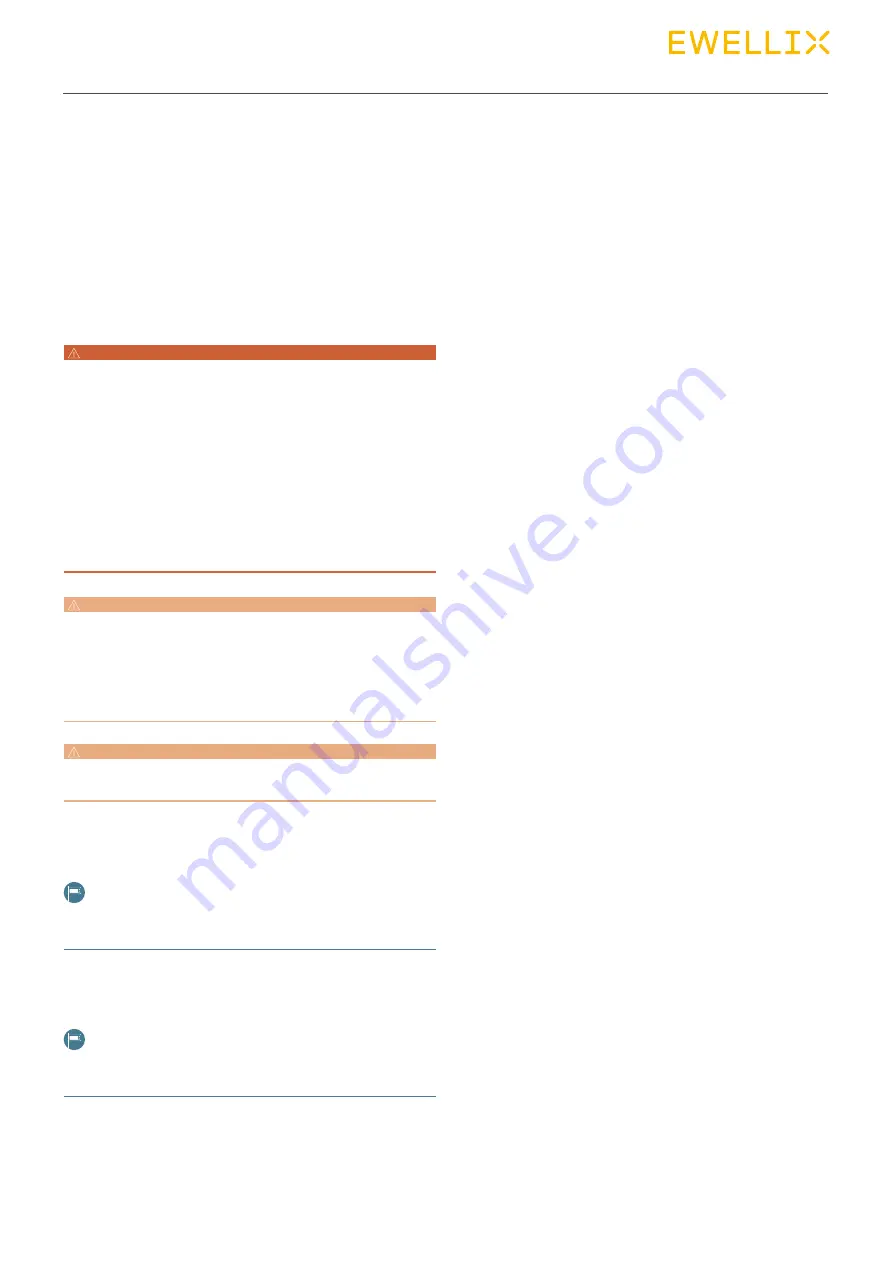
23
7.0 O p eration
7.1 Safety
WARNING
Risk of crush hazard
While the device is in motion, there is a risk of crushing, which
may result in injury to persons or damage to objects.
Therefore:
• Ensure that no persons are in the stroke area of the device while
in operation.
• Make sure the device is always operated within permissible spec-
ifications.
• Immediately take the device out of service if there are any unusual
noises or changes in operation.
• Never tamper with the elements connected to the device while the
device is in operation.
CAUTION
Device damage due to static and dynamic overload of the device
Static and dynamic overload can lead to damage and failure of
the device.
Therefore:
• Do not exceed maximum permissible performance specifications
for the device (⮑ Data sheets in the Appendix, page 31).
CAUTION
Telescopic pillar may be damaged if liquids penetrate the device
during extension and retraction. Keep liquids away.
7.2 Turn on
NOTE
The device does not have its own operating elements. Operation
is via a separate control unit (⮑ Separate operating manual).
7.3 Turn off
NOTE
The device does not have its own operating elements. Operation
is via a separate control unit (⮑ Separate operating manual).
7.0 Operation
7.4 Actions before use
Perform an installation check before starting up the tele-
scopic pillar CPMT for the first time.
Installation check:
• All instructions from the above sections on ‘Operation’
have been followed.
• No impermissibly high side-acting forces impacting on the
guide tubes.
• Fastening screws secured tightly on mounting bores at in-
ner and outer tube base plates
• Entire stroke area unobstructed, so that the telescopic pil-
lar CPMT cannot be driven into a fixed object.
• All cables secured against pinching and trapping, and
properly connected.
• If connected with a flying leads cable, the leads are
connected in accordance with the wiring diagram in the
appendix.
• Electrical supply secured and the telescopic pillar CPMT
securely connected to a control unit.
• Operating device connected to the control unit.