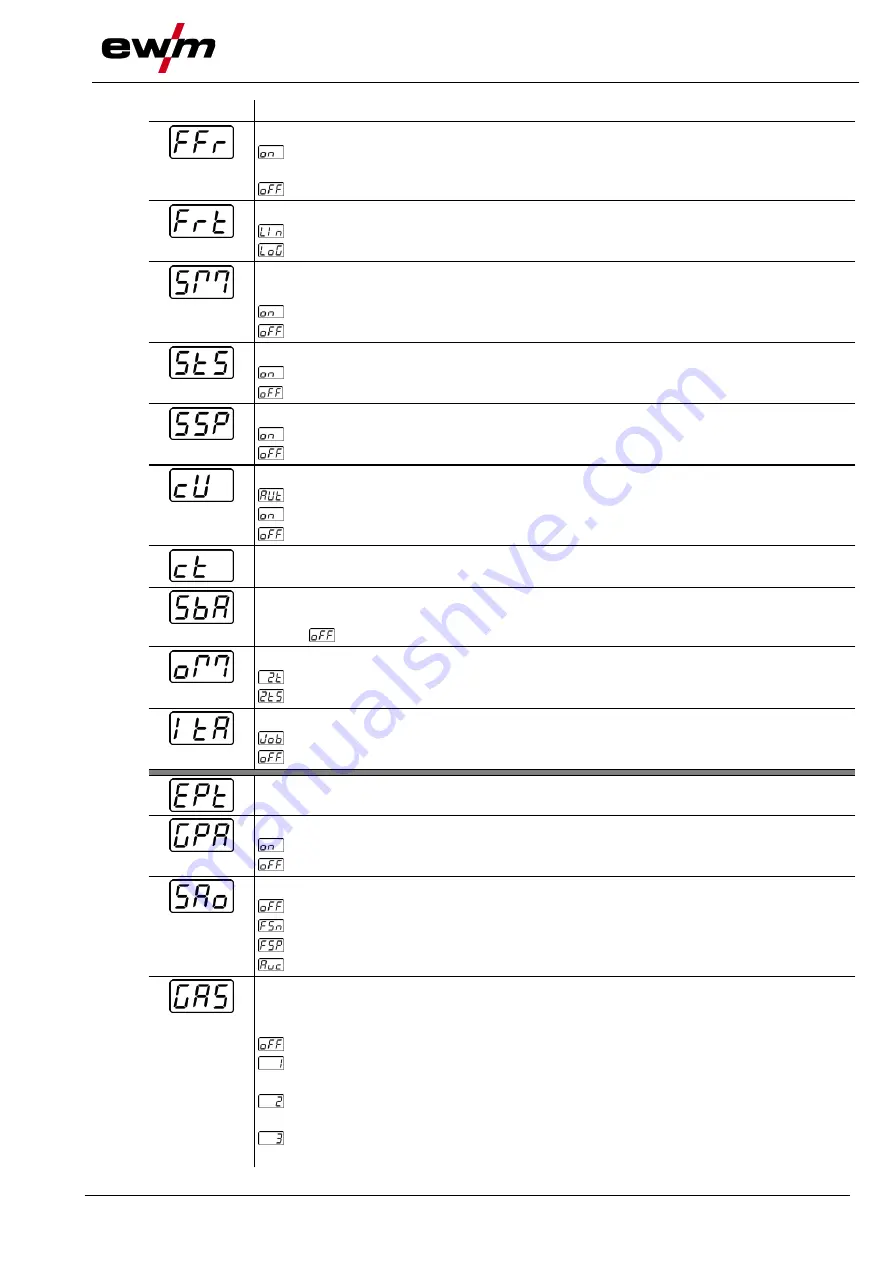
Design and function
Machine configuration menu
099-007033-EW501
4.1.2022
53
Display
Setting/selection
RTF start ramp
-------Welding current rises to the specified main current level in a ramp function (ex
works)
-------Welding current immediately jumps to the specified main current level
RTF response
-------Linear response
-------Logarithmic responsive (ex works)
spotmatic operating mode
Ignition by contact with the workpiece
-------Function enabled (ex works)
-------Function disabled
Spot time setting
-------Short spot time, setting range 5 ms to 999 ms, increments of 1 ms (ex works)
-------Long spot time, setting range 0.01 s to 20.0 s, increments of 10 ms (ex works)
Process activation setting
-------Separate process activation (ex works)
-------Permanent process activation
Torch cooling mode
-------Automatic operation (ex works)
-------Permanently enabled
-------Permanently disabled
Welding torch cooling, post-flow time
Setting 1–60 min. (ex works 5 min.)
Time-based power-saving mode
> see 5.5 chapter
Time to activation of the power-saving mode in case of inactivity.
Setting
= disabled or numerical value 5-60 min..
Operating mode switching via interface for automated welding
------Non-latched
-------Special non-latched
Re-ignition after arc interruption
> see 5.3.2.3 chapter
-------JOB-dependent time (ex works 5 s).
-------Function disabled or numerical value 0.1–5.0 s.
Expert menu
Automatic gas post-flow function
> see 5.1.7.4 chapter
-------Function on
-------Function off (factory setting)
Error output to interface for automated welding, contact SYN_A
-------AC synchronisation or hot wire (ex works)
-------Error signal, negative logic
-------Error signal, positive logic
-------AVC (Arc voltage control) connection
Gas monitoring
Depending on where the gas sensor is situated, the use of a pilot static tube and the
welding process monitoring phase.
-------Function disabled (ex works).
-------Monitoring during the welding process. Gas sensor between gas valve and
welding torch (with pilot static tube).
-------Monitoring prior to the welding process. Gas sensor between gas valve and
welding torch (without pilot static tube).
-------Permanent monitoring Gas sensor between gas cylinder and gas valve (with
pilot static tube).