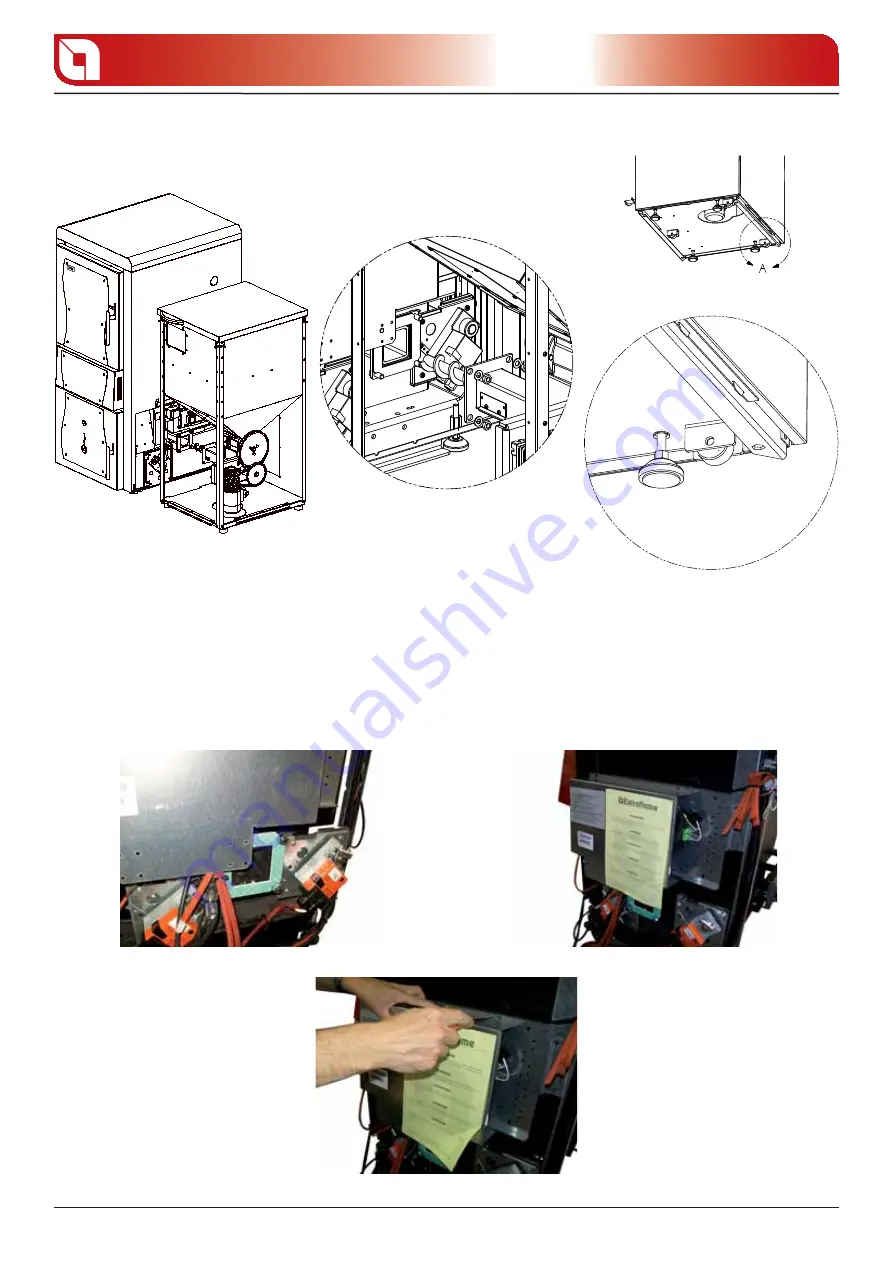
POSITIONING AND MOUNTING THE SILO
46
Chapter 7
Chapter 7
POSITIONING AND MOUNTING THE SILO
To mount the silo, proceed as illustrated in the above fi gures:
Dismantle the front panel of the silo.
Place the silo side by side of the boiler body.
Insert the feeding spiral in the boiler pipe and block everything using the nuts provided, as illustrated
in detail, screw the feet to fi x the silo.
fi gure 7.1
fi gure 7.2
fi gure 7.3
fi gure 7.4
fi gure 7.5
fi gure 7.6