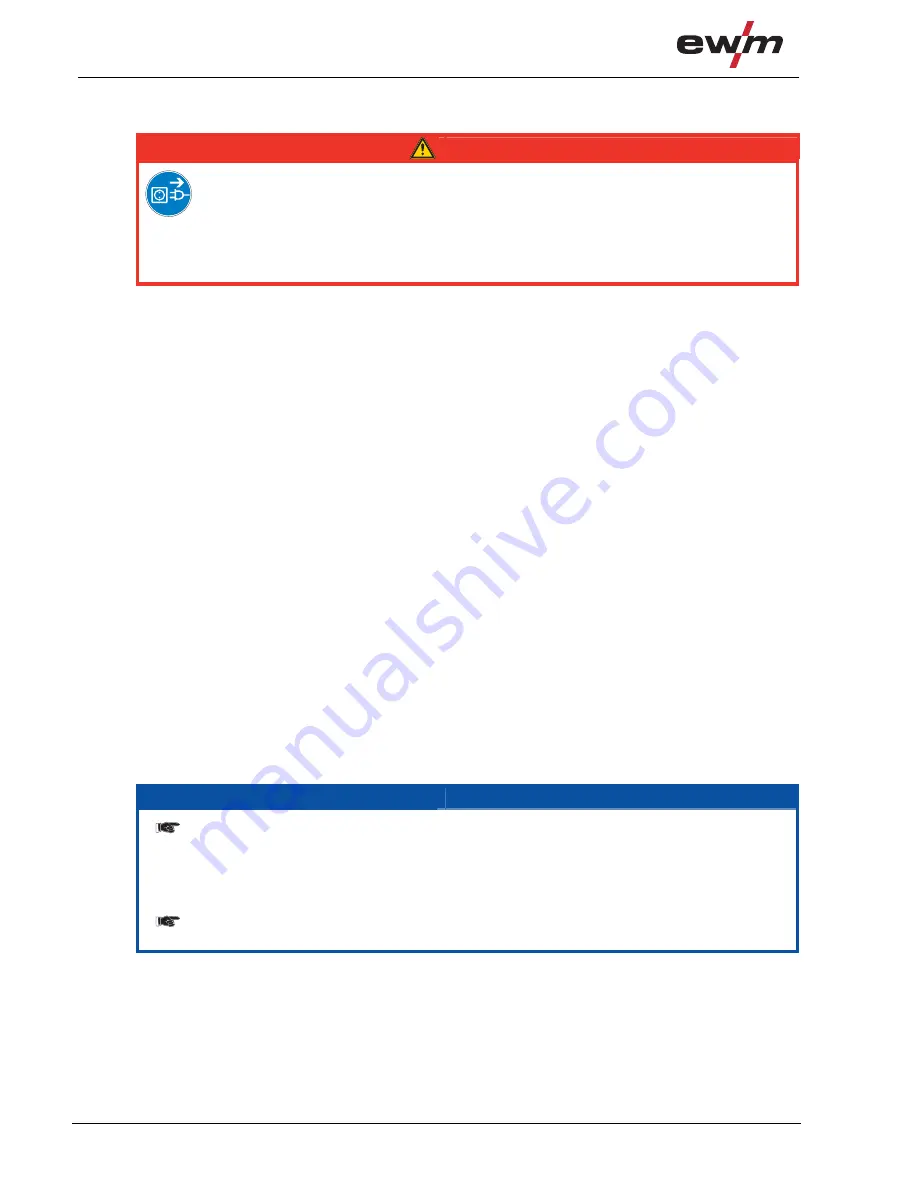
Maintenance, care and disposal
General
68
099-000097-EW501
14.03.2012
6
Maintenance, care and disposal
DANGER
Risk of injury from electric shock!
Cleaning machines that are not disconnected from the mains can lead to serious
injuries!
• Disconnect the machine completely from the mains.
• Remove the mains plug!
• Wait for 4 minutes until the capacitors have discharged!
6.1
General
When used in the specified environmental conditions and under normal operating conditions, this
machine is largely maintenance-free and requires a minimum of care.
There are some points, which should be observed, to guarantee fault-free operation of your welding
machine. Among these are regular cleaning and checking as described below, depending on the pollution
level of the environment and the length of time the unit is in use.
6.2
Maintenance work, intervals
6.2.1
Daily maintenance tasks
6.2.1.1
Visual inspection
• Mains supply lead and its strain relief
• Gas tubes and their switching equipment (solenoid valve)
• Other, general condition
6.2.1.2
Functional test
• Welding current cables (check that they are fitted correctly and secured)
• Gas cylinder securing elements
• Operating, message, safety and adjustment devices (Functional test)
6.2.2
Monthly maintenance tasks
6.2.2.1
Visual inspection
• Casing damage (front, rear and side walls)
• Transport elements (strap, lifting lugs, handle)
6.2.2.2
Functional test
• Selector switches, command devices, emergency stop devices, voltage reducing devices, message
and control lamps
6.2.3
Annual test (inspection and testing during operation)
NOTE
The welding machine may only be tested by competent, capable personsl.
A capable person is one who, because of his training, knowledge and experience, is
able to recognise the dangers that can occur while testing welding power sources as
well as possible subsequent damage and who is able to implement the required safety
procedures.
For further information, please see the accompanying supplementary sheets "Machine
and Company Data, Maintenance and Testing, Warranty"!
A periodic test according to IEC 60974-4 "Periodic inspection and test" has to be carried out. In addition
to the regulations on testing given here, the relevant local laws and regulations must also be observed.