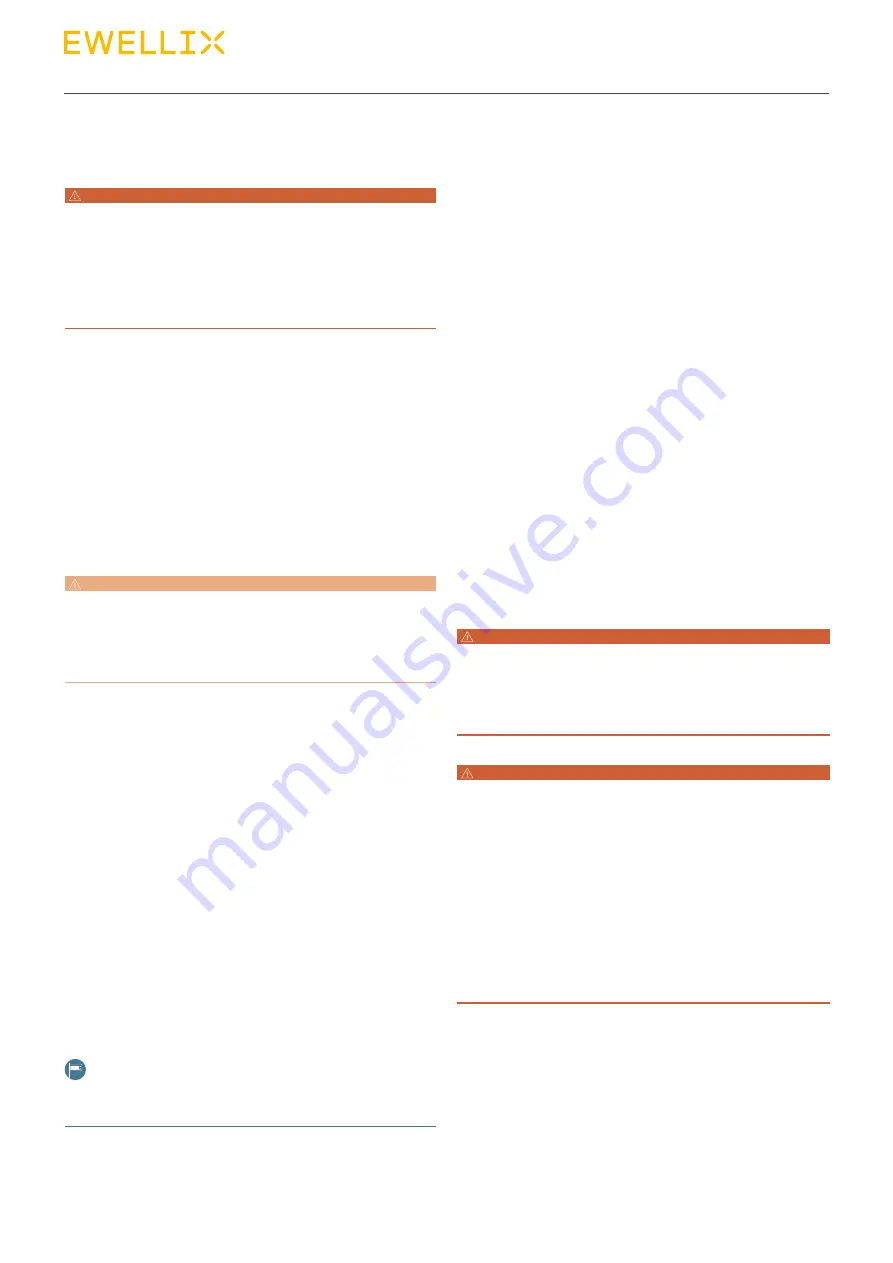
20
CPMT
6.3 Installation
• To be performed by qualified personnel.
WARNING
Risk of injury and device damage due to manipulation of the
screws on the device
Manipulation or loosening of the screws on the device or the optional
devices may lead to injury and device damage during the operation.
Therefore:
• Never loosen screws on the device or the options, except the
transportation screws installed in the mounting bores.
6.3.1 Installation overview
The telescopic pillar CPMT can be mounted to the application
via the Ewellix mounting plates available as accessory, or di-
rectly to the application. Mounting has to be done via the at-
tachment bores on the outer and inner tube, which are acces-
sible through the top and base plates (⮑ fig. 1, page 12).
Screw
8 × M10
Screw-in depth
25 to 35 mm in the pillar
Strength class
10,9
Tightening torque
40 Nm
CAUTION
The outer and inner tube base plates are not designed to
support the rated load of the pillar without additional support
provided by mounting plates. If a custom mounting plate is used,
ensure that it is dimensioned to provide sufficient support of the
base plates.
The telescopic pillar CPMT can be mounted with the outer tube
or the inner tube at the bottom. If the inner tube is fixed and the
outer tube is able to move in the application, ensure that there
is no possibility of strain or pinching of the power cable.
Any subsequent fastening bores in the aluminium tubes may
be made only by Ewellix.
Care must be taken not to damage or scratch the sides of
the tubes, as this can damage the guiding system and lead
to product malfunctions.
6.3.2 Installation steps
1. Remove the transportation screws from the mounting
bores at the outer and inner tube base plates.
2. Fasten the mounting plates, or the attachment points in
the application, to the mounting bores at the outer and
inner tube base plates.
Important: Screw in to a minimum of 25 mm and torque the
screws with 40 Nm.
NOTE
Fastening screws are not supplied. The bore dimensions can be
found in ⮑ Plans and diagrams, page 32.
3. Check that all screws are sufficiently secured against
self-loosening.
4. Check that all interfaces and connections have been
mounted and/or connected correctly.
5. Ensure that the motor cable cannot be crushed, jammed
or pulled during operation, due to tension or pressure.
6. You are now ready to connect and operate the telescopic
pillar using the corresponding control unit and operating
device.
Before connecting the telescopic pillar CPMT to a control
unit, ensure that:
• the telescopic pillar CPMT is attached to the metal plates
of the application on both sides
• all attachment points are securely screwed to the application
• the elements are fully aligned and seated at the top and
bottom
• the areas for force distribution are supported
• the acting force does not impact the guide tubes with inad-
missibly high values, as side-impacting forces that are too
high can destroy the telescopic pillar CPMT
• the telescopic pillar is not obstructed in any way in the en-
tire lifting area
• the cables are not pinched, or caught or subject to tension,
bending, or pull stress.
WARNING
Risk of injury and device damage due to insufficient
fastening
Use fastening bolts only, and secure them adequately. Do not
use screws to install. Never loosen or otherwise manipulate
screws on the device or options.
WARNING
Risk of injury through moving parts
When retracting, there is a risk of crushing between the mounting
plate and the tube end of the telescopic pillar.
Therefore:
• When retracting, ensure that no objects or parts of the body, such as
hands or fingers, can be caught between the mounting plate (2) of
the inner tube and the ends of the outer tubes (1) (⮑ fig. 1, page 12).
• If necessary, install a mechanical safety device depending on the
installation location.
• If the device has been delivered with optional fastening bores, en-
sure that the intended parts have been correctly fitted to these
bores and that the bores are not accessible to any objects or
parts of the body.
Ensure that the telescopic pillar CPMT is not obstructed in
its movement over the entire stroke area. Consider perform-
ing collision tests on the application.