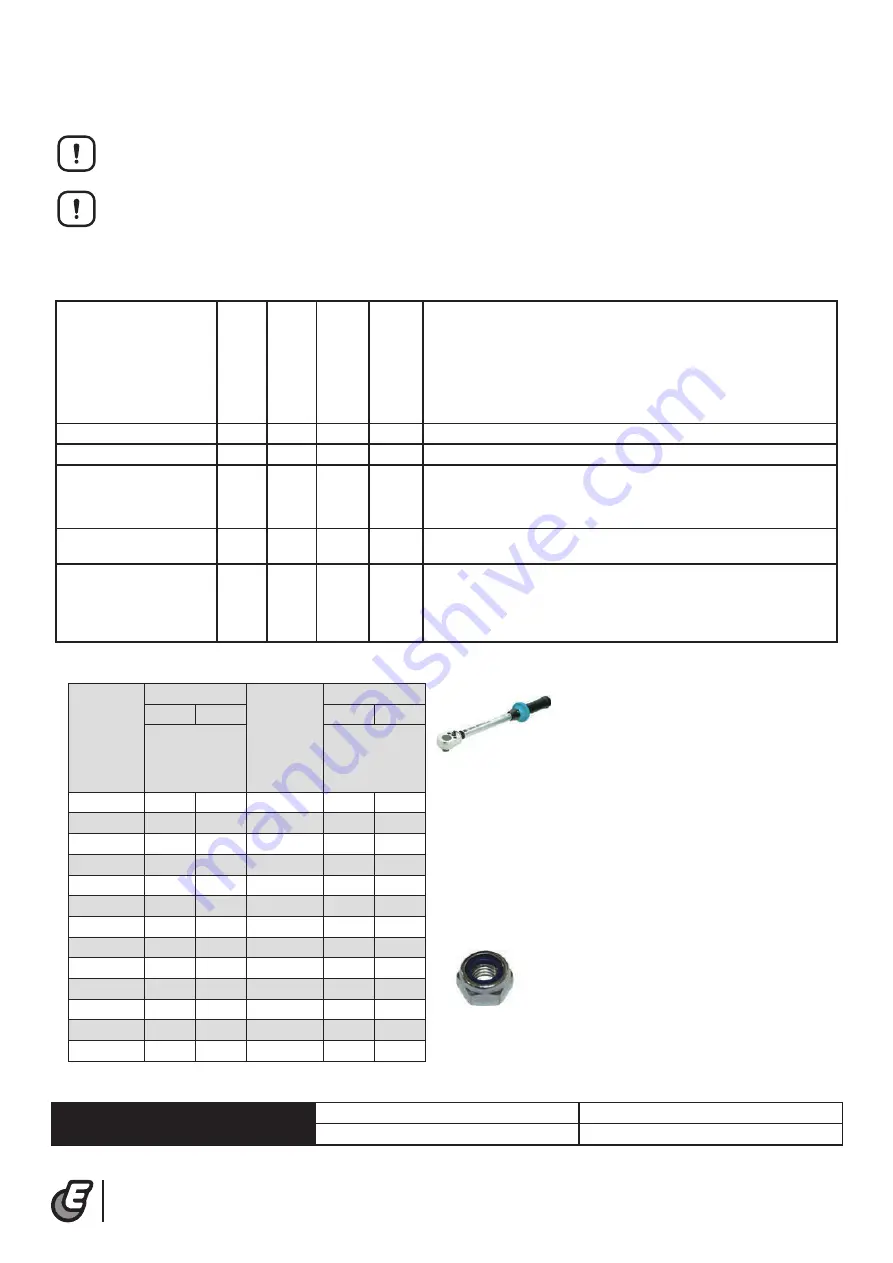
LAMPO Multifunction Unit
Nature and frequency of periodic maintenance operations.
To ensure the correct operation of the machine, it is useful and appropriate to schedule a general maintenance at least once a year. This operation has
the purpose of preventing extraordinary maintenance operations with consequent machine downtime during the period of use. All mechanical, electrical,
pneumatic and hydraulic components must be checked. During the check all the parts that have defects or that may require short-term intervention must be
replaced. It is advisable to carry out a thorough cleaning of mechanical parts, motors and electrical panels.
Tampering/unauthorised replacement of one or more parts of the machine, the use of accessories, tools, consumables other than those recom-
mended by the Manufacturer, may represent a risk of injury and relieve the Manufacturer from civil and criminal liability.
The clothing of those who work or maintain the machine must comply with the essential safety requirements in force in your country, as defined by
Directives 89/656/EEC and 89/686/EEC concerning the use of personal protective equipment.
Attention should also be paid to bracelets, rings or necklaces that must not dangle or hinder the movements of the operator: in this regard, it is appropriate
not to wear such accessories in order to reach the highest possible level of safety.
5.5.1 CARRIAGE SECTION
Component
aft
er the fir
st 50 km
500 km or
once a month
2000 km or
ev
ery 3 months
5000 km or
ev
ery 6 months
Tyre pressure
X
X
•
Check of tyre pressure
Tightening screws
X
X
•
Check the tightness of wheel nuts, tighten if required.
Tyre wear, wheels
X
•
Ageing status of tyres (e.g. cracks, porous areas).
•
Measure the tyre profile depth at the centre of tyres.
•
Check the rims for visible damage (concentricity, coupling), invert the
wheels per axle / in pair or repair them.
Support wheel, supporting
feet
X
•
Check operation and stability.
•
Lubricate the moving parts.
Fixing screws
X
•
Check all the fixing screws for a constant connection (see tightening
torque table).
•
Carefully check the screw connection in the frame area.
•
Tighten immediately the loose connections.
•
Replace screw connections when they are worn / corroded.
5.5.1.1
SCREW TIGHTENING VALUES
Dimensions
Class
Dimensions
Class
Use torque wrenches to secure screw connectors
8.8
10.9
8.8
10.9
Tightening
torque (Nm)
Tightening
torque (Nm)
M 5
5.5
8.1
M 20
425
610
Set the maximum tightening torque of the torque wrench
M 6
9.6
14
M 20 X1.5
475
980
M 8
23
34
M 22
580
820
M 8X1
25
37
M 22 X1.5
630
900
M 10
46
67
M 24
730
1050
M 10X1.25
49
71
M 24X2
800
1150
M 12
79
115
M 27
1100
1550
M 12X1.5
83
120
M 27X2
1150
1650
Use self-locking nuts only once, as the tightening
force of the plastic ring is reduced if reused
M 14
125
185
M 30
1400
2000
M 14X1.5
135
200
M 30X2
1500
2150
M 16
195
290
M 36
2450
3500
M 16X1.5
210
310
M 36X2
2650
3780
Replace the self-locking nuts once the screw connection has been opened
M 18
300
430
M 42
3930
5600
5.5.1.2 TYRE PRESSURE
TYRE
10.0/75-15.3 PR10
11.5_80-15.3 PR12
PRESSURE (bar)
5.1
5.3
38
Summary of Contents for LAMPO GREEN
Page 2: ......