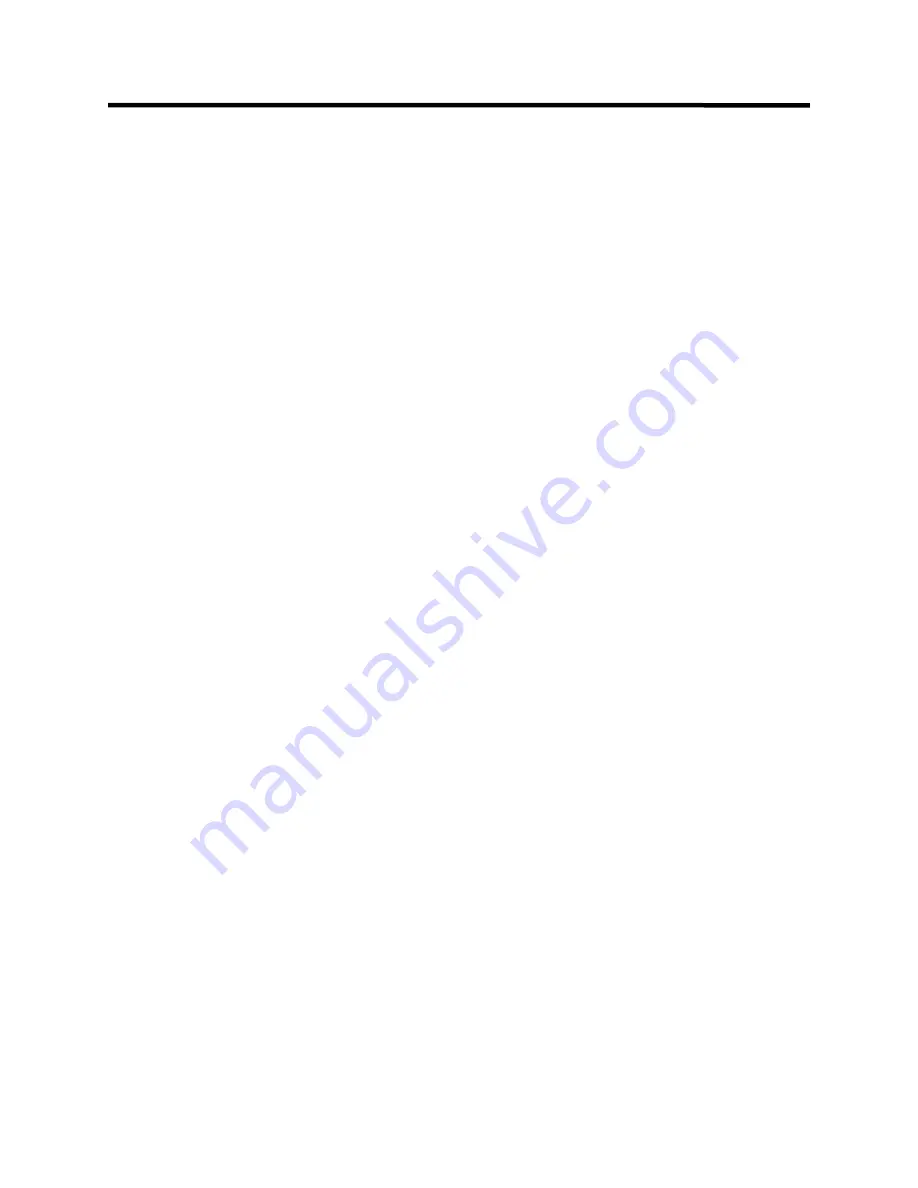
12
related to 2T/4T torch switch or foot pedal opera-
tion. The unit is ready to TIG weld (with the excep-
tion of Tungsten and shielding gas) when it arrives.
Additional TIG consumable kits can be purchased
from Everlast which include stubby consumables or
gas lens kits with Tungsten in the kit.
Attention!
Be sure to read all the connection directions locat-
ed in this manual and important information re-
garding proper connections of torch and work ca-
ble in TIG mode or damage or improper operation
may occur.
3)
SMAW
(Stick).
In stick mode the welder delivers a
smooth DC low spatter arc. Professional, high
-
quality welds are obtainable with E7018, 7014,
309L, 316L, 6011 and many other similar rods that
are designed for use with any DC stick welder. This
unit is optimized for welding E6010. This setting
also works well with the easier
-
welding E6011. The
Stick mode also features adjustable hot start time
and hot start intensity controls which are designed
to help reduce sticking during arc starts while sim-
ultaneously reducing porosity or inclusions during
arc initiation.
Note: This unit does not provide AC
operation in stick mode. AC operation is for TIG
only.
4)
Stick Arc Force Control.
The arc force control ad-
justs the quality and feel of the welding arc. It does
so by modifying the volt/amp curve. As the voltage
drops below approximately 20 volts when the arc
gap (length) is shortened, the unit reacts by auto-
matically boosting the amps over the original Amp
setting. This helps to prevent the rod from sticking
and helps keep the arc going as arc voltage falls.
This action also boots penetration and can be used
to change the way the arc feels and acts.
5)
Burn Back Control.
Burn back control is used to
control the length of the wire stick
-
out after the
trigger is released. It helps to prevent the welding
wire from sticking in the coalescing weld puddle
after the arc is terminated and saves the user from
having to trim the wire before restarting the arc.
6)
Synergic MIG Mode.
Synergic mode may be en-
gaged to simplify welder setup and adjustment.
This mode will allow the customer to input basic
parameters and the machine will automatically set
the wire feed speed (amps) and voltage based off
of the user input. The unit
’
s programming is easily
overridden and the welder will remember the new
ratio of voltage to wire feed setting during the ac-
tive welding session until the process is changed, or
until the Synergic mode is deselected. The machine
has three synergic modes, one for standard MIG
operation, one for standard Spool gun operation
and one for standard push
-
pull gun operation. If a
setting is found that is desirable, be sure to save it
under a program number and record it, or the
settings will be lost once you leave the welding
session/mode.
7)
Pulse TIG Mode.
The pulse TIG feature can be em-
ployed to control heat, wicking of the puddle and
reduce the arc cone diameter, improving the di-
rectability of the arc. The Pulse TIG mode allows
the setting of Pulse Amps, Pulse Frequency, and
Pulse Time
-
On. Each features serves to change and
shape the welding arc and puddle to control heat,
wet
-
in and penetration.
8)
Pre and Post Flow Control.
The adjustable Pre and
Post flow control features are designed to improve
weld quality at the beginning and end of the weld
where porosity from oxidation can be a problem.
This is accomplished by providing adjustable time
controls for both pre flow and post flow of shield-
ing gas. This control is active for both MIG and TIG.
9)
MIG Start and Crater Fill (MIG End)
Feature im-
proves starts and starts, and helps prevent bead
cracking and porosity in 4T mode.
10)
Slow Run
-
in of Wire.
This feature improves arc
striking quality in MIG modes by helping prevent
arc stuttering (machine gunning) and push
-
off dur-
ing arc initiation by slowing the wire speed until
the arc is established.
Note: This feature does
prevent the user from taking accurate measure-
ments of wire feed speed manually as the wire
will feed slower until the arc is struck and main-
tained.
Adjustments to starting (upslope) may be
made to further improve the arc starting proper-
ties of this welder.
11)
Spool Gun Modes.
This welder is well equipped to
handle the aluminum welding needs of most cus-
tomers by being both spool gun ready. The unit
can handle several different Everlast spool gun
models, but the best is the 300 amp, Parker® DSP
360A spool gun. Also the user may want to consid-
er the Everlast SM200N
-
MTS gun which is a 200+
Amp gun with a 24 series barrel. A spool gun is an
economical choice for light to heavy applications
requiring a fast deposition rate of aluminum on
materials
3/16”
or greater in thickness. A spool
gun is limited to
4”
rolls (usually holding 1 lb of
aluminum and 2 lbs of other filler metals) so nu-
merous spools may be needed on larger projects
.
Note: This unit does not support push
-
pull gun
operation. It only supports spool gun operation.
Section 1
Introduction and Specifications