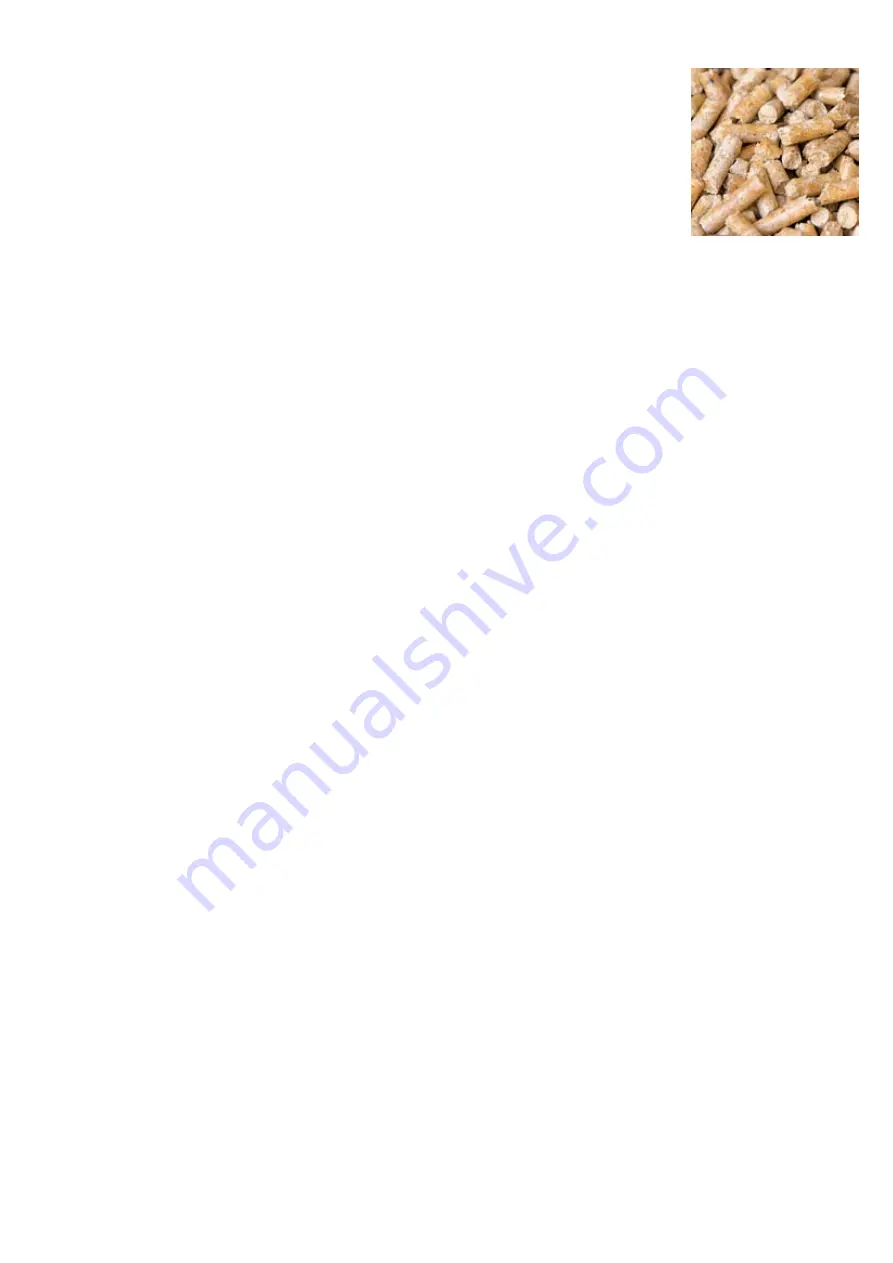
© EUROHEAT DISTRIBUTORS (H.B.S) LTD. July 2011
Instructions Part Number IN1232 Ed 1
7
Only pellets produced to ENplus standard are suitable for this appliance.
How can you recognise good quality wood pellets?
Good quality: the surface looks smooth with a semi-matt sheen, pellets of equal
length, no dust.
Lower quality: longitudinal cracks, high proportion of extremely long or short pellets,
high dust content.
How can we check the compaction quality of the pellets quickly and approximately?
Put a handful of pellets into a glass of water.
Good quality: pellets sink; due to their high density compared with water.
Lower quality: pellets float; due to their low density compared with water.
Return Flow Temperature Control
A return flow temperature control is essential.The return flow temperature must be at least 55°C at the appliance
return flow connection (optimum value 60°C), otherwise soot and tar formation, with resulting corrosion, can
occur. Euroheat offer special connection assemblies for this purpose which can be positioned inside or outside
the boiler. Details can be found in the separate installation instructions.
Buffer Cylinder/Accumulator
A buffer cylinder/accumulator is essential for efficient operation of this appliance. By using a buffer cylinder/
accumulator, the boiler can always be operated in the optimum output range, thus minimising consumption
and pollutant emissions. This also extends the service life of the system and wearing parts. The minimum size
of the cylinder should be 9kW Evo Aqua 400L/15kW Evo Aqua 500L.
Buffer Sensors
We recommend installation with buffer sensors. The stoves operation is controlled via these sensors, one sensor
is mounted in the buffer top and one at the bottom. When the top sensor drops below a preset temperature,
normally 60°C, the stove starts to operate. When the lower sensor reaches a pre set temperature, normally
65°C, the stove stops operating.
Cleaning, Maintenance and Servicing
This appliance is a wood-fired boiler. Ash and soot accumulate when solid fuel is burnt, which means that
periodic cleaning and servicing is essential. If this is not carried out, faults can arise for which we cannot accept
any liability. Only a clean and correctly adjusted boiler is an efficient boiler. A coating of only 1 mm of dust on
the heat exchanger surfaces increases fuel consumption by approximately 7%.
Mains Voltage/Power Supply
230 VAC/50 Hz. Voltage fluctuations from -15% to +10% are admissible.
Visionconvey AIR Pellet Conveying System for EVO AQUA (suction conveying system)
The EVO AQUA boiler can be equipped or retrofitted with an automatic pellet conveying system which avoids
the need to top up the inbuilt hopper with pellets manually.
The design of the storage room, assembly and operation of this system are described in the separate technical
documentation accompanying the discharge system.