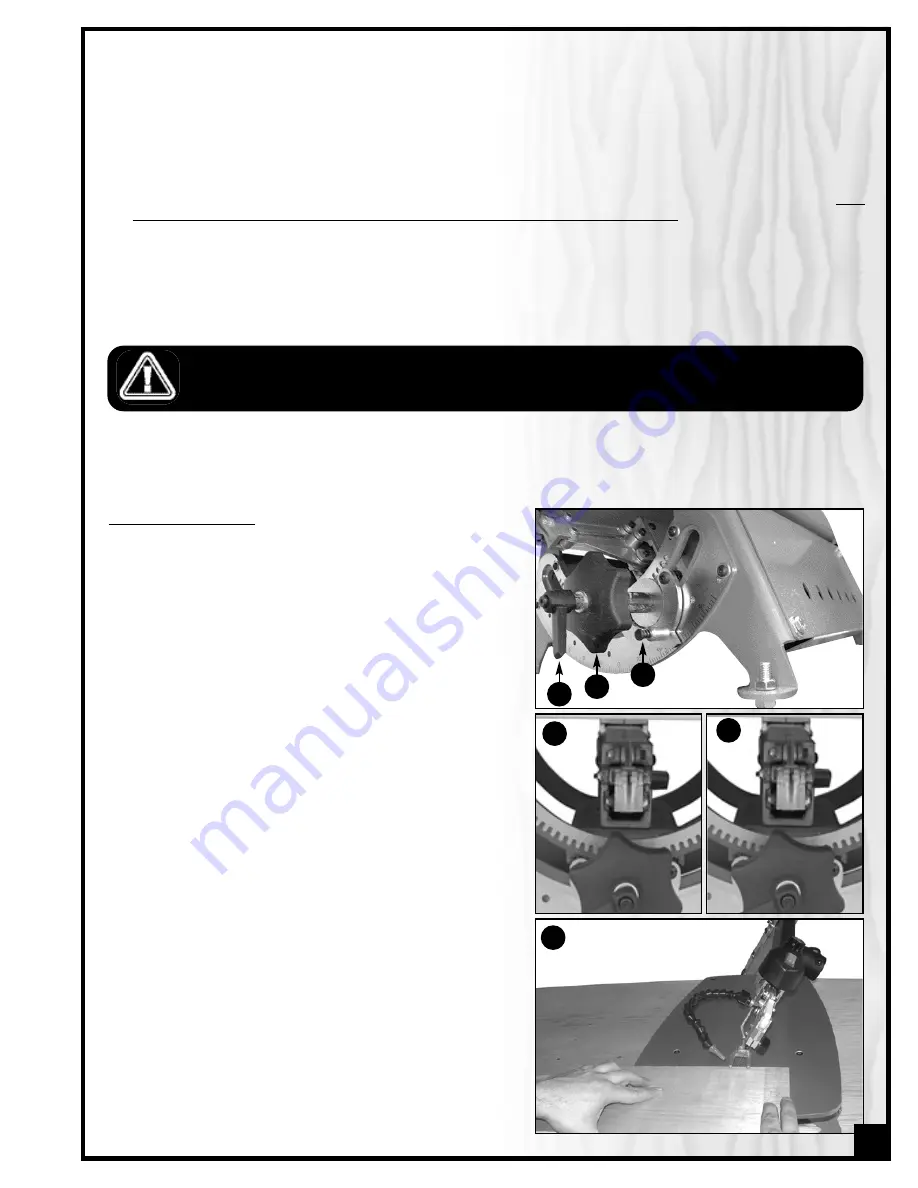
3.
Release tension on the blade by flipping the blade tension lever forward.
4.
Loosen the thumbscrew on the lower blade mount, located under the table, to release the blade from the mount.
5.
Raise the upper arm assembly which will lift the blade up through the hole and above the table.
6.
Position the workpiece on the table so that the guide hole lines up with the hole in the table.
7.
Lower the arm assembly with one hand while guiding the blade through the hole in the workpiece and table.
8.
Re-install the bottom end of the blade in the lower blade mount and tighten the thumbscrew, only
enough to secure the blade in the lower blade clamp and prevent it from slipping.
Note: Overtightening the blade clamp thumbscrews can cause premature wear to the blades gripping surface and result
in blade slippage or cause premature wear of the threads in the blade clamp housing. (added this sincd Norm’s copy)
9.
Flip back the blade tension lever to re-tension the blade and test the blade tension as described in
“Installing or Changing Blades” section of this manual.
10.
To begin cutting follow the same steps as described in “Basic 90° straight or curved cuts” section on page 13 of
this manual.
TO REDUCE THE RISK OF INJURY, ALWAYS TURN OFF THE SAW AND WAIT FOR THE BLADE TO COME TO
A COMPLETE STOP BEFORE REACHING IN TO REMOVE WASTE MATERIAL FROM A FRET CUT.
ANGLE OR BEVEL CUTTING
One of the unique features of the EX-16 Scroll Saw is the ability
to tilt the head of the saw in order to make angle or bevel cuts.
The table and the workpiece always stay horizontal (parallel to
the floor) while the blade tilts, keeping your hands in the same
comfortable cutting position as they would normally be for
regular right angle cuts.
Because you are not fighting gravity or working with your
hands or wrists bent in awkward positions, it can be a huge
advantage and makes it easier and safer to make accurate
bevel cuts.
The blade tilt controls are located under the table at the front
saw. To tilt the blade for bevel cutting:
1.
Release the locking lever
A
by turning counter-clockwise.
2.
Turn the tilting handle
B
left or right to set the blade to the
desired angle.
Note: Push in and hold the spring loaded indexing pin C to locate
the following common angles: 90º, 45º, 30º & 22.5º both left and
right.
When tilting the blade to the left at extreme angles, it may be
necessary to remove and reverse the lower blade mount thumb-
screw assembly in order to maximize clearance under the table.
(
D
shows the lower blade mount in default position and
E
shows
it reversed).
3.
Tighten the locking lever
A
to secure the blade at the
desired angle.
4.
To begin cutting, follow the same steps as described in
“Basic 90° straight or curved cuts” section on page 13 of
this manual. Letter
F
shows the scroll saw in position for
bevel cutting.
B
C
A
D
E
F
15