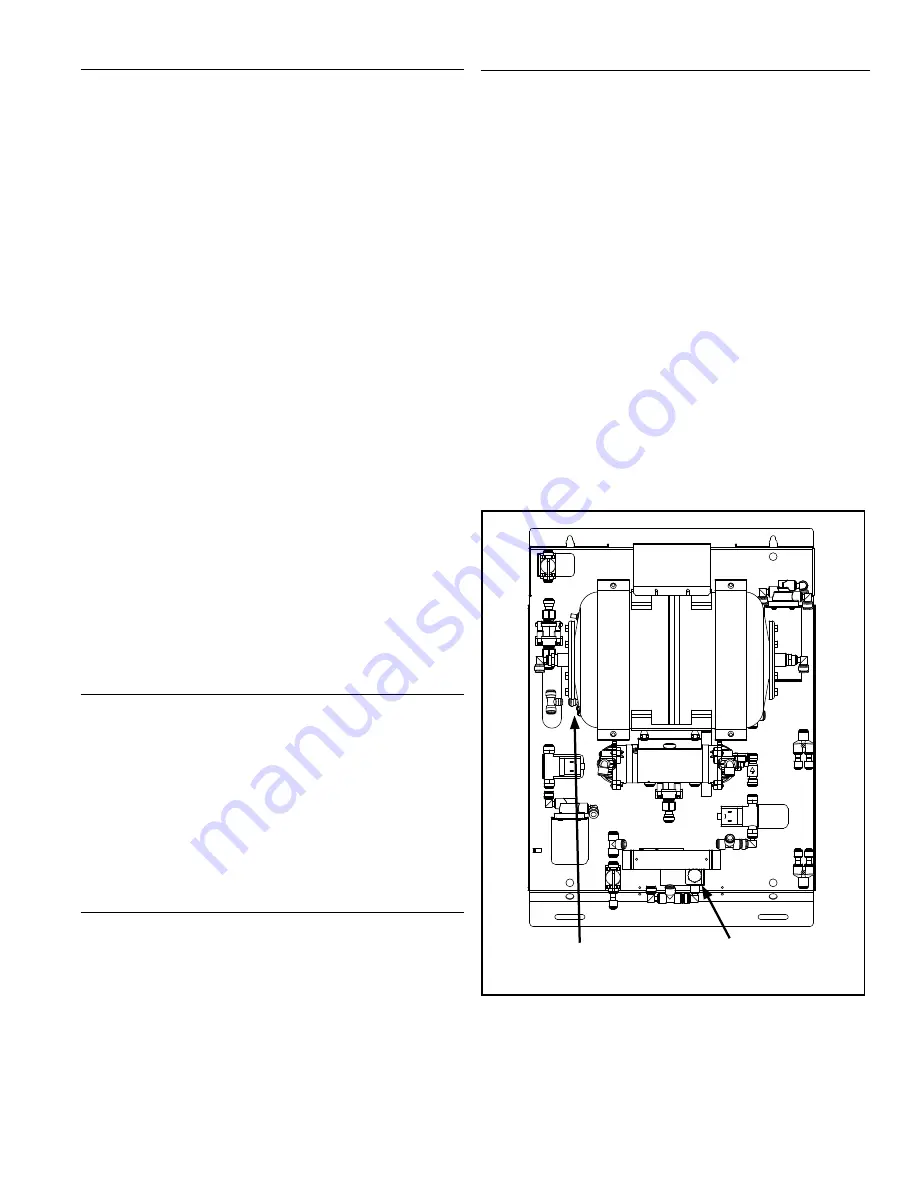
7
dISInfectIon
When cartridge activation and recovery adjustments are complete,
the storage tank and associated piping must be disinfected, then
completely flushed. The steps for this are outlined below.
Locate the 3/8" OD tubing that connects to the inlet (left side)
1.
of the storage tank. Disconnect the end which connects to the
elbow fitting at the processor. Measure 1 ounce of 5.25% bleach
for every 7.5 gallons of storage tank capacity. Pour this volume of
bleach into the tube that leads to the storage tank. Re-connect
this tube to the elbow fitting. Apply power to the system by
plugging the power cord into the receptacle. The booster pump
should begin to run and fill the storage tank.
Once sufficient water has entered the storage tank (more
2.
than 1/4 full), demand treated water from at least one piece of
equipment the ENVI-RO is supplying water to. Once all of the
air has been purged, and a solid flow of water is observed, stop
the flow at the connected equipment. Purge the air from all
remaining pieces of connected equipment by demanding water
from each one individually.
Allow the storage tank to fill until the booster pump turns off.
3.
Allow the chlorinated water to remain in the storage tank and
distribution piping for 10 minutes.
Unplug the power cord. Drain the storage tank by demanding
4.
water downstream and allow the storage tank to drain. Once the
storage tank is empty, stop demanding water downstream.
Apply power to the system by plugging the power cord into the
5.
receptacle. Once sufficient water has entered the storage tank
(more than 1/4 full), demand treated water from at least one piece
of equipment the ENVI-RO is supplying water to. After 5 minutes,
stop the flow at the connected equipment. Flush the lines to each
remaining piece of connected equipment by demanding water
from them for 2 minutes each.
Allow the storage tank to fill until the booster pumps turns off.
6.
Unplug the power cord. Drain the storage tank by demanding
7.
water downstream and allow the storage tank to drain. Once the
storage tank is empty, stop demanding water downstream
Repeat steps 5-7 until no residual chlorine odor is detected from
8.
the water exiting the storage tank or connected equipment.
PlacIng enVI-ro Into SerVIce
Once the cartridges have been activated, the storage tank and
distribution piping sanitized, the ENVI-RO can be placed into service.
During normal operation, the valves on the ENVI-RO should be in the
following positions:
System inlet and outlet valves – open
A.
System by-pass valves – closed.
B.
Once the system been started-up initially, it is a good idea to
measure the outlet water flow rate and quality to verify the system’s
performance. The initial values should be recorded for future
comparison to detect any changes in performance. A Performance
Log has been provided on Page 9 to record this information.
oPeratIon
During normal operation, a continuous supply of water must be
1.
available to the system.
The system inlet and outlet valves must be open, the sample
2.
outlet and flushing valves must be closed and the drain line must
be unrestricted.
dual outlet and blend adjuStment
The ENVI-RO system is capable of producing two water qualities,
which are detailed below.
The outlet marked “STEAMER” provides water directly from the
•
RO Membrane. The TDS of this water is very low, ideally suited
for applications such as flash steamers and other equipment that
“boils away” the water. This outlet requires no adjustment.
The outlet marked “COFFEE” can produce a wide range of water
•
qualities. It combines or “blends” two sources of water; 1)
directly from the RO Membrane and, 2) filtered water containing
the same level on mineral content as the raw (feed) water. The
following text describes the adjustment of this feature.
Open the feedwater blend valve (FBV) and dilution blend
1.
valve (DBV) fully. See
figure 6
for location of these valves.
Demand flow on the “COFFEE” line. The flowrate should
2.
equal the maximum expected demand of all connected
equipment.
Access the “Coffee TDS” view screen on the controller to
3.
observe a real-time reading of the TDS quantity in the water
flowing to the “COFFEE” line.
Compare TDS value on controller to application requirement.
4.
If controller reading is higher than requirement, slowly close
FBV until TDS value is met. If controller reading is lower than
requirement, slowly close DBV until TDS value is met.
figure 6.
RO Blend Valve Locations
Feedwater Blend
Valve (FBV)
Dilution Blend
Valve (DBV)