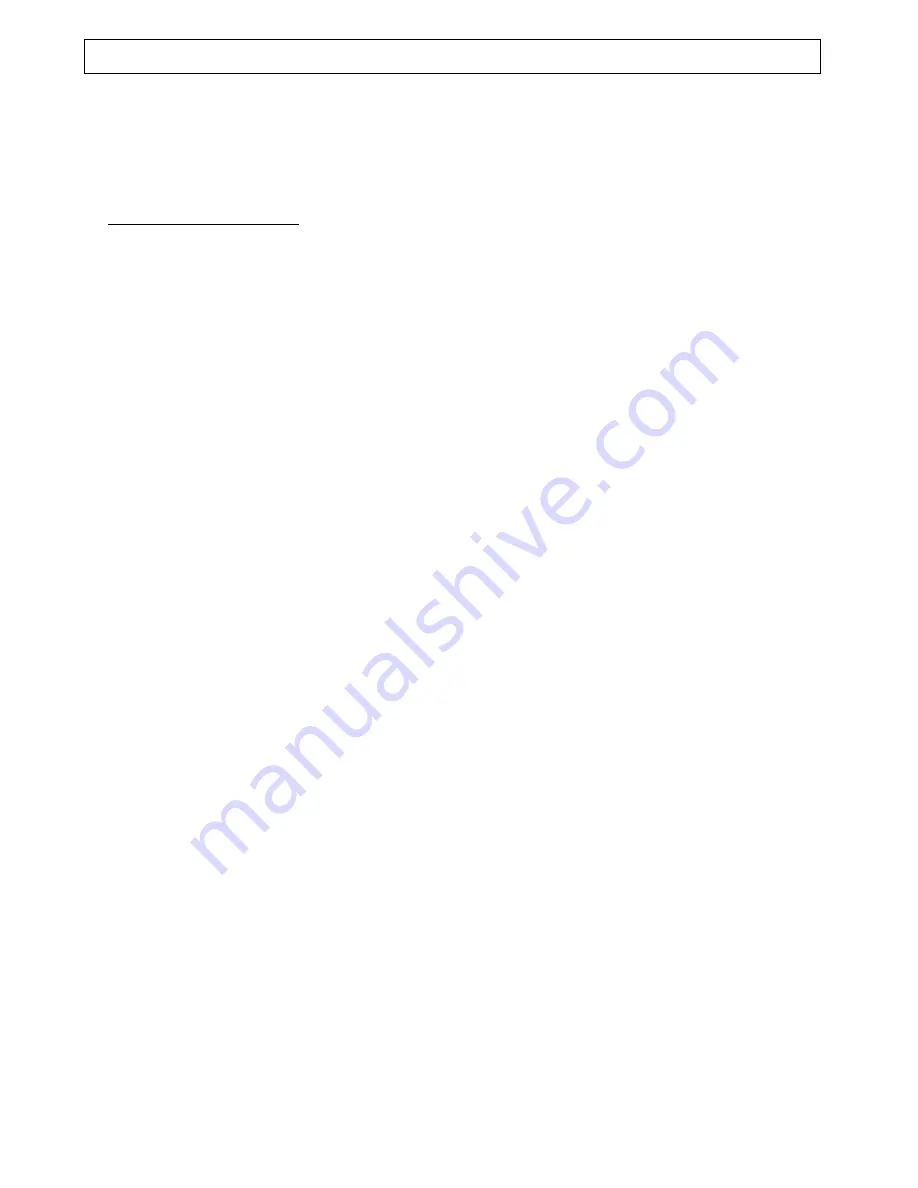
2
IMPORTANT NOTICE FOR THE INSTALLER
GENERAL SAFETY REGULATIONS
1) WARNING! FAAC strongly recommends to follow these instructions literally for the safety of persons. Improper
installation or misuse of the product will cause very serious damages to persons.
2) Packaging material (plastic, polystyrene etc.) is a potential hazard and must be kept out of reach of children.
3) Read the instructions carefully before installing the product.
4) Keep these instructions for future reference.
5) This product has been designed and manufactured only for the use stated in this manual. Any other use not expressly
set forth will affect the reliability of the product and/or could be source of hazard.
6) FAAC S.p.A. cannot be held responsible for any damage caused by improper use or different from the use for which
the automation system is destined to.
7) Do not use this device in areas subject to explosion: the presence of flammable gas or fumes is a serious hazard.
8) Mechanical constructive elements must comply with UNI8612, CEN pr EN 12604 and CEN pr EN 12605 standards.
Countries outside the EC shall follow the regulations above besides their national normative references in order to
offer the utmost safety.
9) FAAC cannot be held responsible for failure to observe technical standards in the construction of gates and doors,
or for any deformation of the gates which may occur during use.
10) Installation must comply with UNI8612, CEN pr EN 12453 and CEN pr EN 12635.
The degree of safety of the automation must be C+E.
11) Before carrying out any operations, turn off the system’s main switch.
12) An omnipower switch shall be provided for the installation with an opening distance of the contacts of 3 mm or more.
Alternatively, use a 6A thermomagnetic breaker with multi-pole switching.
13) Ensure that there is a differential switch up-line of the electrical system, with a trip threshold of 0.03A.
14) Check that the earthing plant is in perfect condition and connect it to the metallic parts. Also earth the yellow/green
wire of the operator.
15) The automation is fitted with an anti-crush safety system that is a torque control device. In any case, further safety
devices shall be installed.
16) The safety devices (e.g. photocells, safety edges, etc.) protect areas where there is a mechanical movement
hazard, e.g. crushing, entrapment and cutting.
17) Each installation must be fitted with at least one flashing light (e.g. FAAC LAMP, MINILAMP etc.) as well as a warning
plate suitably fixed to the gate, besides the safety devices as per point 16. above.
18) FAAC cannot be held responsible regarding safety and correct functioning of the automation in the event that parts
other than FAAC original parts are used.
19) Use only FAAC original spare parts for maintenance operations.
20) Do not carry out any modifications to automation components.
21) The installer must supply all information regarding manual operation of the system in the event of an emergency
and provide the end-user with the "End-user Guide" attached to the product.
22) Keep out of persons when the product is in operation.
23) Keep out of reach of children the remote radio controls and any control devices. The automation could be
operated unintentionally.
24) The end-user must avoid any attempt to repair or adjust the automation personally. These operations must be
carried out exclusively by qualified personnel.
25) What is not explicitly stated in these instructions is not permitted.