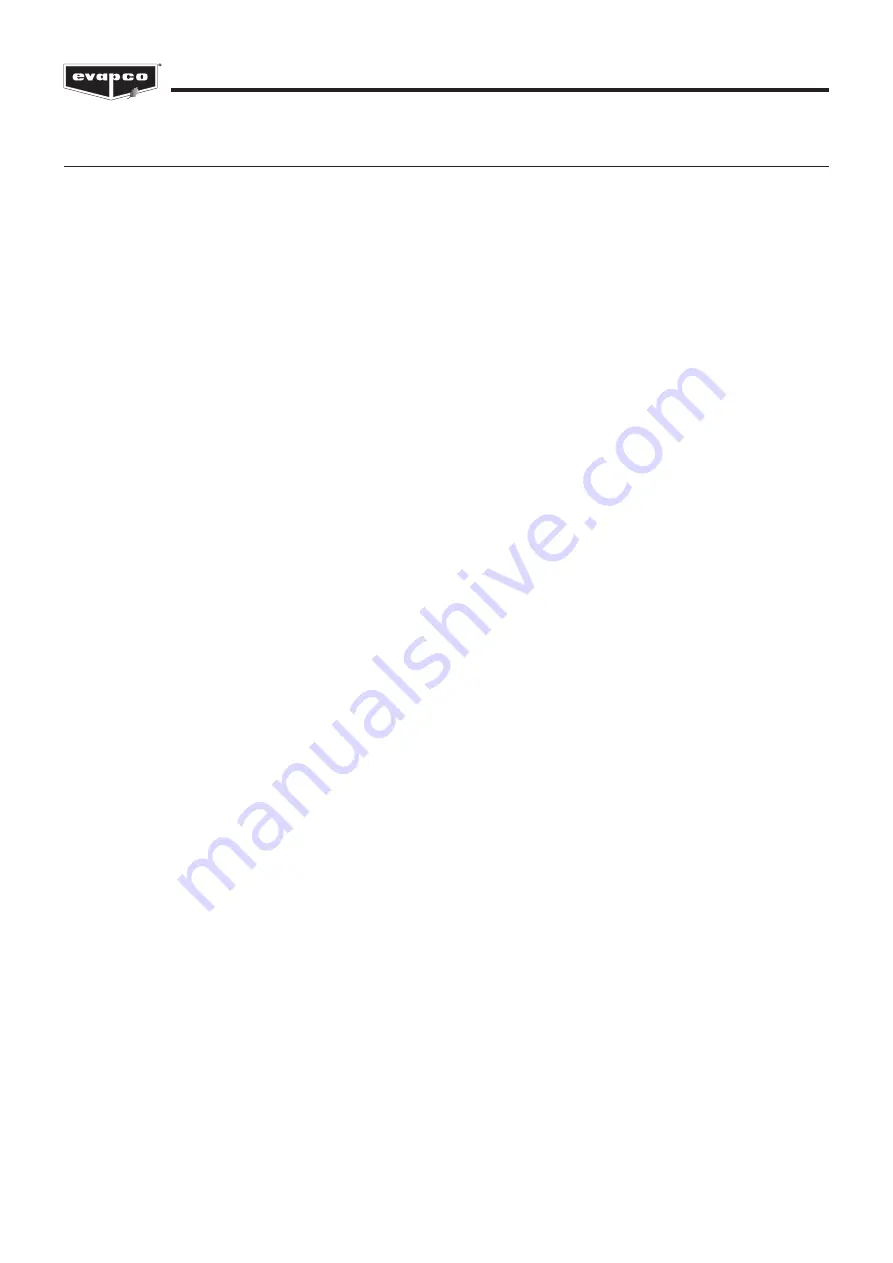
8
PHC PARALLEL HYBRID EVAPORATIVE CONDENSERS
Final Assembly & Startup Details
Shipping Materials
Remove any wood chocks, spare parts, or miscellaneous items that have been placed inside the unit for shipping purposes. Clean all
debris from the basin.
Pump Discharge Line
Connect the riser pipe from the pump discharge on the basin section to the riser pipe on the coil / fan section using the flexible
connection and hose clamps provided.
Makeup Water Line
Connect (plumb) the makeup water source to the makeup water connection on the unit. The makeup water supply pressure to the
unit should be maintained between 20 and 50 psig (140 kPa and 340 kPa). Water supply pressure in excess of 50 psig (340 kPa) may
damage the mechanical float valve.
Bleed or Blowdown
EVAPCO recommends an automated conductivity controller to maximize the water efficiency of your system. Based on
recommendations from the selected water treatment company, the conductivity controller should open and close a motorized ball or
solenoid valve to maintain the conductivity of the recirculating water. If the manual valve provided in the bleed-off line on a unit with
factory supplied pump(s) is used to control the rate of bleed, it should be set to maintain the conductivity of the recirculating water
during periods of peak load at the maximum level recommended by the selected water treatment company. If no direction is provided,
the valve should be fully open. On units shipped without a pump (remote sump applications), the bleed-off arrangement and valve
must be provided by the customer.
Float Valve Adjustment
The float valve is preset at the factory however adjustment should be checked after rigging. The float valve should be adjusted so that
the center of the float is 1” below the center of the overflow connection when the valve is in the fully closed position. Raise or lower the
float by using the wing nuts on the vertical threaded rod. Do not adjust the horizontal rod.
During normal operation, the water level will drop 3” (76 mm) to 4” (102 mm) below the overflow.
Strainer
Check the strainer in the basin to ensure that it is in its proper location over the pump suction.
Screens
Protective screens are provided across the top of the fan cylinders on all models. Inspect the screens to ensure there are no gaps that
may present a safety hazard. Check all screen fasteners to ensure they are tight and secure.
Fan Rotation
Bump start and check the fans for proper rotation. Directional arrows are placed on the inside of the axial fan cylinders.
Pump Rotation
After filling the basin to the overflow with fresh water, bump start and check the pump for proper rotation. Directional arrows are found
on the pump impeller housing.
Do not start pumps prior to filling the basin with water. Dry pump operation will damage the pump
seals.
Maintenance
Once installation is complete and the unit is turned on, it is important that it be properly maintained. Maintenance is not difficult or
time consuming but must be done regularly to assure maximum trouble free performance of the unit. Refer to the “Operation and
Maintenance Instructions” bulletin enclosed with the unit for proper maintenance procedures.
Also, proper freeze protection must be provided if the unit is located in a cold climate. Refer to the “Operation and Maintenance
Instructions” bulletin supplied as well as factory product bulletins for further information.