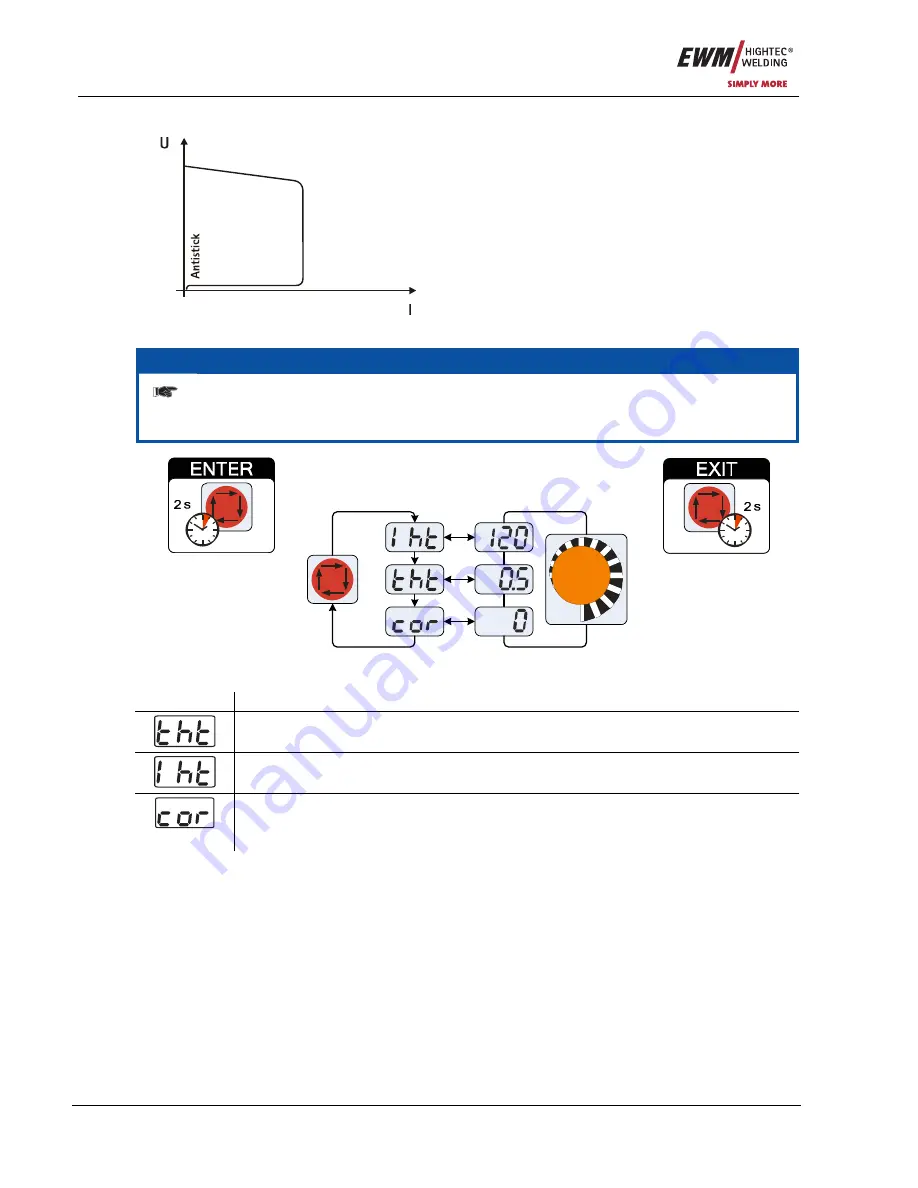
Functional characteristics
MMA welding
32
Item No.: 099-002046-EWM01
5.2.4
Antistick
Anti-stick prevents the electrode from annealing.
If the electrode sticks in spite of the Arcforce device, the
machine automatically switches over to the minimum
current within about 1 second to prevent the electrode
from overheating. Check the welding current setting
and correct according to the welding task!
5.2.5
Advanced settings
NOTE
To change the advanced setting parameters, hold down the "Welding parameters" button
for 2 seconds after selecting the welding process.
The following diagram shows the setting options.
Figure 5-9
Display Setting/selection
Hotstart time
Hotstart time setting (0,1 s to 20,0 s)
Hotstart current
Hotstart current setting (50 % to 200 %)
Arcforce correction (setting -10 to 10, factory setting 0)
• Increase value > harder arc
• Decrease value > softer arc