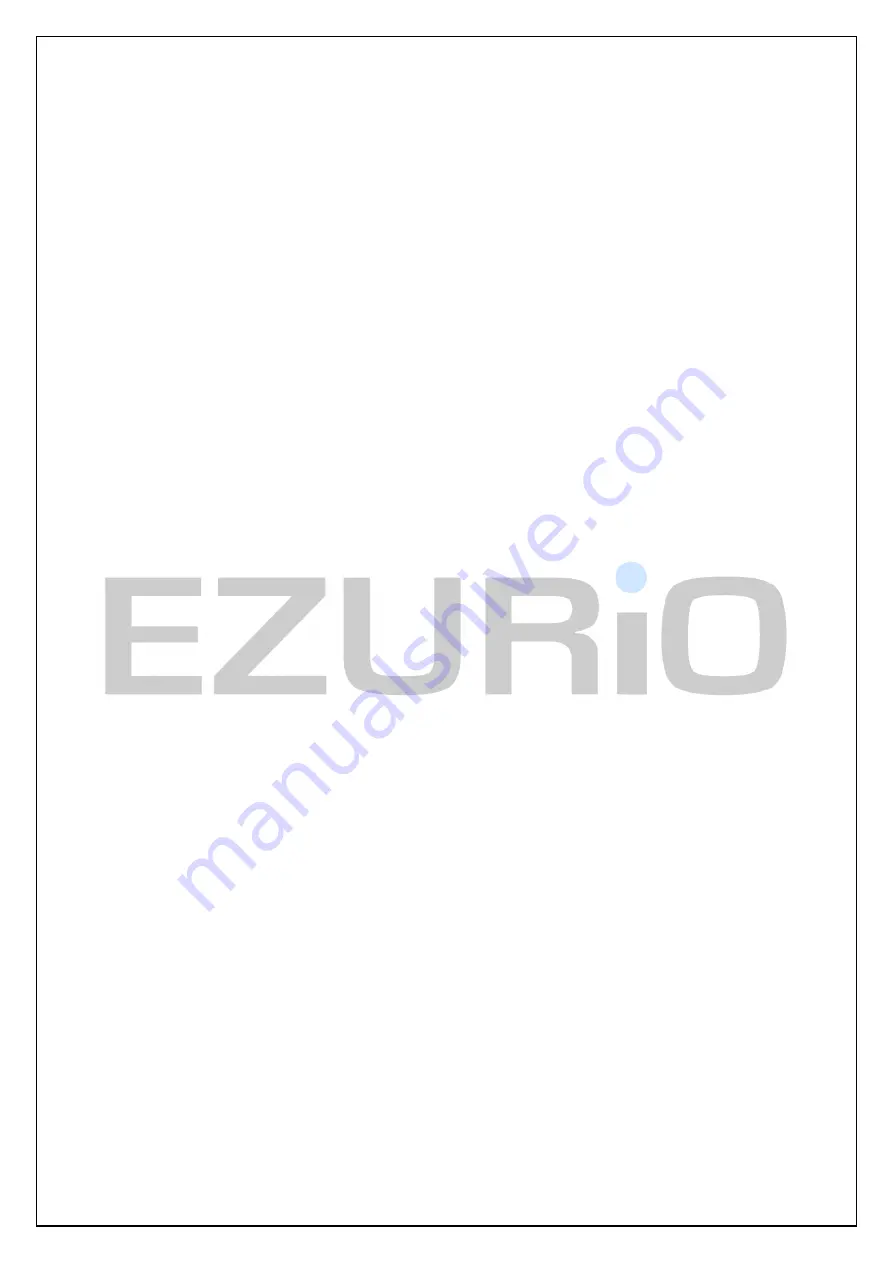
www.ezurio.com
DSH_BT024-00200_1v4 © Ezurio Ltd 2006
18
10.
Application Information
10.1
Antenna Position
The antenna used on the Embedded Intelligent
Bluetooth
module is designed to be largely immune from the
effects of proximity detuning. Normally, antennas operating at 2.4GHz are affected by their surroundings, so that
great care is needed in their placement and orientation.
The Embedded Intelligent Serial Module can be used in most locations and orientations and is only marginally
affected by the presence of a significant ground plane in close proximity.
The antenna distribution is close to isotropic, which means that the orientation of mounting has only a limited
effect on the overall range. However the optimum range is achieved when the two antennae are directly facing
each other
The module should not be located in a sealed metal enclosure, as this will act as a Faraday cage and severely
attenuate the radio signal. A distance of 6mm has been allowed between the metal shield and the antenna to
allow the antenna to protrude through a slow in a metal enclosure.
10.2
Power Supply Considerations
The power supply for the Module has to be a single voltage source of Vcc within the range of 3.3 V to 7.0 V. It
must be able to provide sufficient current in a transmit burst. This can rise to 65mA.
10.3
Power-On-Reset
The Module is provided with an active low reset pin. Upon the application of power, the Power On Reset circuit
built into the Module will ensure that the unit starts correctly. The internal reset circuit is triggered when the
input voltage to the module drops below ~1.7V and is hence only suitable for providing a power on reset signal. If
the supply voltage to the module can drop below the minimum voltage level in normal operation, then it is
recommended that an external brownout circuit is provided to assert the module reset and to ensure that the
module is reset when the module supply voltage drops below 3.1V.
This will ensure that the module will return to an operational state when the supply voltage comes back within
specification. For example, if the module supply can drop to 2.7V and then be restored to 3.3V there is no
guarantee that the module will still be operational unless the reset signal has been asserted.
10.4
RF Shield
To meet FCC requirements and to facilitate IR soldering, all modules are supplied with a soldered RF shield. This
meets the requirement that users may not be able to access RF circuitry without special tools. Removal of the
shield may negate RF approvals.
10.5
Mounting the Module onto the application platform
The antenna (Brown square component on top side of PCB) is designed to minimise detuning effects from nearby
components and metalwork. However, it is good design practise to ensure that other active circuitry is kept away
from the antenna.
The proximity of the antenna to large metallic objects can affect the range and performance of the system.
Designers should carefully consider the location of the Module and the type of enclosure material that is used.
No tracks should be present on the top layer of the board on which the module is soldered, as these may cause
inadvertent connections to test pads. The recommended land pattern for the mother PCB is detailed below