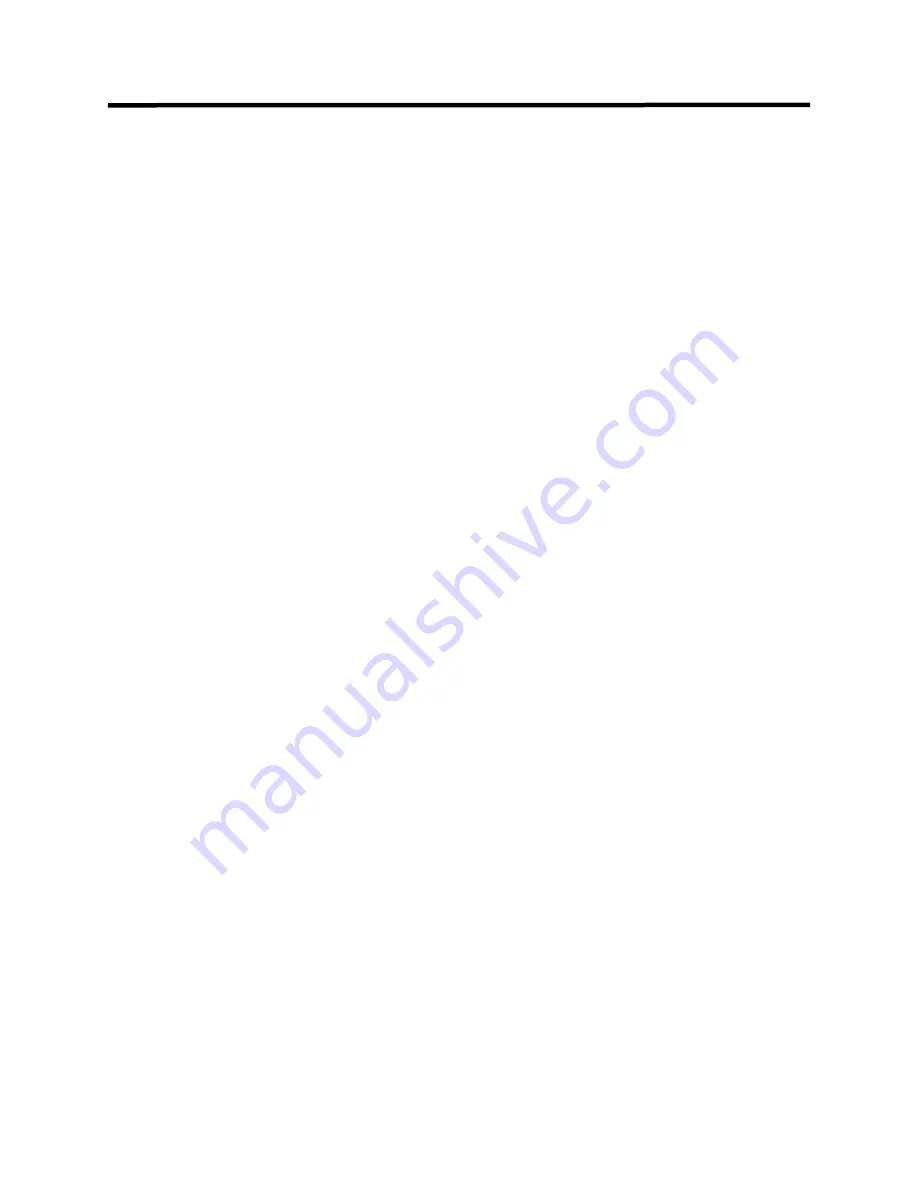
33
good for light gauge metals and offers great con-
trol and good bead profile qualities on thin gauge
metals. The way the wave form is shaped, it
spends the least amount of time fully
“
on
”
at the
peaks, so output will seem reduced and even the
meter may show a lower top end output. How-
ever, due to the way the wave form is shaped, in
laymen
’
s terms, the meter reads a lower output
than actual computed output.
This is normal.
Generally, given the fact that the triangular wave
form is intended for lighter gauge metals, the
“
cooler
”
feel of the arc will not be an issue.
Additional features located within the Sequencer.
1.
MIG Inductance.
(Located on the far left side of
the Sequencer Graph.)
Varies the current
-
rise
time while welding after the arc shorts to the
puddle during the short
-
circuit transfer process.
This affects the actual physical point where the
current has risen sufficiently to melt back the
wire, subsequently pinching off and depositing in
the puddle. The physical point at which the wire
has burned back is considered the
“
pinch point
”
of the arc. This is where the wire will melt back
to before transferring the wire back to the pud-
dle to once again short out. To put it in more
practical terms, the user will see that the wire is
sticking out longer or shorter from the MIG torch
before it burns away, depending upon the exact
setting. This controls spatter, penetration and
bead profile. When the arc force knob is rotated
from one extreme to the other, the operator will
observe that the arc is more stiff at one end or
more fluid at the other end. Bead profile chang-
es will occur as well. A stiffer arc will produce a
deeper but more narrow profile. A fluid arc will
produce a wider, shallower weld, usually with an
improved bead appearance and less spatter. Arc
force control is also known as inductance con-
trol, slope or wave form control (MIG). By
changing the level of inductance, the user can
fine tune the arc performance so the welder re-
sponds in a manner that the user is accustomed
to with other brands of machines. The arc
sound will also change as the arc force is adjust-
ed, going from a relatively high pitched whine to
a frying sizzle. All MIGs, regardless of brand,
without an adjustable arc force, do have some
fixed level of inductance, though not all are set
at the same level. A user can either adjust the
inductance to have a familiar feel, or to improve
arc behavior whenever welding position or con-
dition change. This control is primarily useful for
short circuit welding and has limited value in Axial
Spray. While using many types of flux core or dual
shield, manufacturers will often specify a setting of
“0”,
though
“0”
is a relative value, and inductance
cannot be completely eliminated. In MIG, exces-
sive or too little amounts of inductance can create
a violent arc or an unstable one, so be careful
about selecting too much or too little. A good
starting point is around 60 or 70%. Make gradual,
changes to fine tune the inductance. Giant swings
will make other parameters harder to dial in
properly as the inductance can greatly affect the
feel of welding arc in both modes. Set the amount
of inductance to the approximate level desired
before tuning other parameters (whether you are
in standard or pulse modes). Do not attempt to
further alter inductance until all other parameters
are fine tuned as much as possible. After Volt and
Amp adjustments are tuned to the best setting you
can achieve, then fine tune the inductance level as
the final stage of MIG adjustment.
2.
Burn Back Timer Control.
(Located vertically on the
Sequencer Graph.)
The burn back timer controls
the amount of time that the arc stays engaged
after
the trigger is released and the wire feeding
stops. This is to help reduce wire stick out and
reduce the need to trim the wire before starting
another weld. This also serves to prevent the wire
from sticking in the weld puddle once the arc is
stopped. For best results this should be used with
the Post flow feature so that the wire does not
become oxidized during the burn back phase. If too
much burn back is used, the wire may burn back up
into the tip. Increase burn back by only a tenth of a
second at a time to prevent over adjusting the burn
back and destroying the contact tip. Generally
burn back control will produce consistent results
and increase production. Different wire diameters
and feed rates will change the burn back time re-
quirement. Keep in mind burn back control is an-
other tool designed to help increase quality and
ease of welding. Time can be set at
“0.0”
without
severely affecting weld quality.
3.
Pre
-
Flow and Post
-
Flow of Shielding Gas.
Both
Pre flow and Post flow are functional in the MIG
and TIG welding processes. However, many MIG
welders do not provide Pre and Post flow of shield-
ing gas. This is one reason that some professionals
do not consider MIG for high quality welds, where
porosity must be minimized. However, by provid-
ing a Pre
-
flow and Post
-
flow of shielding gas in MIG
Setup Guide and Component Identification
Section 2