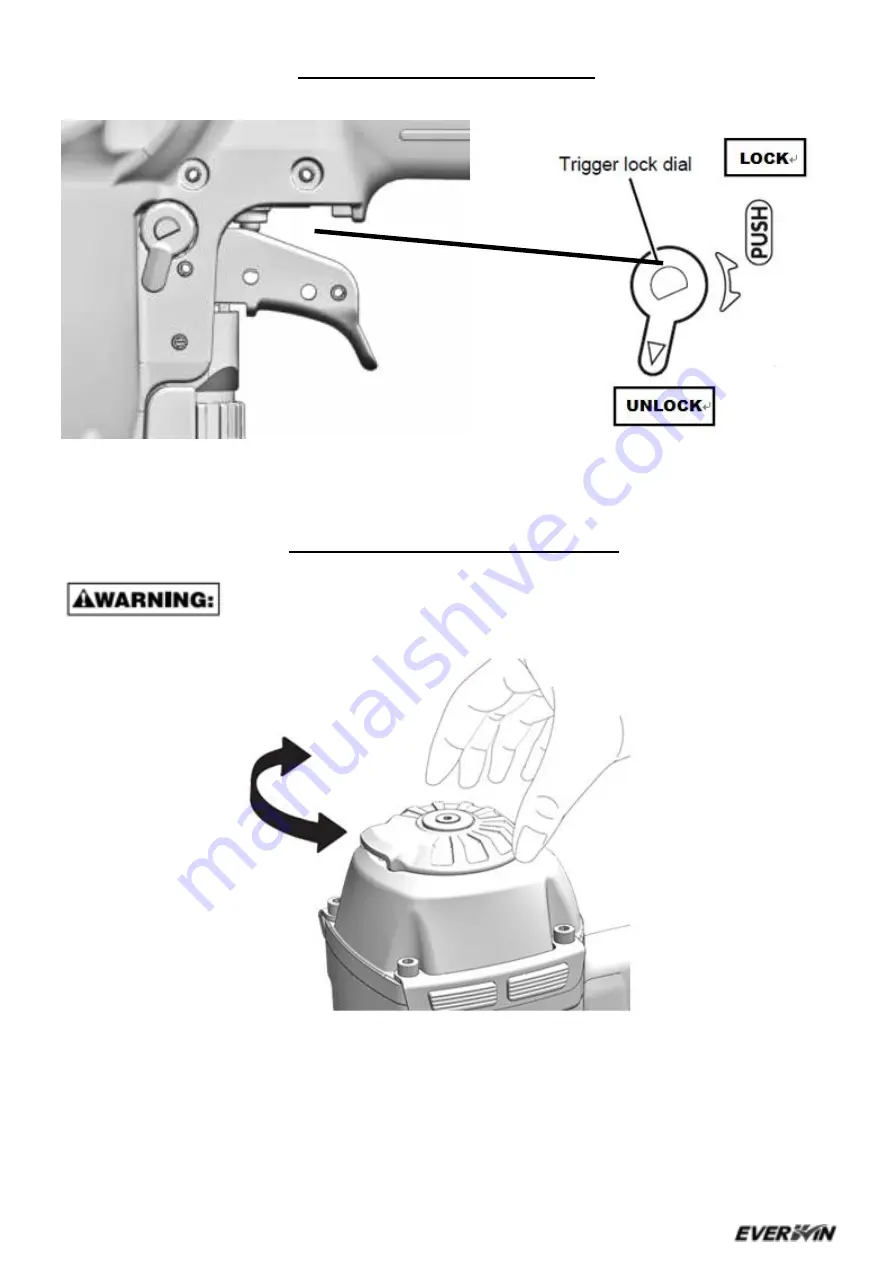
12
TRIGGER LOCK MECHANISM
The tool is equipped with a Trigger Lock mechanism. Push and rotate the Trigger Lock Dial to the trigger free
position before driving nails.
DIRECTIONAL EXHAUST COVER
ALWAYS disconnect air supply before rotating the exhaust cover by
hand.
Direction of the
exhaust air is changed by
rotating exhaust
cover by hand,