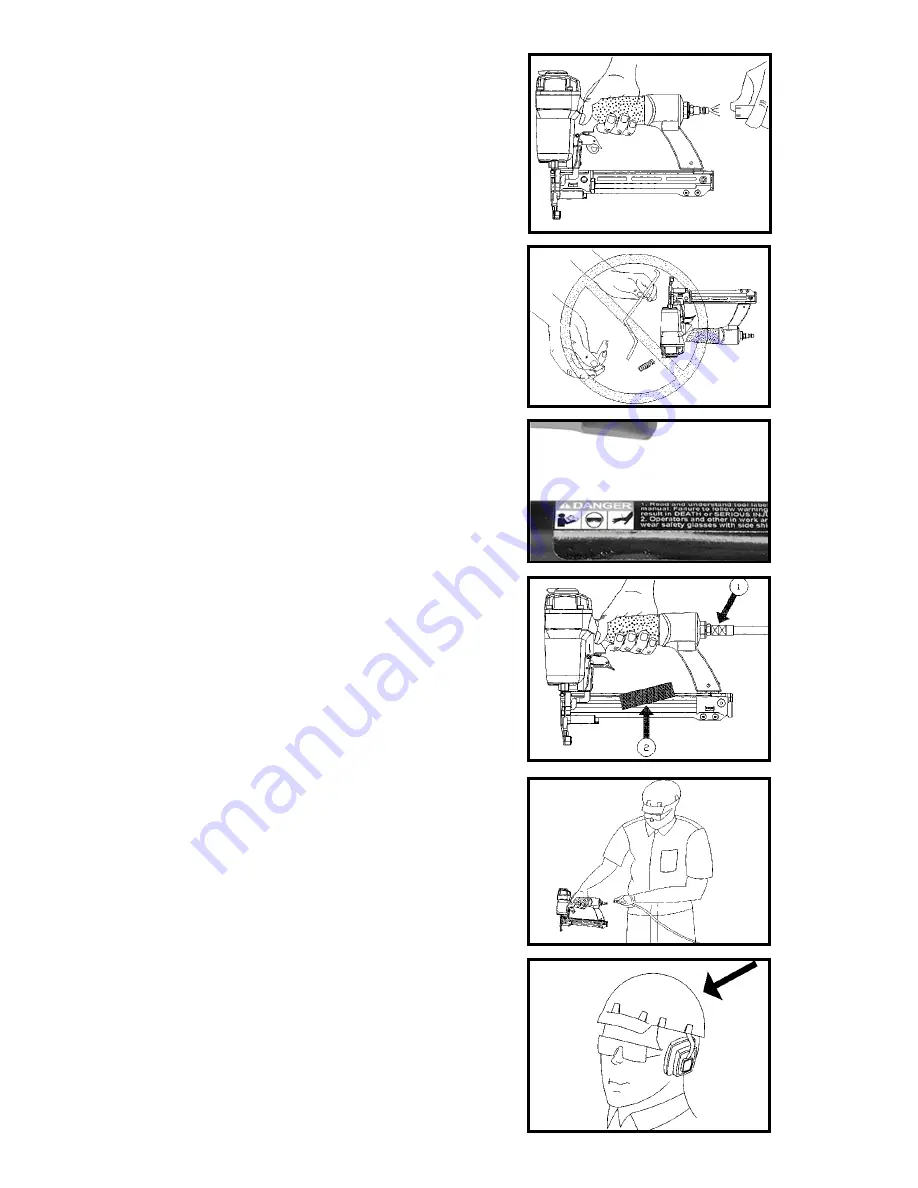
5
9.
Do not connect tool
to pressure which
potentially exceeds 200 PSI (13.7 BAR).
10. All air line components (hoses,
connectors, filters, regulators, etc.)
must
be rated for a maximum working pressure
of at least 150 PSI (10.3 BAR) or 150% of
the maximum system pressure, which ever
is greater.
11. Connect tool to air supply hose
with a
coupling that automatically removes all
pressure from the tool when the coupling is
disconnected. Fig. 7.
12. Disconnect tool from air supply hose
before doing tool maintenance, clearing a
jammed fastener, leaving work area, moving
tool to another location, or handing the tool
to another person. Fig. 7.
13. Never use a tool
that is leaking air, has
missing or damaged parts, or requires
repair. Make sure all screws and caps are
securely tightened. Fig. 8.
14. Never use tool if safety, trigger or
springs
are inoperable, missing or
damaged. Do not alter or remove safety,
trigger, or springs. Make daily inspections
for free movement of trigger and safety
mechanism. Fig. 8.
15. Do not use tool without safety
warning label.
If label is missing, damaged
or unreadable, contact the Customer Care
Department at 1-800-888-2468 for a
replacement. Fig. 9.
16. Only use parts and accessories
approved by DeVilbiss Air Power Company.
17. Connect tool to air supply before
loading fasteners, to prevent a fastener
from being fired during connection. The tool
driving mechanism may cycle when tool is
connected to the air supply. Fig. 10.
18. Always assume the tool contains
fasteners.
No horseplay. Respect the tool
as a working implement. Fig. 11.
19. Operator and bystanders should wear
hard hats
to safeguard against possible
injuries. Fig. 12.
20. Keep bystanders and children away
from work area
when operating this power
tool.
Fig. 8
Fig. 9
Fig. 11
Fig. 12
Fig. 7
Fig. 10