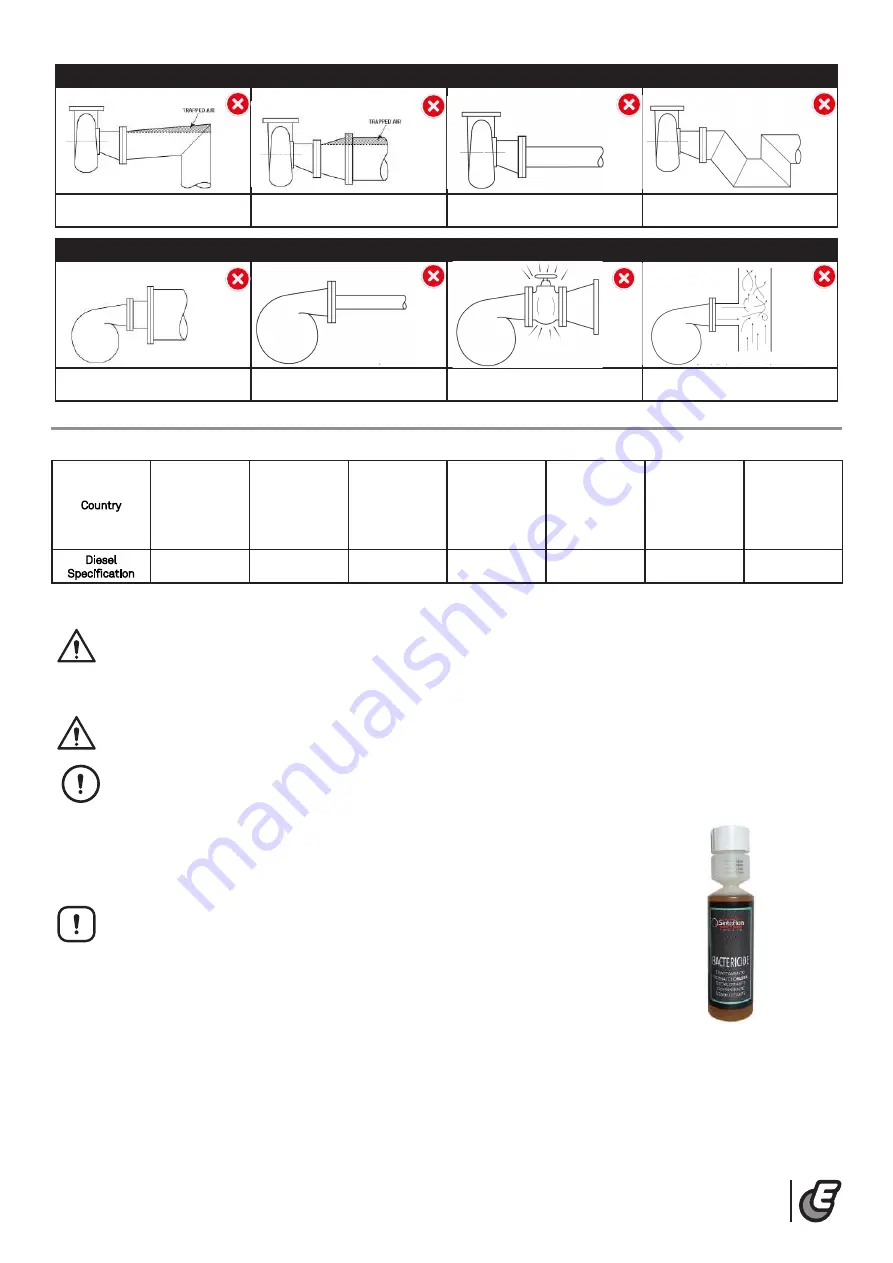
LAMPO Multifunction Unit
SUCTION
Do not tilt the pipes towards the
pump
Do not use concentric reduction
units
Do not choke water flow
Do not use too many fittings
DELIVERY
Avoid sudden changes in the pipe
diameter
Do not use small pipes, drain valves
or fittings
Do not design a system to operate
with the drain valve partially closed
Avoid using “T-shaped” branches in
delivery
3.4 SUPPLY
The machine is supplied with DIESEL fuel
Diesel fuel must comply with the specifications below. The table lists several specifications for diesel fuel worldwide.
Country
U
SA
EU
Int
er
na
tional
Unit
ed
King
dom
Japan
K
or
ea
China
Diesel
Specification
No. 2-D, No. 1-D,
ASTM D975-94
EN590:2017
ISO 8217 DMX
BS 2869-
A1 or A2
JIS K2204
Grade No. 2
KSM-2610
GB252
In some conditions diesel fuel can be flammable and explosive.
Fill the fuel tank with diesel fuel only. Filling the tank with petrol can cause fire and damage the engine.
For no reason it is allowed to smoke and/or use open flames near the machine during refuelling.
Clean all fuel leaks immediately.
Never overfill the fuel tank.
Refuelling operations must be carried out only with machine off
Keep all containers containing fuel in a well ventilated area, away from any fuels or sources of ignition.
Failure to comply with these instructions can result in death or serious injury.
Avoid refuelling if fuel leaks are present.
The use of diesel with a high percentage of Bio-Diesel may seriously damage the engine.
The prolonged stop and sudden temperature changes may affect the characteristics of the diesel and/or
give rise to the formation of condensate inside the tanks.
The use of a bactericidal additive helps prevent the formation of bacteria, fungi and moulds, stabilises
the diesel and prevents its oxidation.
Euromacchine recommends the constant use of a bactericidal additive in the machine and in the Diesel
stocking tanks to prevent malfunctions and/or breakages.
To this end, Euromacchine suggests the product “SINTOFLON - BACTERICIDE”
19
Summary of Contents for LAMPO GREEN
Page 2: ......