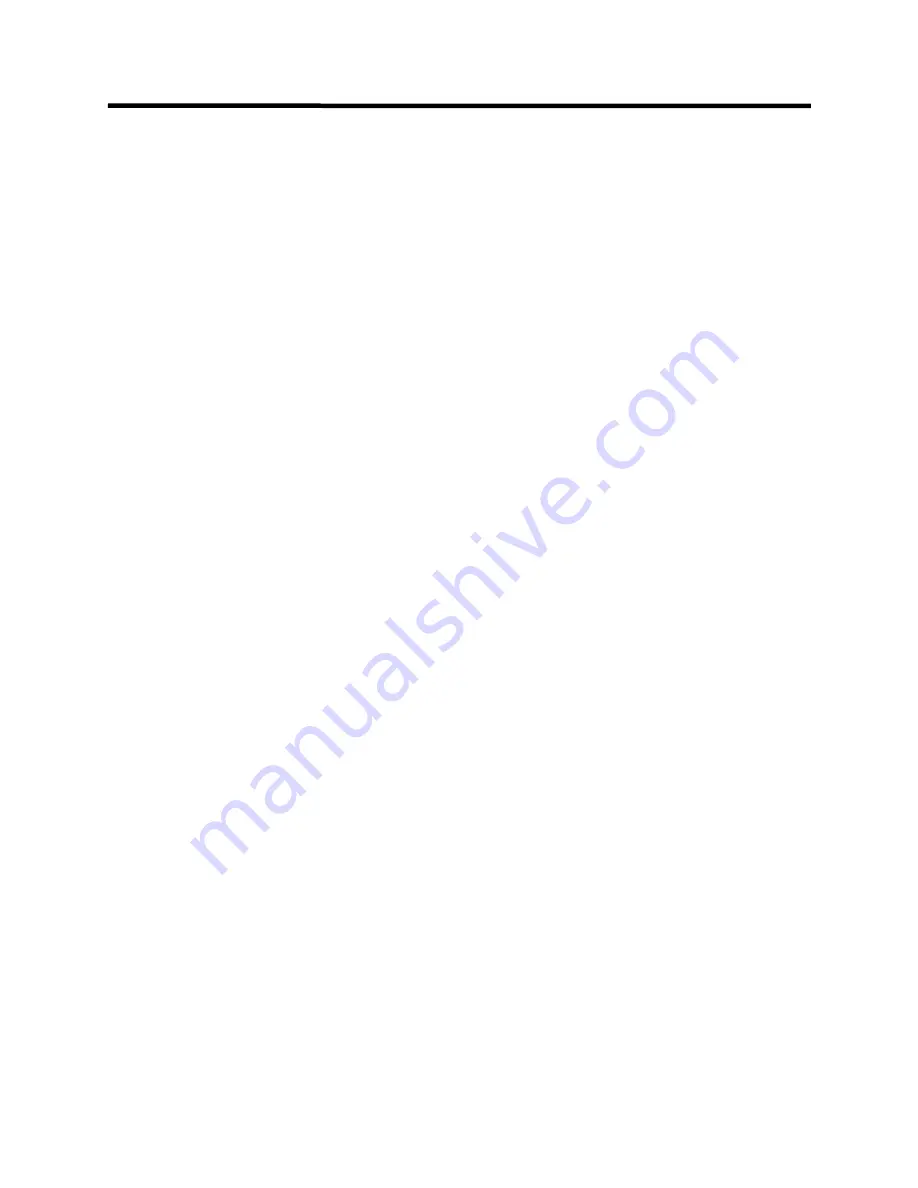
43
MIG OPERATION
or pull the MIG gun. Stringer beads are often best
for novice welders. Stringers are simply straight
beads that move forward with little or no side to
side travel or oscillation. These will offer the sound-
est welds for a beginner. Stringer welds leave little
or no room for contaminates to enter the weld and
are the fastest to produce without creating an op-
portunity for cold lap. Moving too quickly however
with a stringer can create undercut which will weak-
en the weld. The best policy is to move a slow
steady speed, making sure the sides of the weld are
filled. If undercut is present, it is either from too
much voltage or moving before the wire has time to
fill the area the arc has melted.
Think of weaving as a method of
“
sewing
”
the metal
together. If weaving is of interest to you, start with
the basic weave pattern. Simple weaves using one
variation or the other of a cursive
“
e
”
motion are
best to begin with. Other weave patterns can be
used of course. C
’
s, V
’
S, U
’
s , Triangles and many
more weave patterns can be used depending upon
the application. Weaves are employed for a number
of reasons. Weaves are often considered to have a
more pleasing appearance and can help bridge gaps
where fit up is a problem. A weave is also frequently
used to manage heat build up. For example: when
welding vertically weaves are almost always used to
prevent the molten metal from sagging due to the
force of gravity. The major drawback of weaving is
that it introduces a greater possibility of getting in-
clusions and other forms of contamination in the
weld. Properly done weaving is a valuable tool, but
it must be practiced before employing it in any struc-
tural or critical application.
Metal Cleaning.
MIG welding requires a well prepped surface to ob-
tain a sound weld. The removal of paint, rust mill
scale, or other contaminate such as grease should be
done before welding. Stick welding is more forgiving
of rust and mill scale, but when MIG welding, con-
taminates will result in porosity and inclusions in the
weld, weakening it. A grinder will usually prep the
metal sufficiently to remove oxidation and paint.
However, to remove grease a degreaser such as ace-
tone should be used. Do not use any degreaser such
a brake cleaner with chlorinated solvents or death or
serious injury may occur!
A MIG wire such as ER70S
-
6 or ER70S
-
2 includes a
sufficient level of deoxidizers such as silicone and
copper that are formulated to allow it to handle mi-
nor to moderate amounts of rust and mill scale.
These deoxidizers will float out most moderate
amounts of contaminates out of the weld and will
appear in the usual form of glassy like deposits on
top of the cooled metal. They are easily brushed off
before starting the next pass. They should not be
welded over. Any pinholes that appear are a result
of trapped gas in the weld and should be ground out
before the next pass. It should be noted that some
MIG wires such as ER70S
-
3 have low levels of deoxi-
dizers and must be thoroughly cleaned and ground
before welding.
Multiple Pass Welds.
One of the common misunderstandings that people
have when beginning to MIG weld is that if the
welder has the power, then a single heavy pass will
do to weld up in a single pass. This is a primary way
to introduce cold lap and incomplete fusion to the
weld. Single pass welds should not exceed
1/4”
even with the heaviest wire the welder is capable of
handling. A thick pass may also begin to cool before
contaminates and gas pockets have the time to float
out to the surface. It
’
s far better to make multiple
smaller passes to complete a plate weld for a higher
quality result. For best results, this requires that
most joints
1/4”
and over be prepared with a grinder
to accept multiple weld passes. The weldment edg-
es should be ground to form a V, U or J shaped
groove to create a recess where the welds can be
welded one on top of another. For welding
with
.035”
wire and under, create a bead no thicker
than
3/16”
in a single pass, no more than
1/8”
with
.030”
wire, and with
.025”
wire and smaller no
more than 3/32 for best results. This will help main-
tain proper fluidity of the weld and prevent gas from
being trapped in the weld and give time for any mi-
nor contaminates to float out of the weld. It will
also help to maintain reasonable forward travel
speeds. Too slow of travel speeds will create excess
build up and can tend to create cold lap at the weld
toes resulting in poor tie in. One issue created with
a weaving technique even if the metal deposited is
the correct thickness s that it can slow the forward
progress down. If weaving is too wide, one side of
the puddle will cool and oxidize before the torch is
brought back across to that side. This is a point
Basic Theory and Function
Section 3