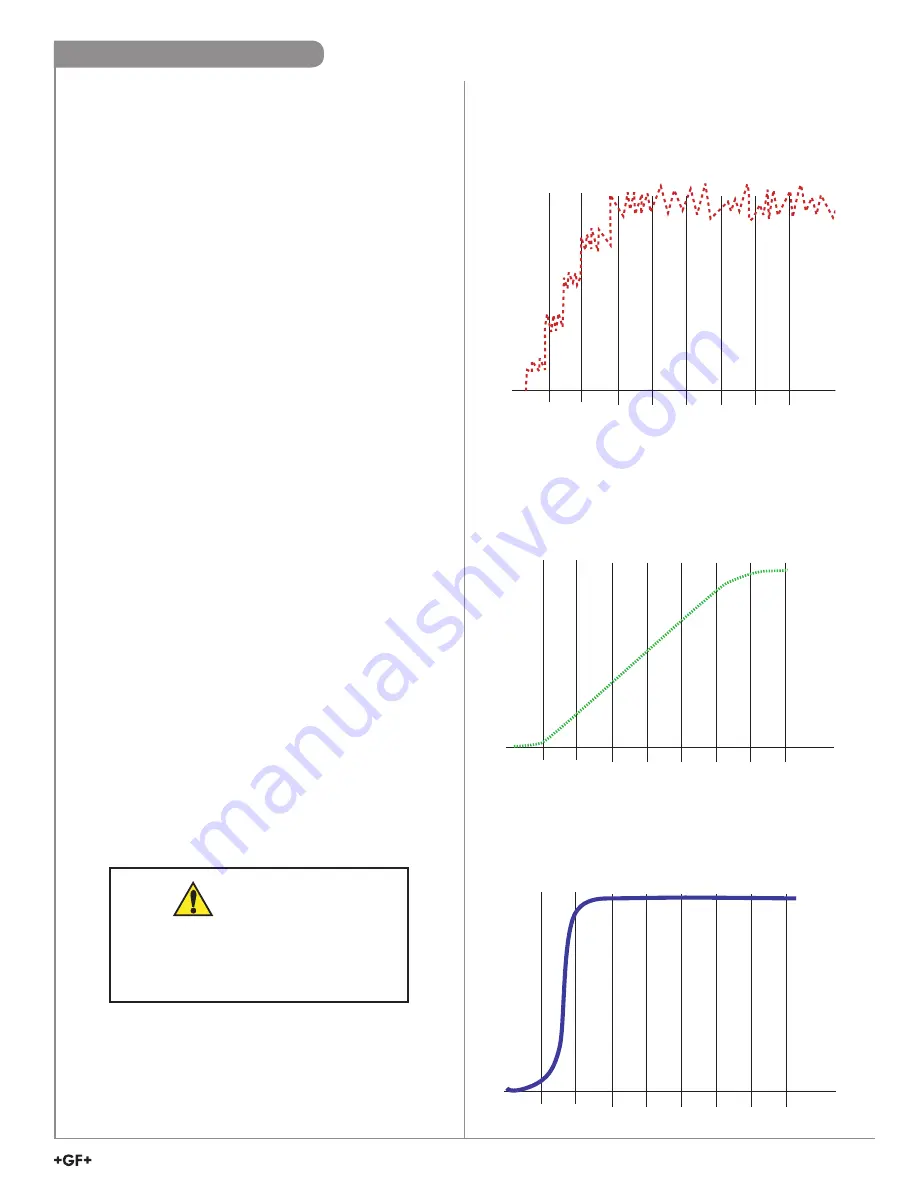
9
2551 Blind Magmeter
Sensitivity
• The SENSITIVITY setting determines how the 2551
responds to sudden surges in the fl ow rate. It "overrides"
the Averaging function just long enough to allow an actual
change in fl ow rate to be displayed, then resumes the
averaging. The result is a smooth fl ow display and a quick
response to large shifts in the fl ow rate.
• The settings for Sensitivity represent a percentage of the
magmeter's maximum range, or 10 meters per second (m/s).
• Example: A sensitivity setting of 25% means that the fl ow
rate must change instantly and by more than 2.5 ms before
the function is enabled.
NOTE:
The SENSITIVITY function is ineff ective if the
AVERAGING function is set to zero.
Averaging
• The AVERAGING setting dictates the time over which the
magmeter will average the fl ow signal.
• The LCD display is updated every second. With averaging
at 14 seconds, the fl ow rate on the display is an average of
the previous 14 seconds input.
• Short averaging times provide the fastest display and output
response to changes in the fl ow rate.
• Higher averaging times help to smooth the display and
current output where the fl ow in the pipe is erratic or
unstable due to installation limitations.
No Averaging
With AVERAGING set to zero, the fl ow rate will be displayed
immediately and with no fi ltering. This line represents the
actual output of the fl ow sensor as it responds to unstable fl ow
conditions in the pipe.
10 s
20 s
30 s
40 s
50 s
60 s
70 s
Time
Ve
locity
Averaging Only
With AVERAGING set to 50 seconds and SENSITIVITY still
set to zero the fl ow rate is stabilized, but a sharp change in
fl ow rate is not represented on the display or at the output for
50 seconds or longer.
10 s
20 s
30 s
40 s
50 s
60 s
70 s
Time
Ve
locity
Averaging and Sensitivity
With AVERAGING at 50 seconds and SENSITIVITY set to
25%, the fl ow rate is stabilized, while the sudden shift in fl ow
is refl ected very quickly.
10 s
20 s
30 s
40 s
50 s
60 s
70 s
Time
Ve
locity
Even the most carefully engineered fl ow systems may
experience erratic and unstable conditions. If the instability is
communicated to the output functions, the results may create
problems for control devices.
To alleviate these issues, the 2551 provides two adjustments
that operate in tandem. The information here will help
in determining the appropriate settings for any specifi c
application.
Averaging and Sensitivity
The SENSITIVITY function changes the
response characteristics of the magmeter.
If used as part of a tuned closed loop control
system, such a change may be undesirable.
CAUTION